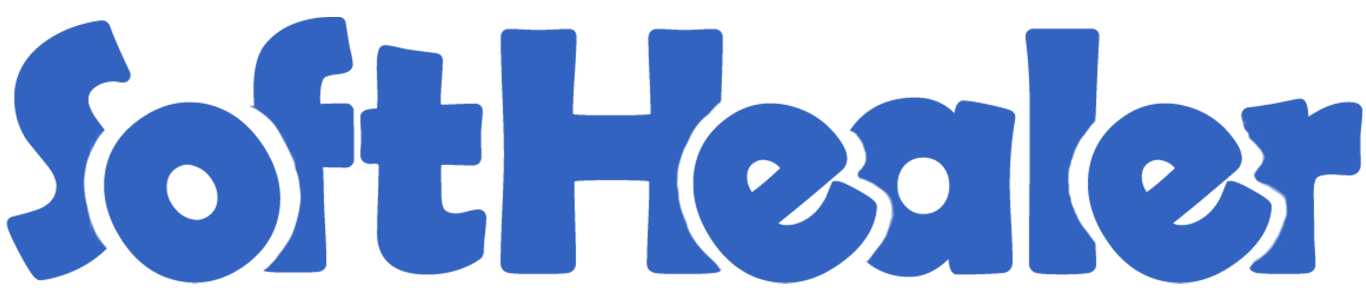
Quality Control Advance - Manufacturing, Work-Order, Inventory

Currently, in odoo, there are no options for 'Quality Control'. So, don't worry about that. Here we build a module that will help you to manage the quality of your products. Nowadays in the majority of businesses have Manufacturing, importing, exporting products. So you can receive goods(products) via transportation. Transportation increases the likelihood of goods being damaged. That's why you need to check product quality while you receiving or delivering products. Good quality control helps companies meet consumer demand with better products. This module will help you to analyze data of product quality checks.
Hot Features

Features

- There are two security groups for Quality Control 1. Manager 2. User
- Fully functional dashboard.
- Easy to set the team to manage a particular type of product.
- Easy to analyze product quality data using pivot and pdf reports.
- Easy to define the maximum number of quality checking. If you set '0' it means that the product quality checking has no limit.
- Set Quality Control mandatory for a particular product in a single click.
- Easy to create a quality point for required products.
- Easy to create quality alert stages with approver.
-
There are 4 different types of quality control...
- 1. Text: The quality controller will have to add a description(text) about product quality control.
- 2. Measurement: The quality controller will have to add the measurements as product quality.
- 3. Pass and Fail: The quality controller will have to just select the product quality that is passed or failed.
- 4. Take a Picture: The quality controller will have to add the pictures which represent the quality of the product.
-
There are different alert messages after quality check like...
- 1. Product Quality Control Passed.
- 2. Product Quality Control Failed.
- 3. Product Quality Control Still Pending.
- 4. Product Quality Control Complete with Some Products Partially Passed.
- Easy to do quality checking globally in operation form view. Also, you can perform quality checks manually from the operation line.
- Easy to do quality alert globally in operation form view. Also, you can perform quality alerts manually from the operation line for each product.
- Easy to access 'Quality Check' and 'Quality Alert' list into picking form view.
- This is user friendly. Users can access Pending QC, Passed QC, Partially Passed QC, Failed QC in a separate menu.
- Here you have pivot report for 'Quality Check' and 'Quality Alerts' for Inventory, Manufacturing, and Work Order.
- Easy to print PDF report of 'Quality Check' with different filters like product-wise, group by with picking the type, products, and with status also.
- Easy to print PDF report of 'Quality Alerts' with different filters like product-wise, responsible person, and stages.
- Easy to set email alias for quality alerts.
- This application fluently works with multiple companies.
User Config Setting: There are two different user config settings for
1. Manager 2. User.
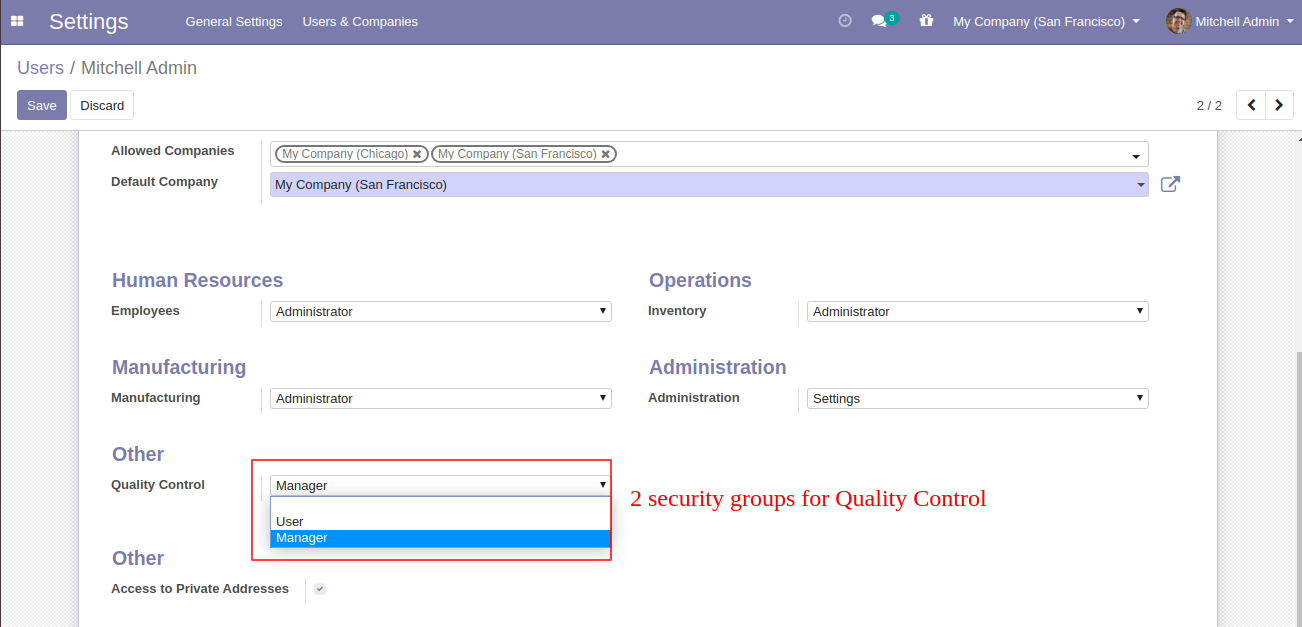
Quality Control Dashboard.
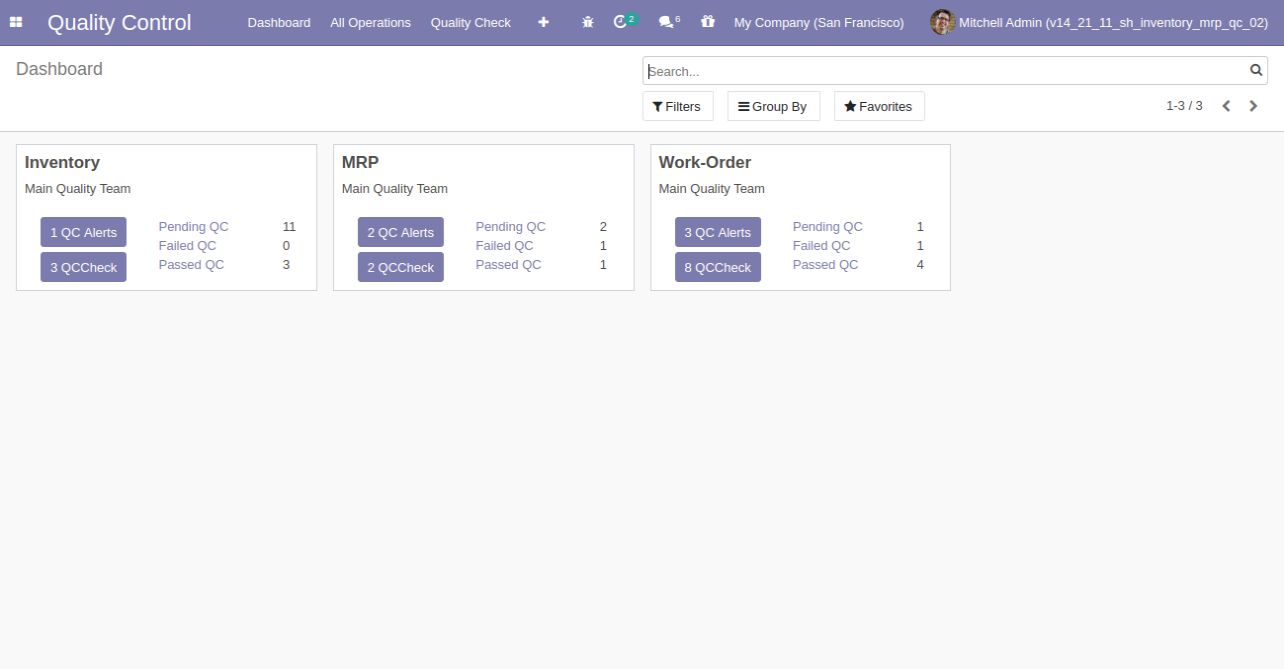
"Quality Team" Menu and Tree View.
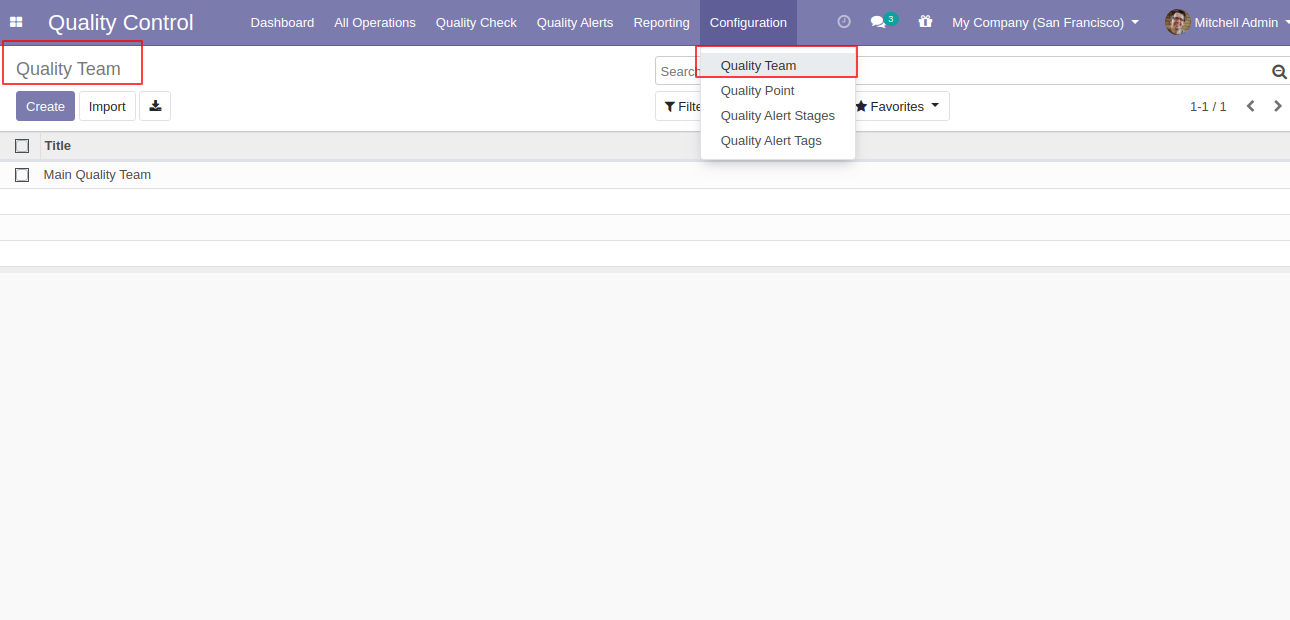
"Quality Team" Form View. Where you can define team members.
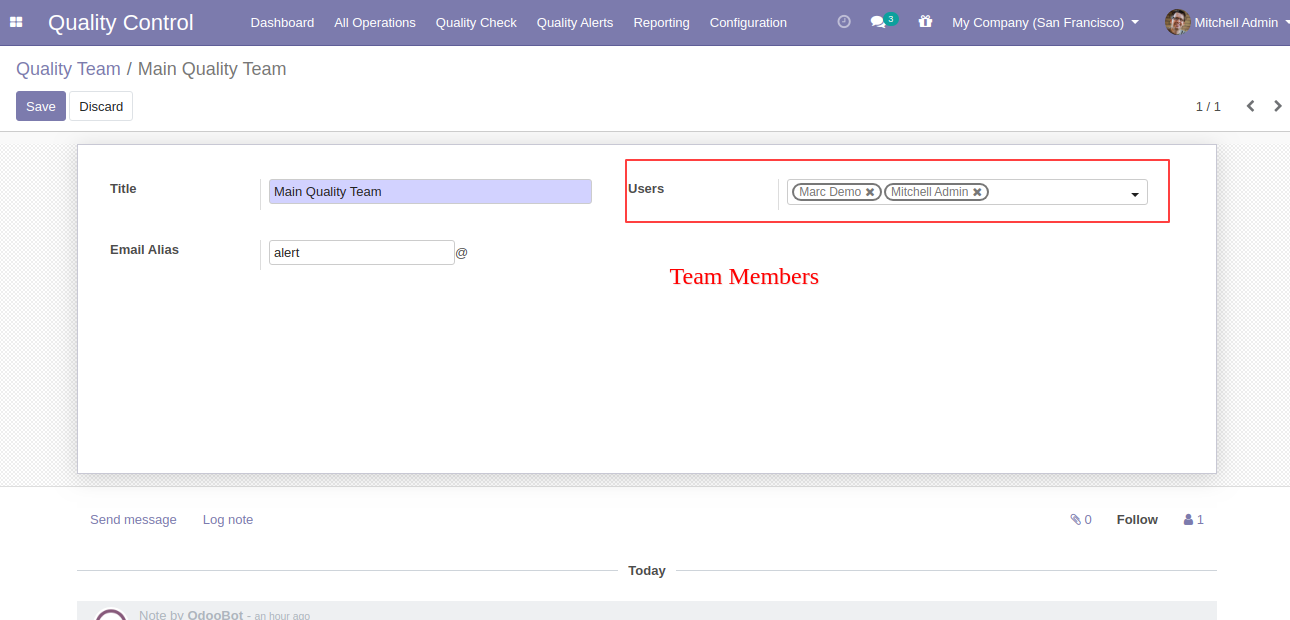
"Quality Points" Menu and Tree View.
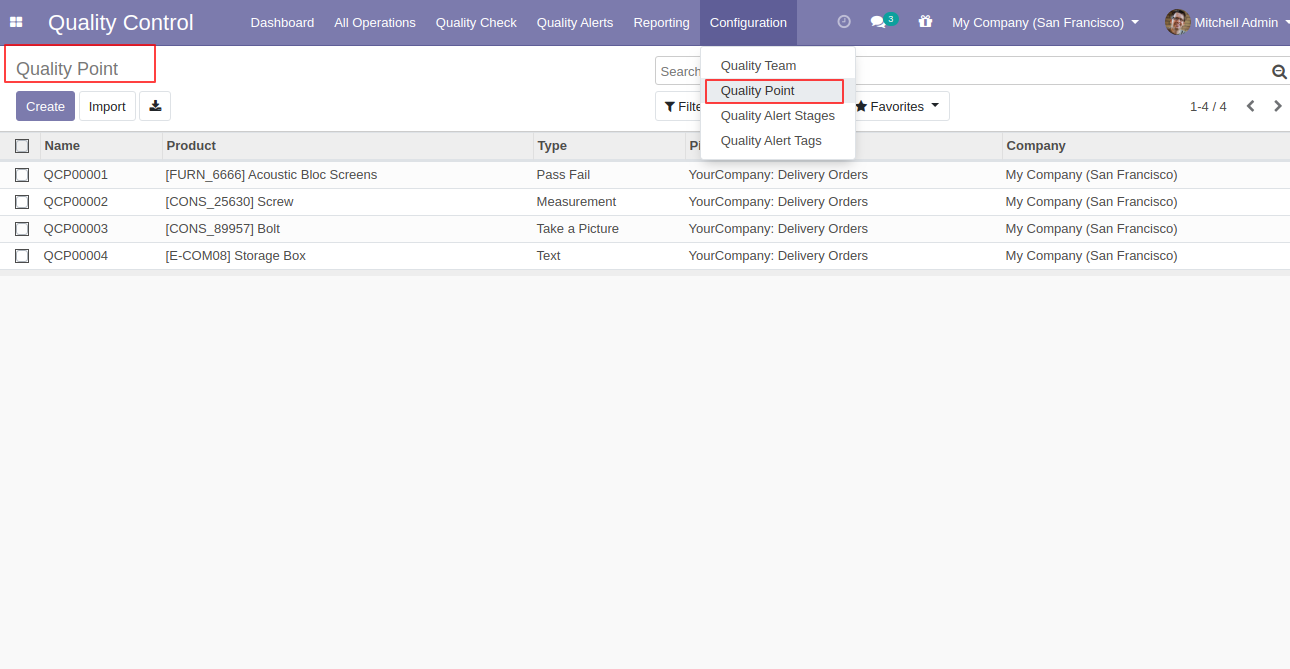
"Quality Points" Form View. Where you can define the quality points of each product with severals points.
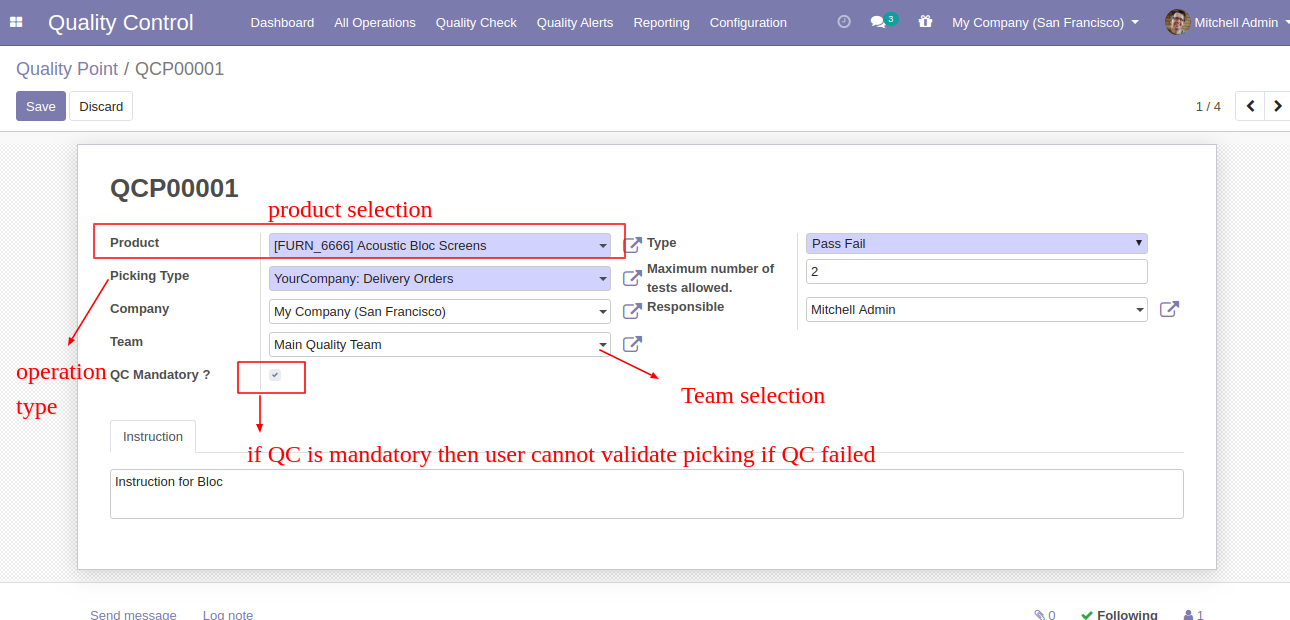
In quality points, here you can select the type of quality controls like 1. Pass or Fail.
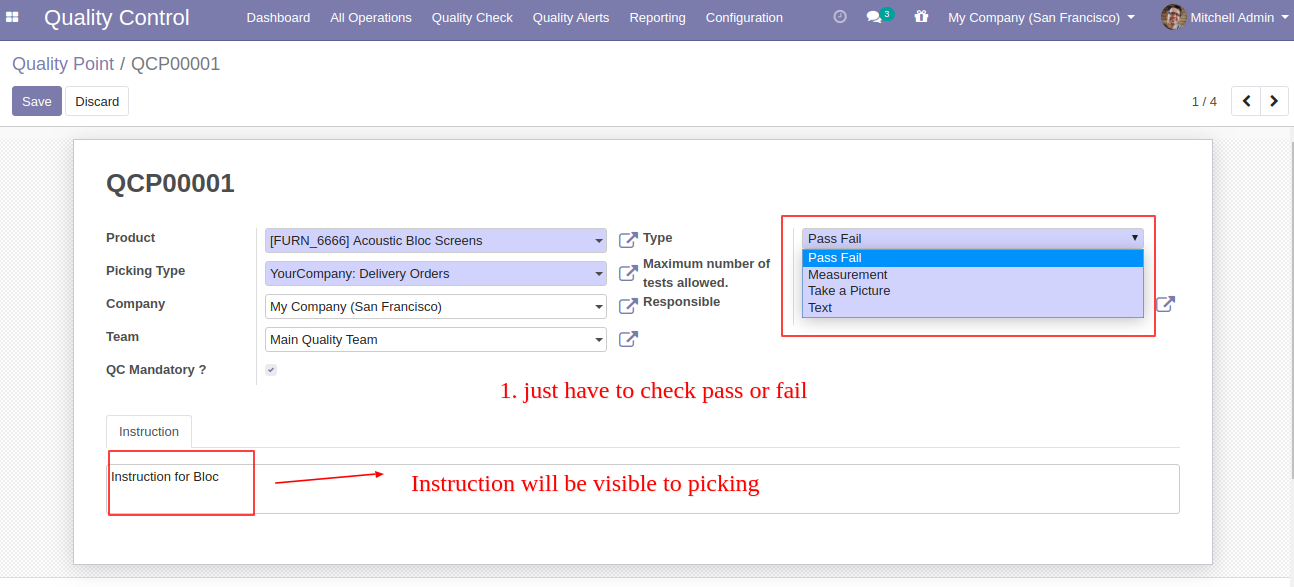
Quality Control Type 2. Measurements. In this type, you can define the tolerance level of products.
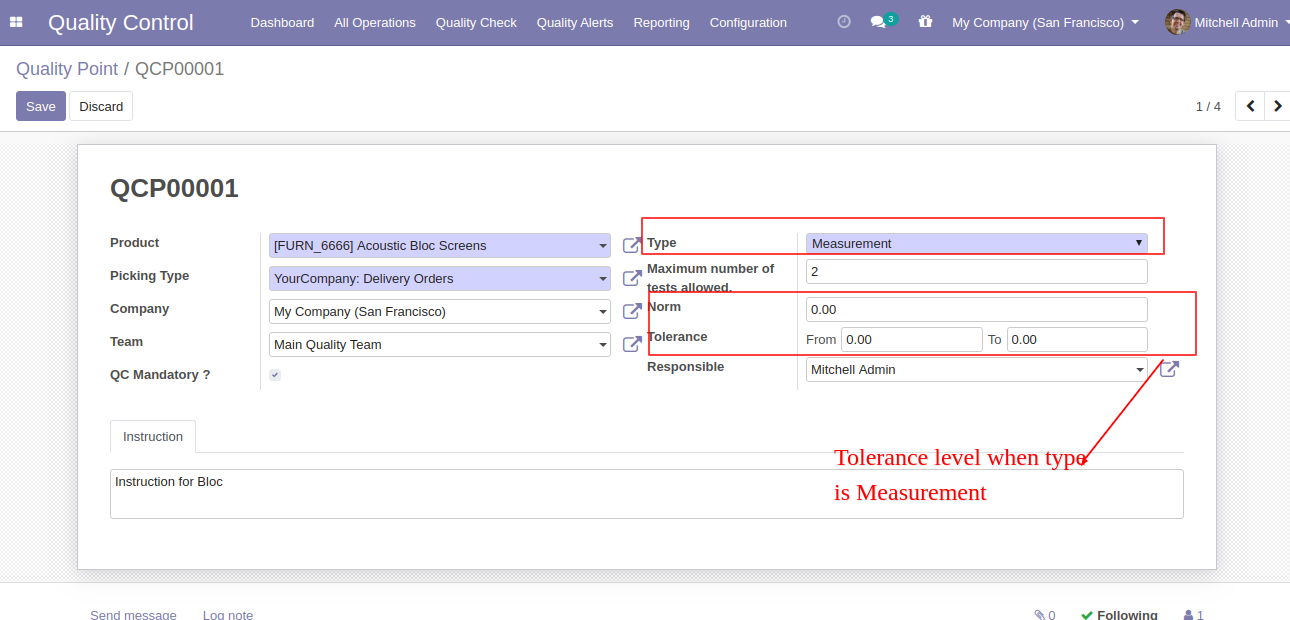
Quality Control Type 3. Take a Picture. This means a responsible person has to upload pictures of products while doing a quality check.
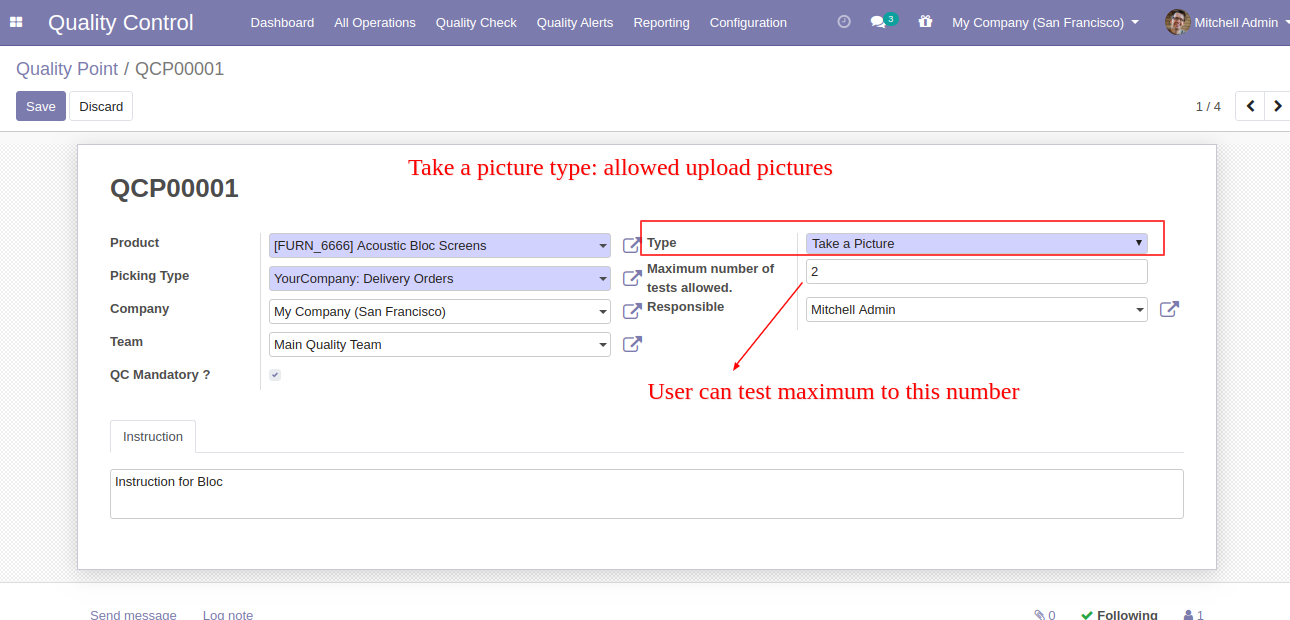
Quality Control Type 4. Text. This means a responsible person has to describe the quality of the product in only text.
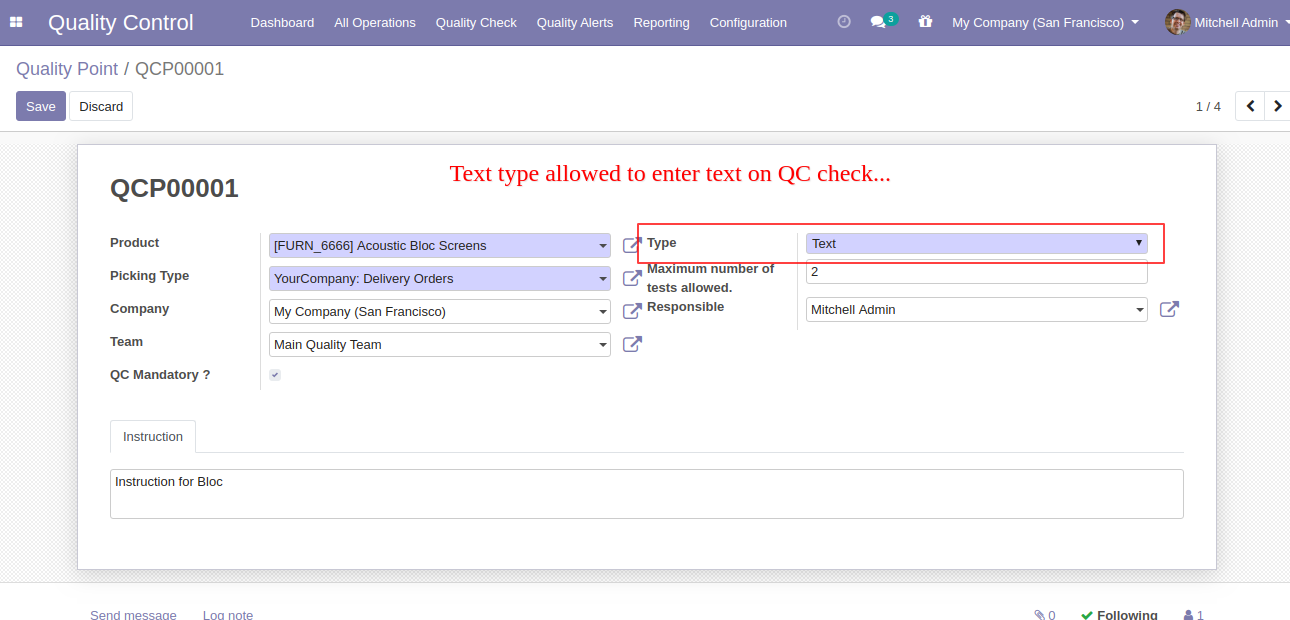
Quality Alert Stages Menu and Tree View.
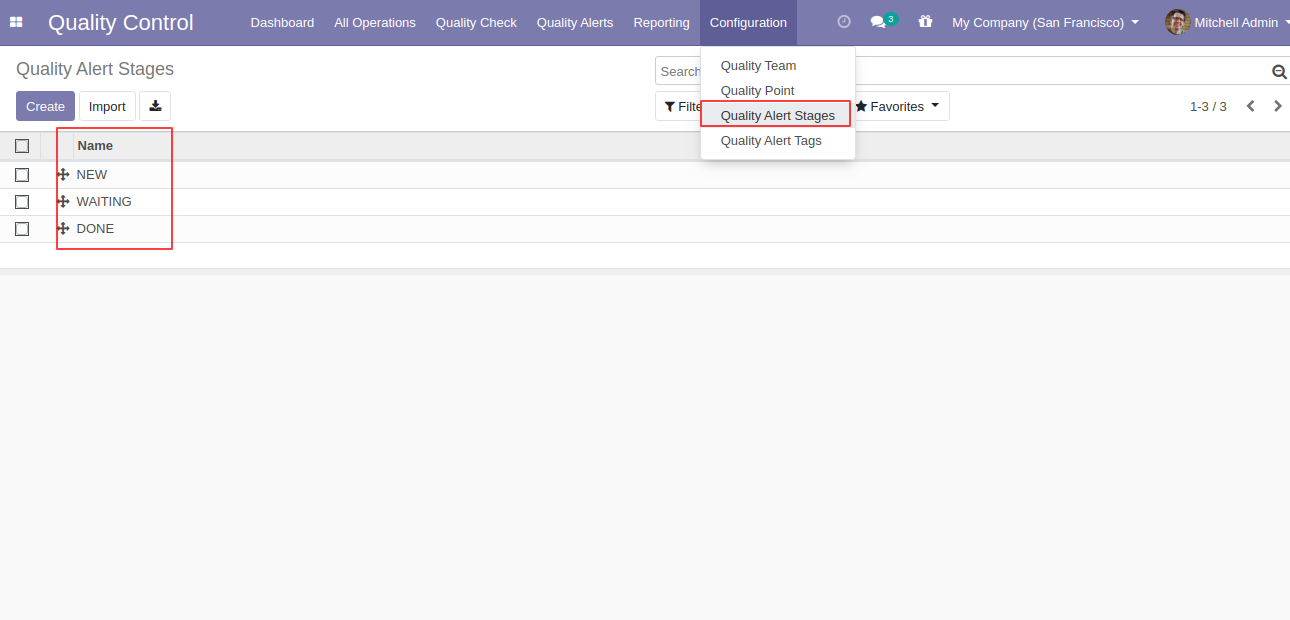
Quality Alert Stages Form View. Here you can define different stages of quality control with the responsible person and company also.
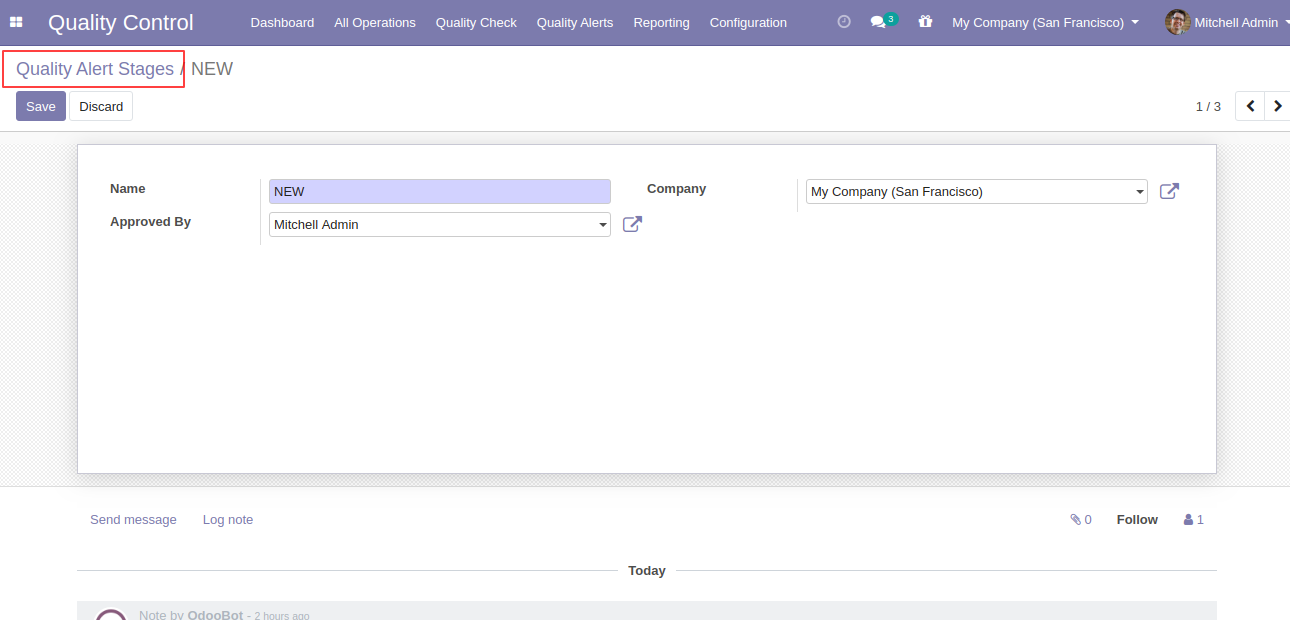
Quality Alert Tags Menu and Tree View.
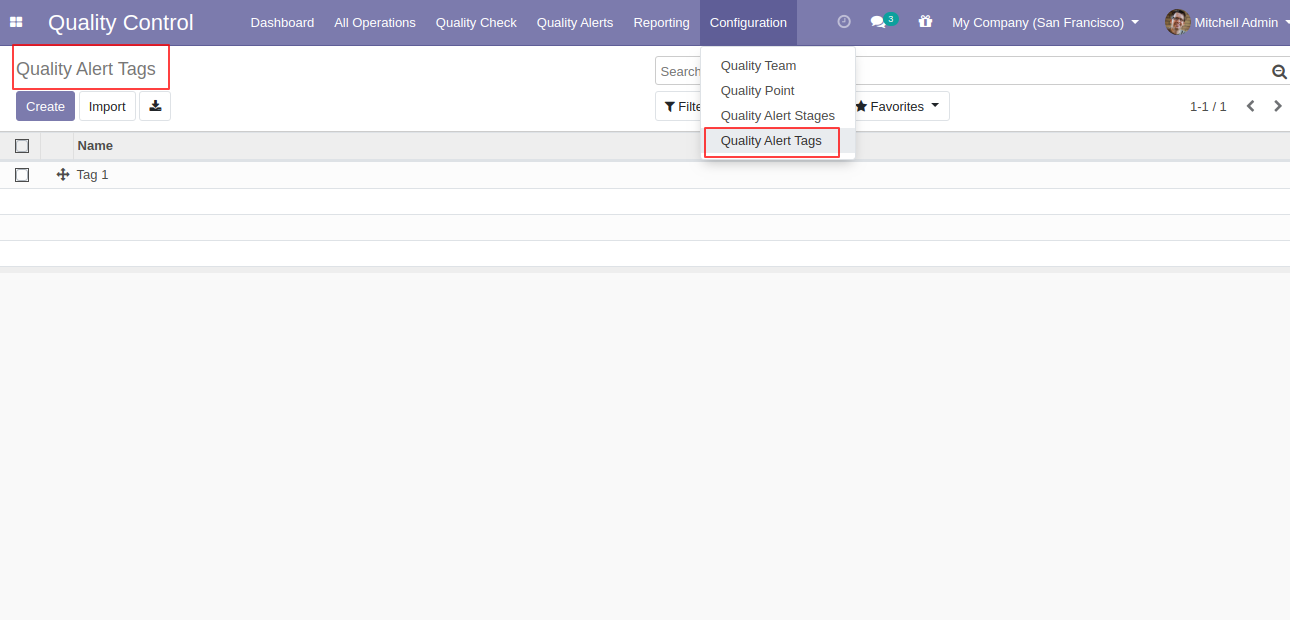
Quality Alert Tags Form View.
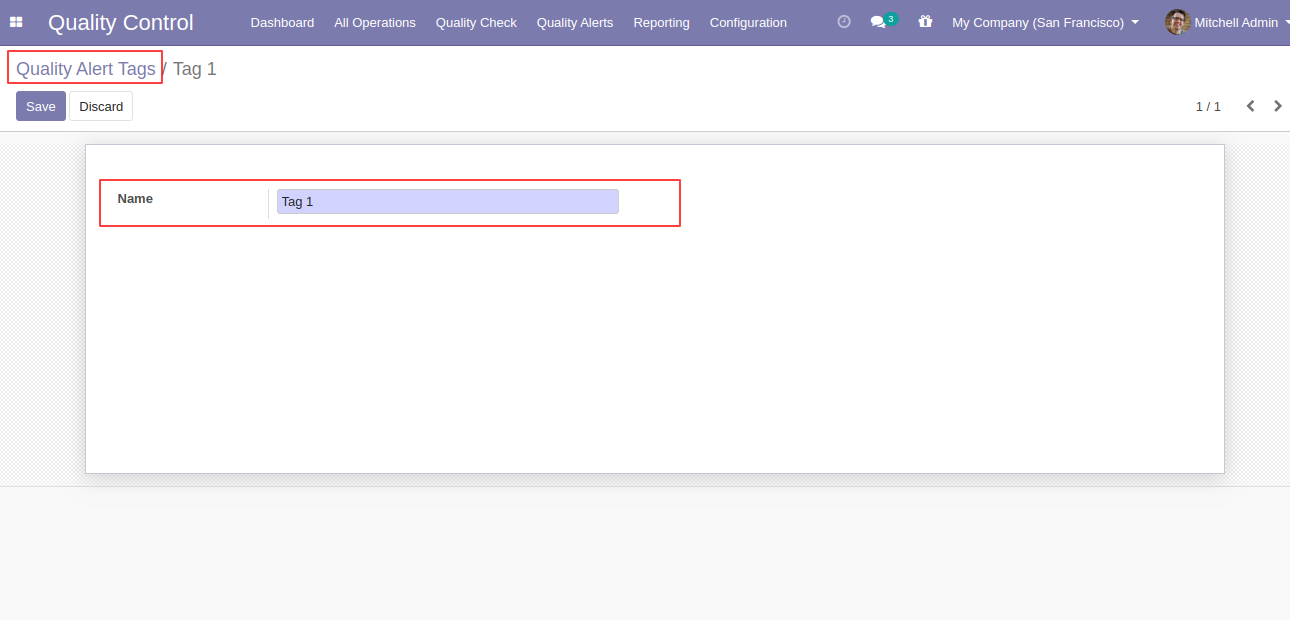
In the delivery order form view, there are two buttons "Quality Alerts" and "Quality Check", in operation lines you can see alert and check status, also see the global alert warning label on form top.
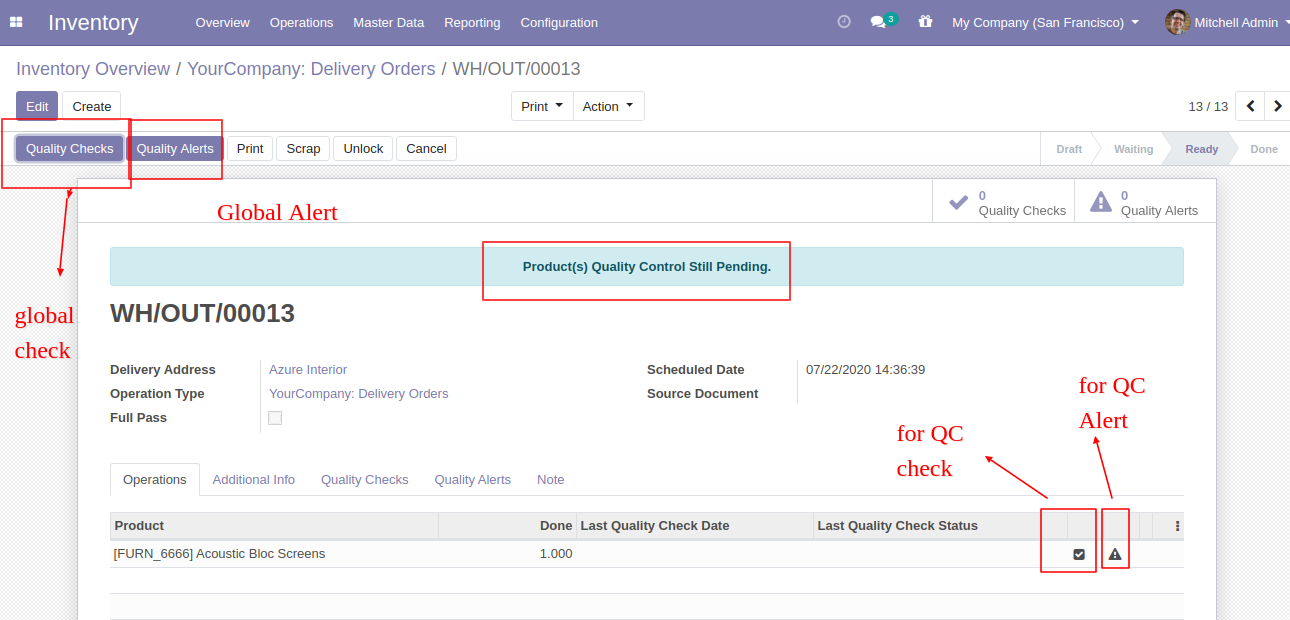
While clicking on "Quality Check" and check type "Text Only", In the wizard you have to add text and click Pass or Fail.
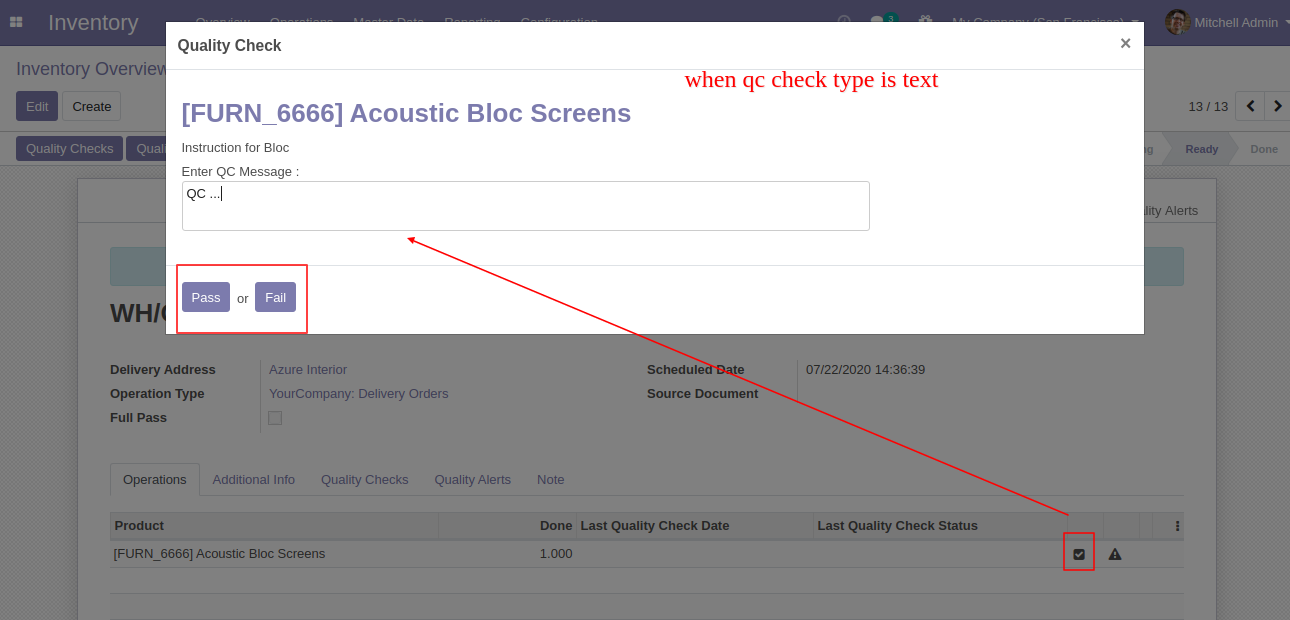
If Pass, Then that line will glow green and status is a pass.
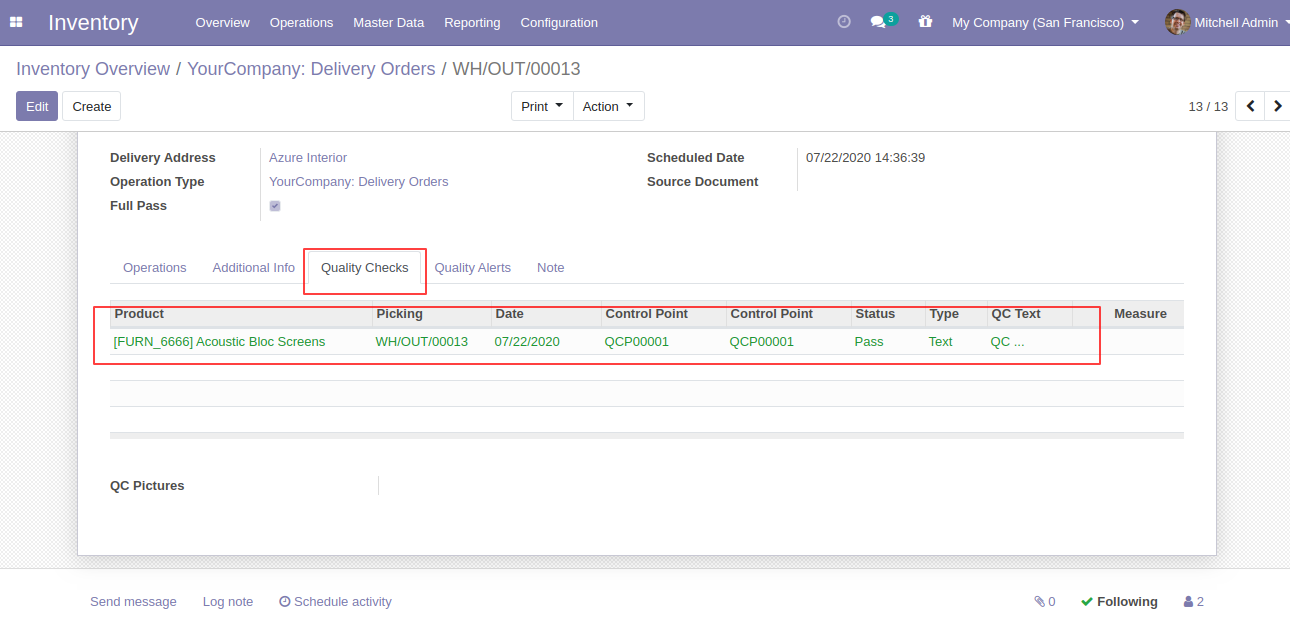
If in line more than one products and some products pending for QC than status is "Partially Passed QC"
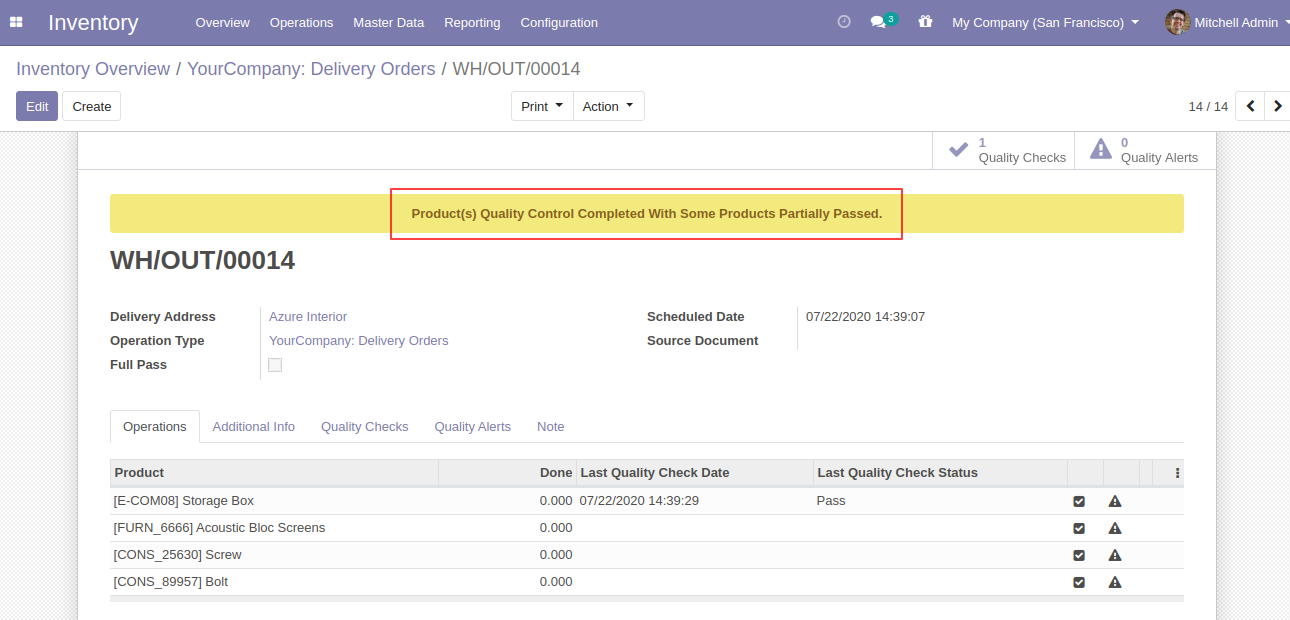
While clicking on "Quality Check" and check type "Measurement", In the wizard you have to add measurement in define criteria and click validate.
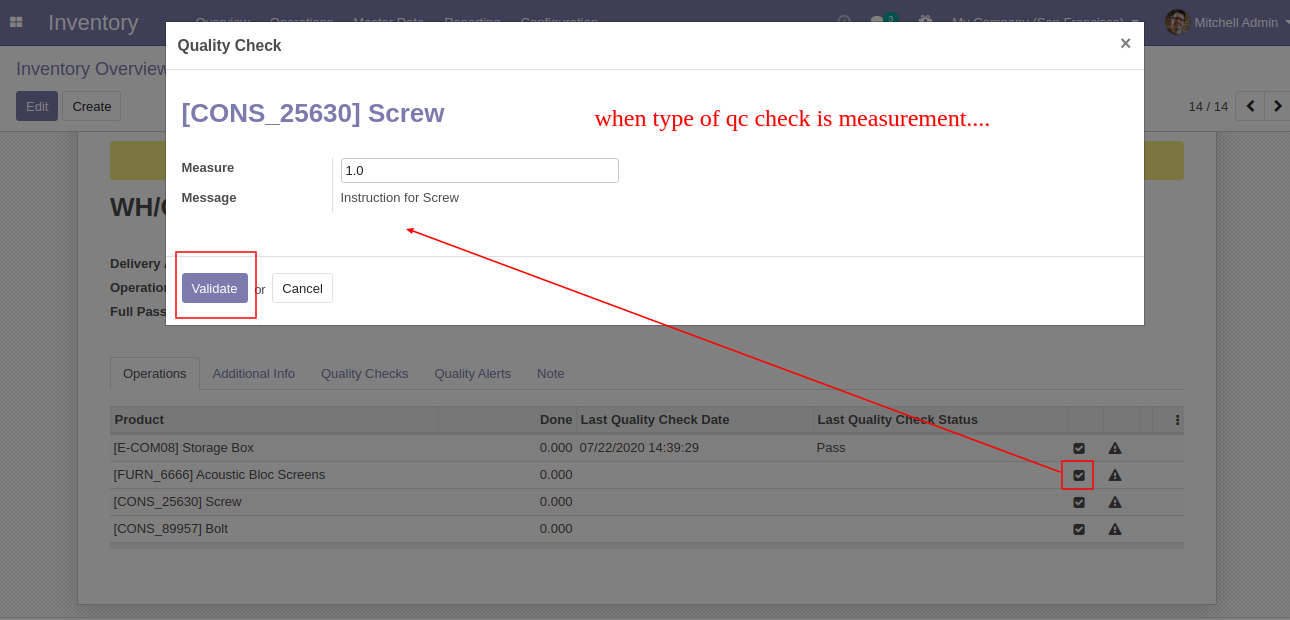
If enter measurement does not match criteria then it will popup this message where you have to select, If enter measurement is correct then click 'Confirm Measure' else click 'Correct Measure' and it will redirect to you on the previous popup.
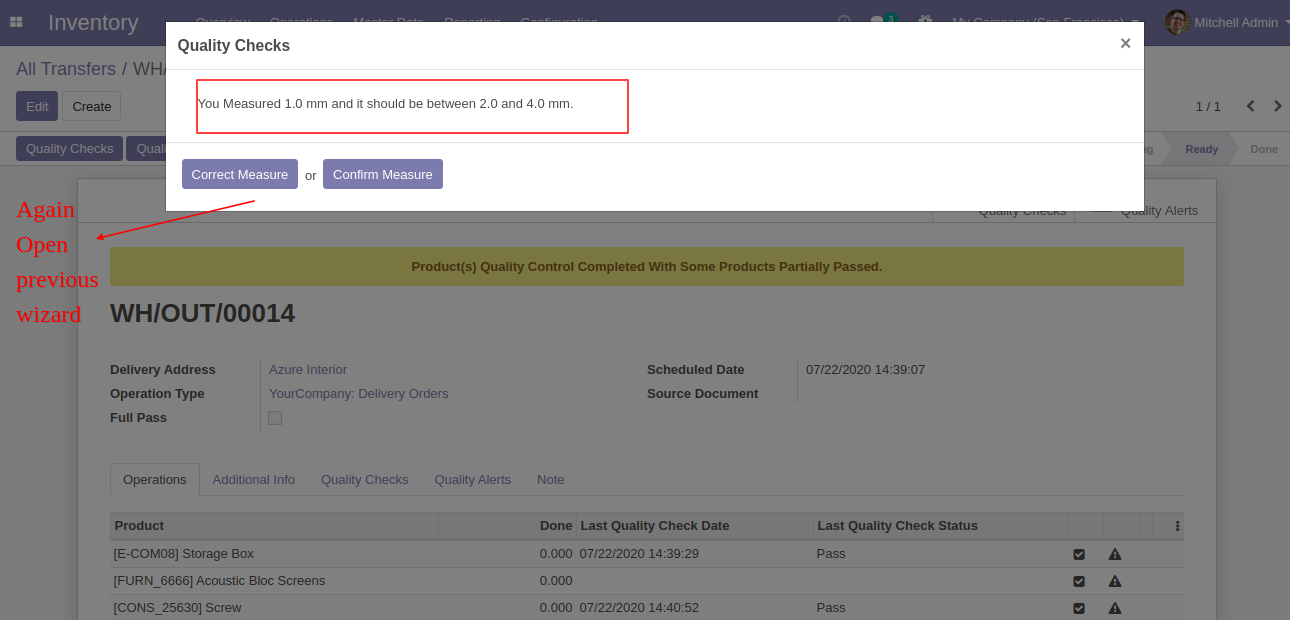
If Quality Check Type "Pass or Fail", Then responsible person has to click only pass or fail button.
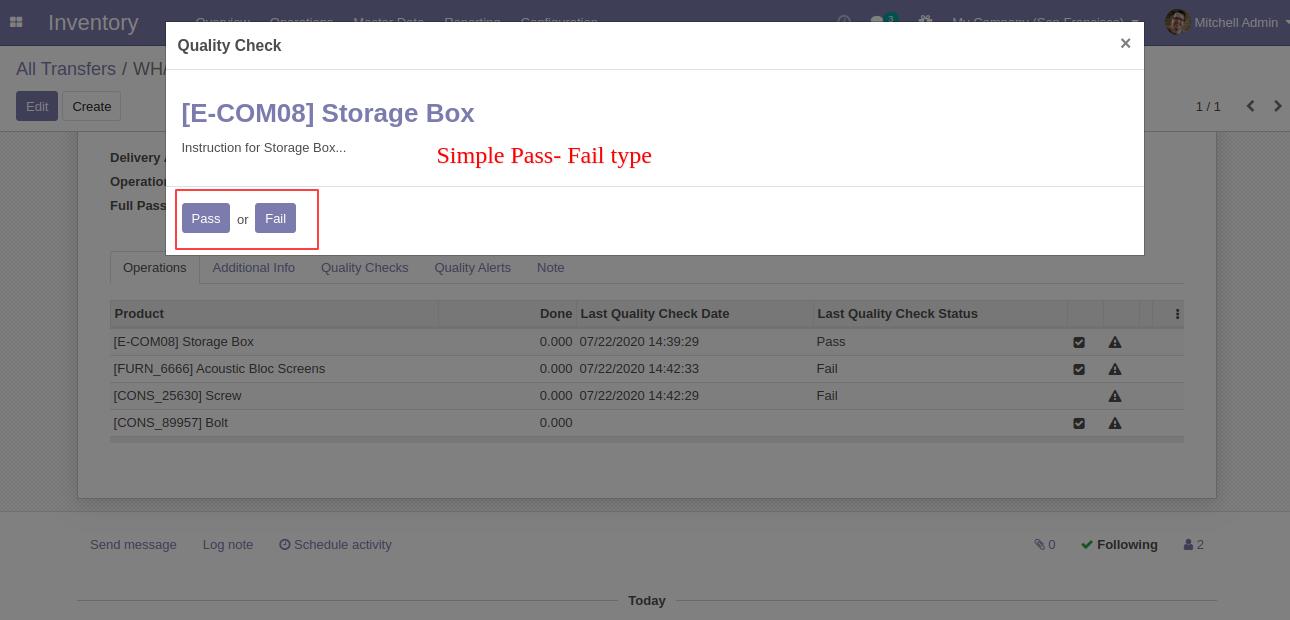
Quality Check Type "Take a Picture", Than responsible person has to add pictures of products.
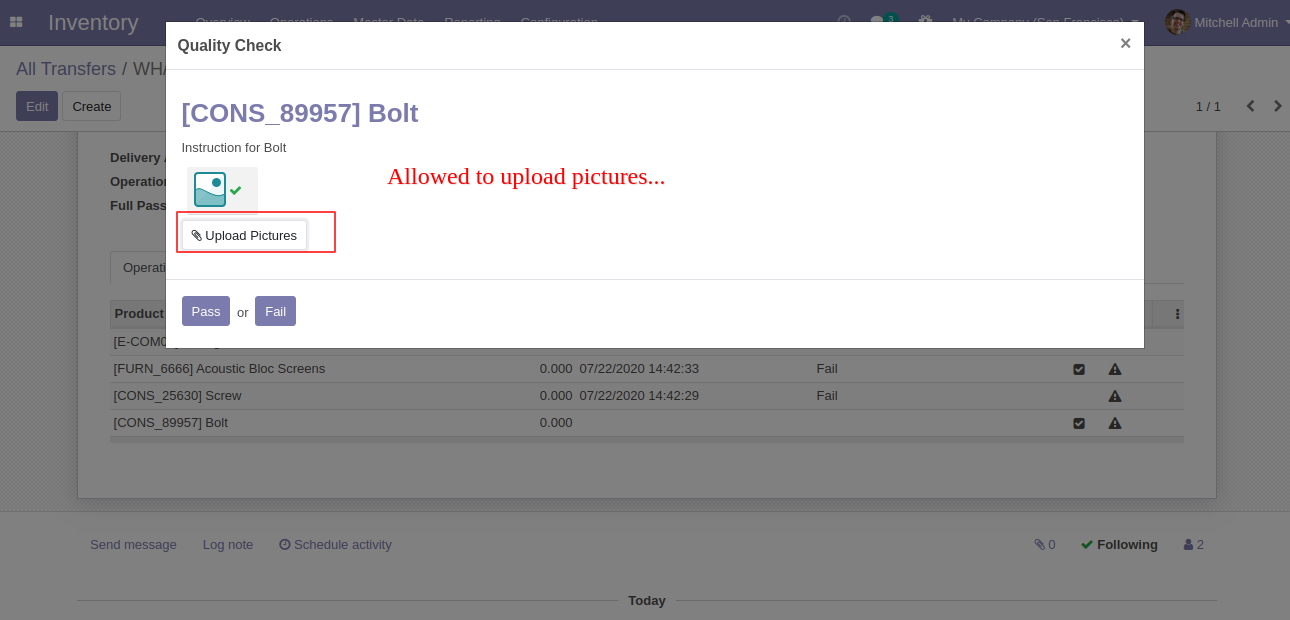
Here users have two buttons for 'Quality Alert' one for global alert and the second for the individual alert.
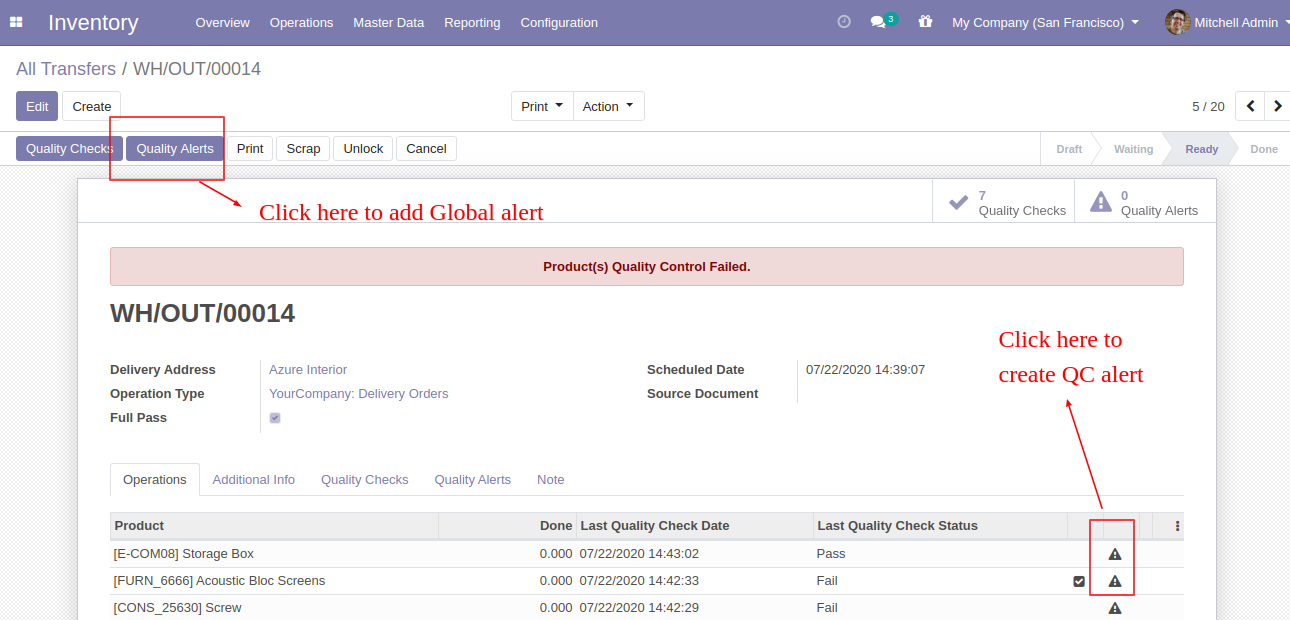
This is global 'Quality Alert' popup. Where you can see a list of all products and names of the responsive team, person, and priority.
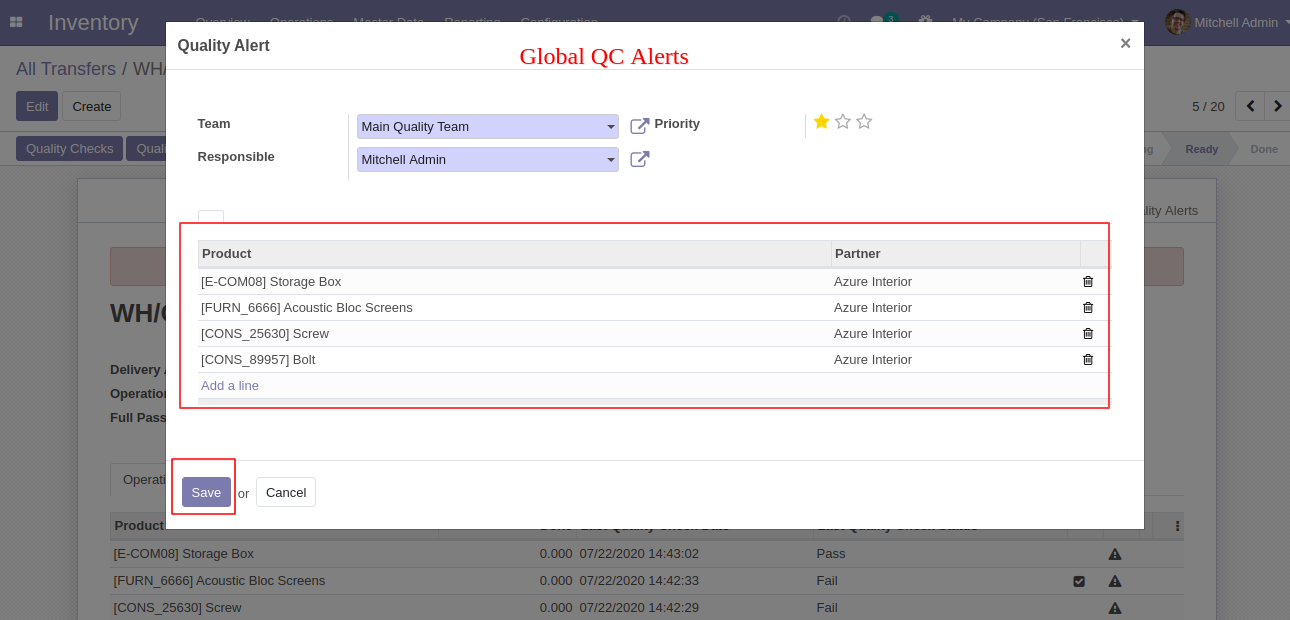
This is global 'Quality Alert' popup. Where you can see a list of all products and names of the responsive team, person, and priority.
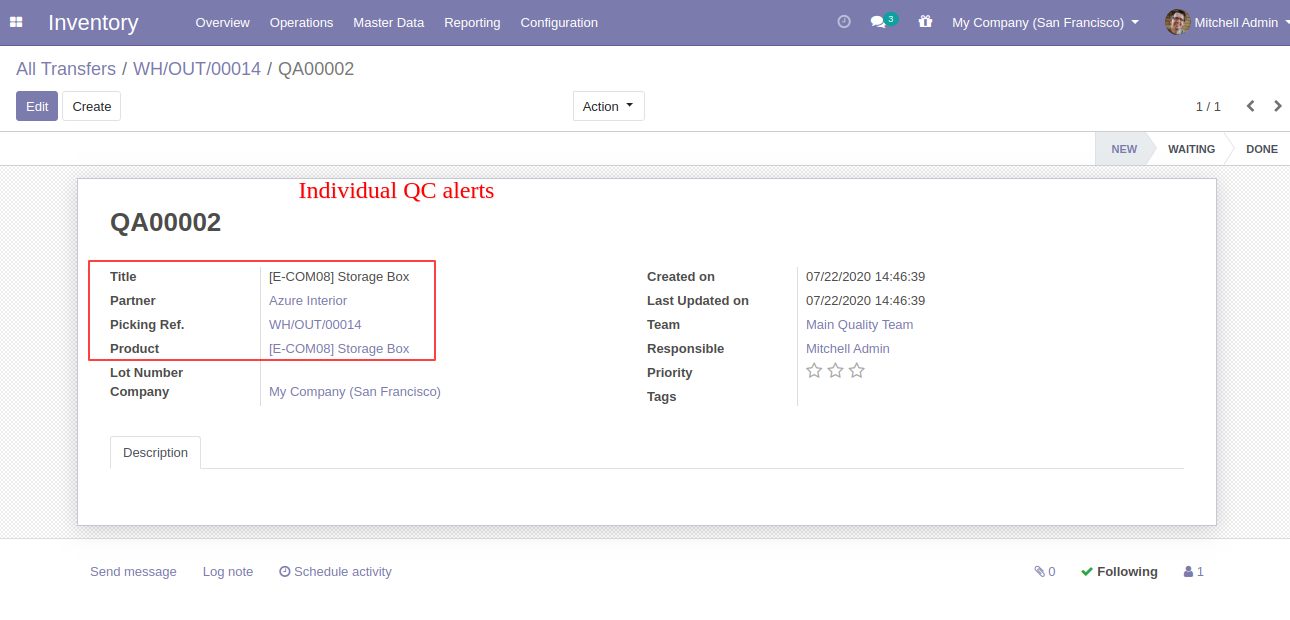
In picking form view there is also a smart button for 'Quality Check' and 'Quality Alert' with the counter.
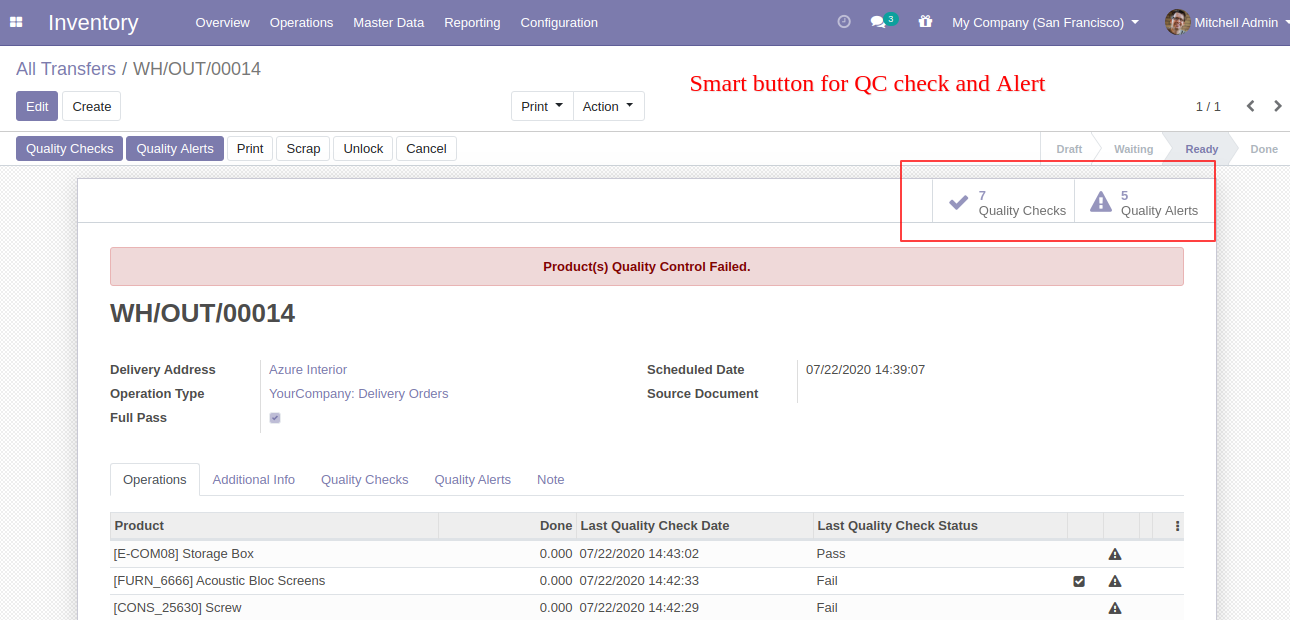
'Pending QC' Menu and Tree View.
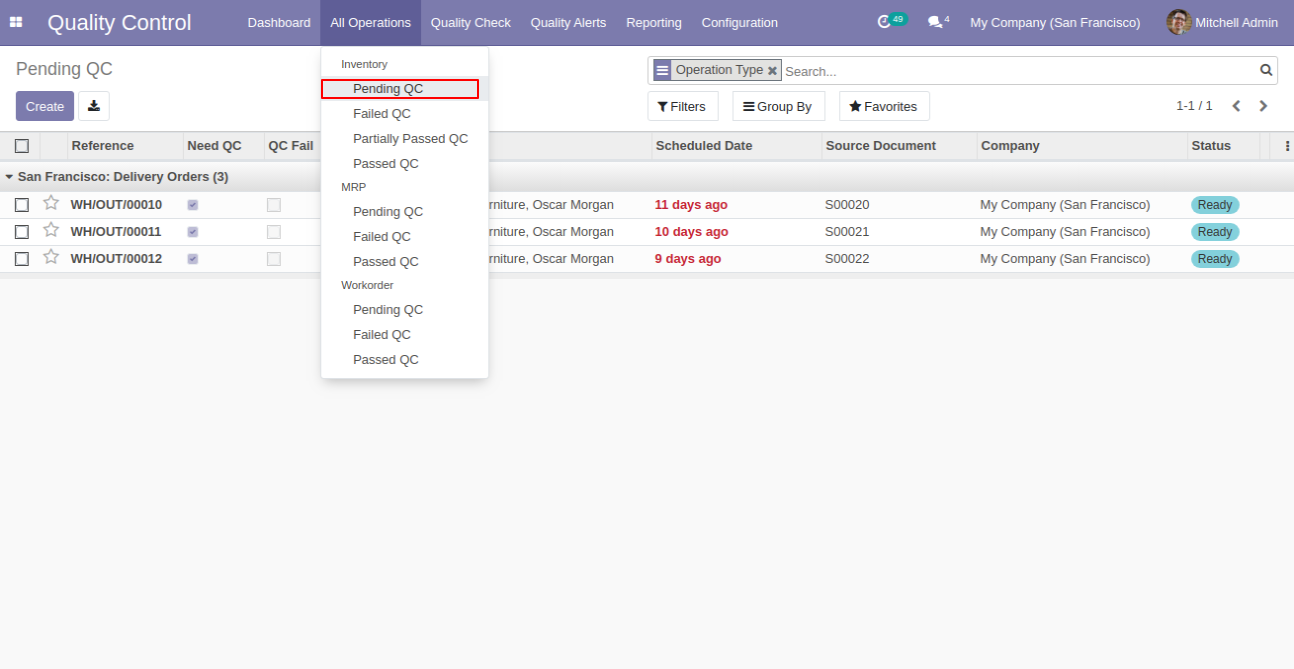
'Failed QC' Menu and Tree View.
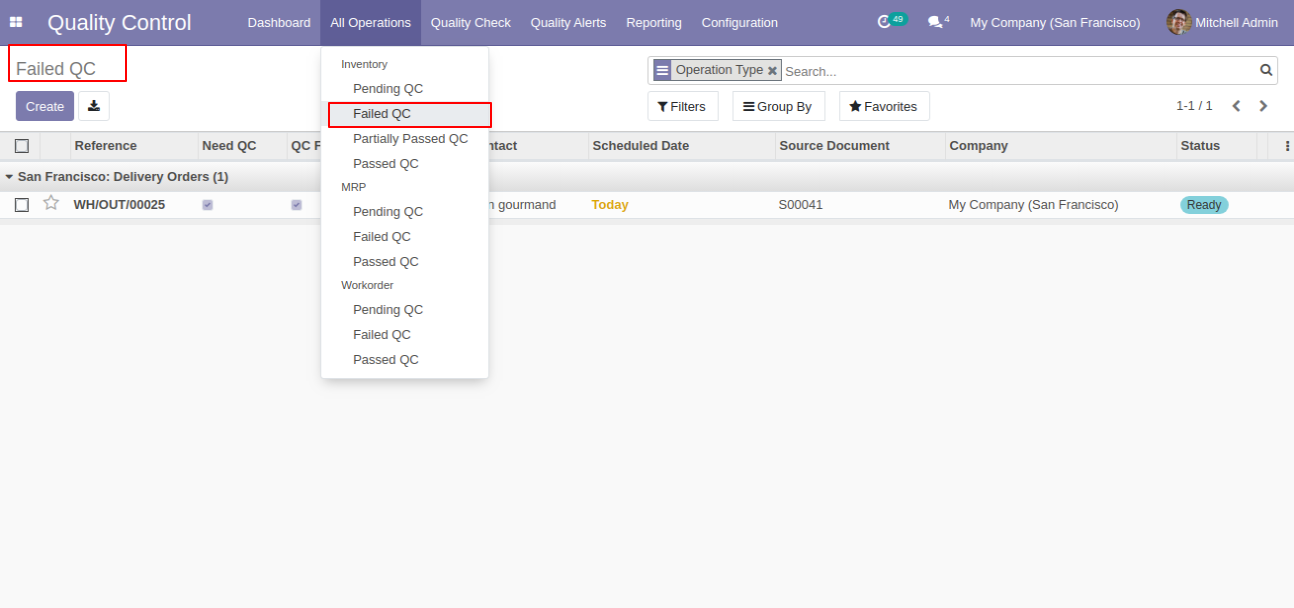
'Partially QC' Menu and Tree View.
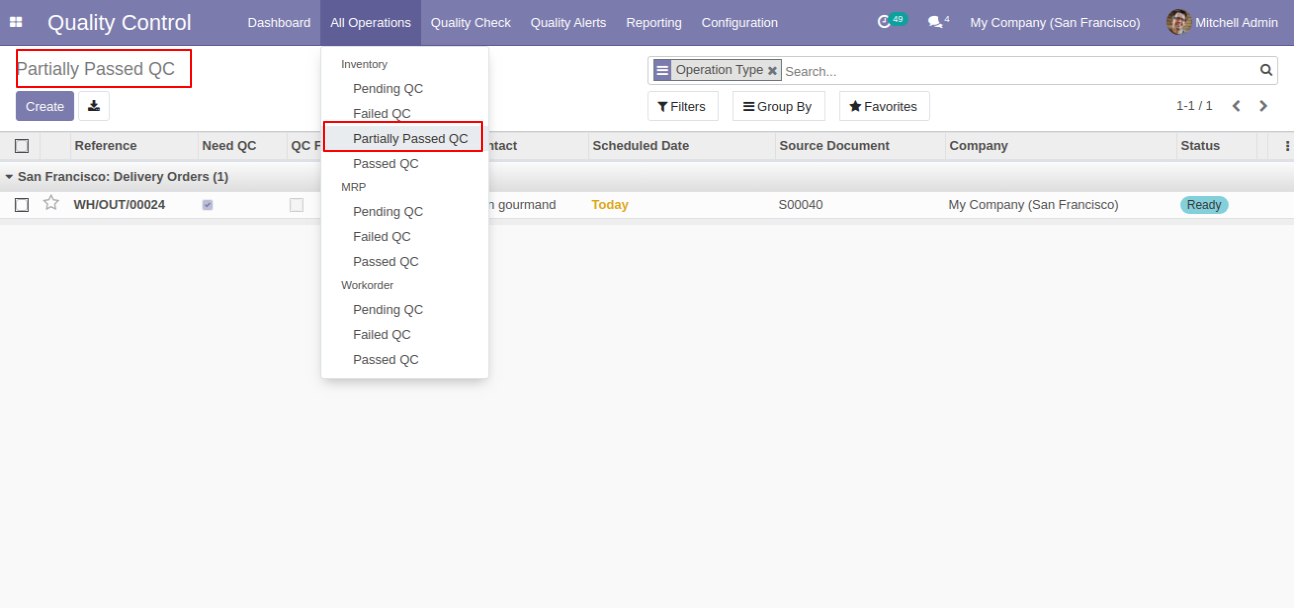
'Passed QC' Menu and Tree View.
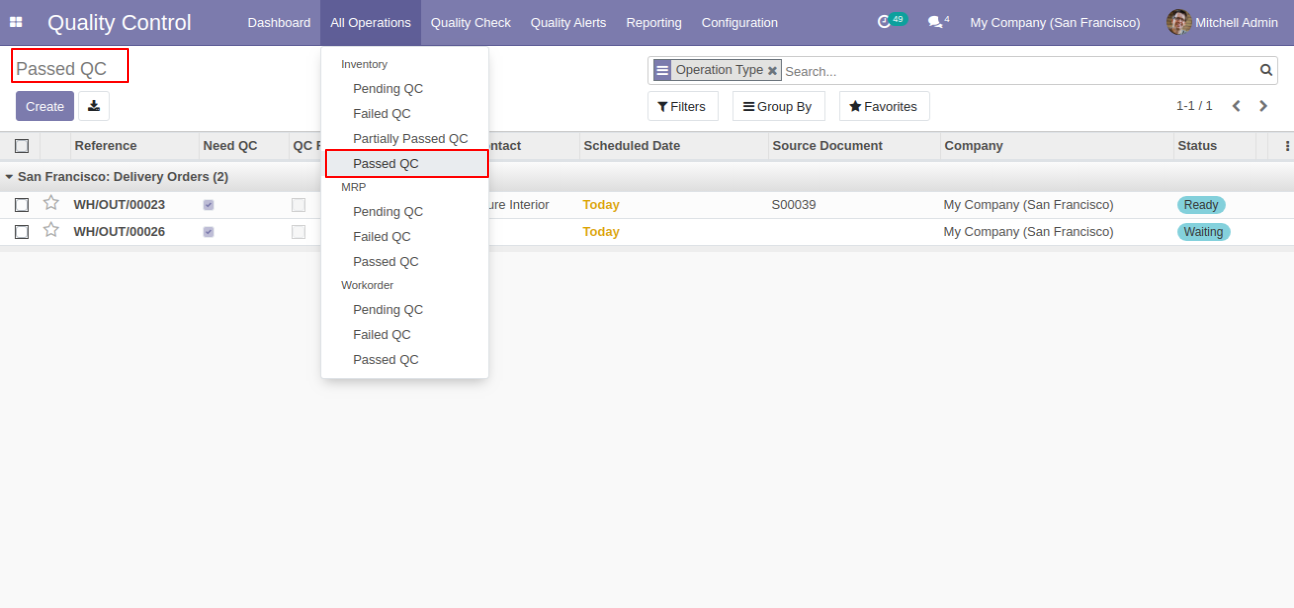
'Quality Check' Menu and Tree View.
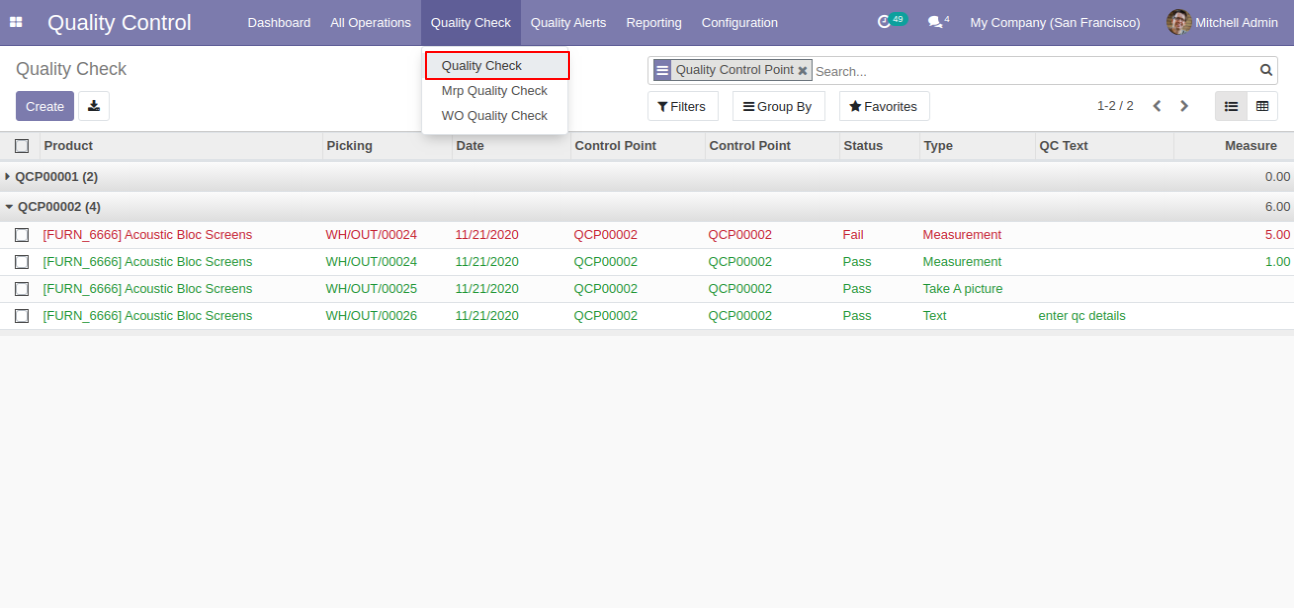
'Quality Check' Form View.
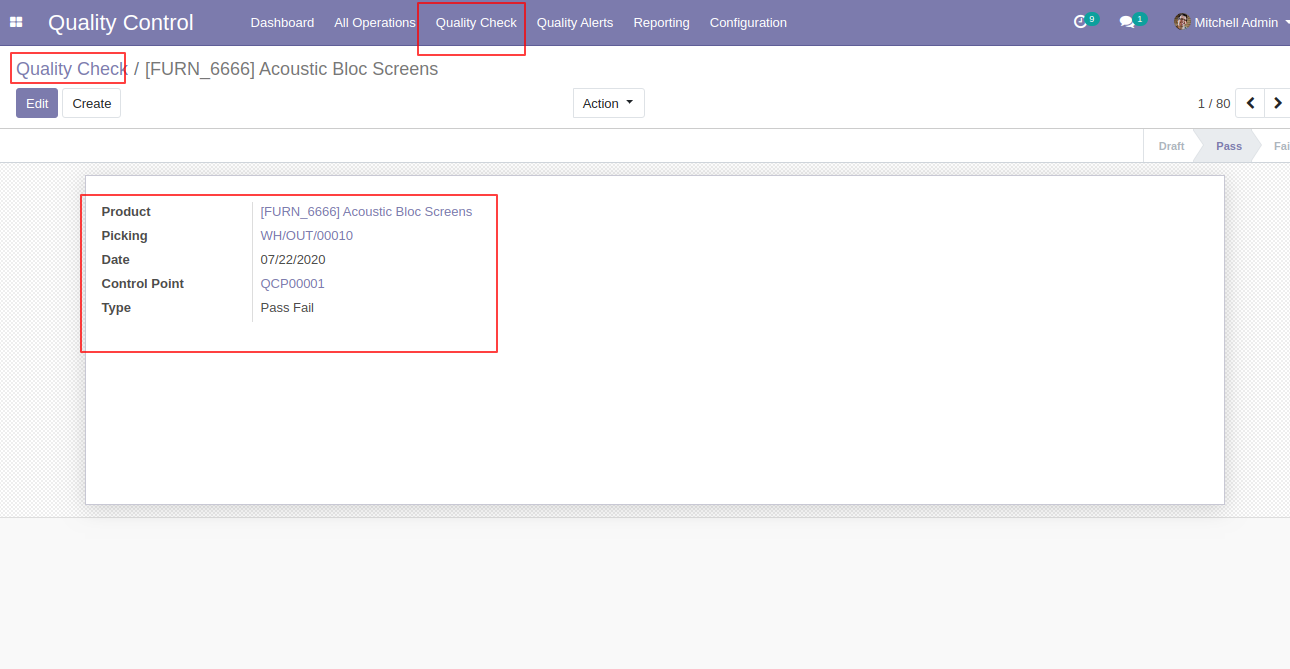
'Quality Alerts' Menu and Tree View.
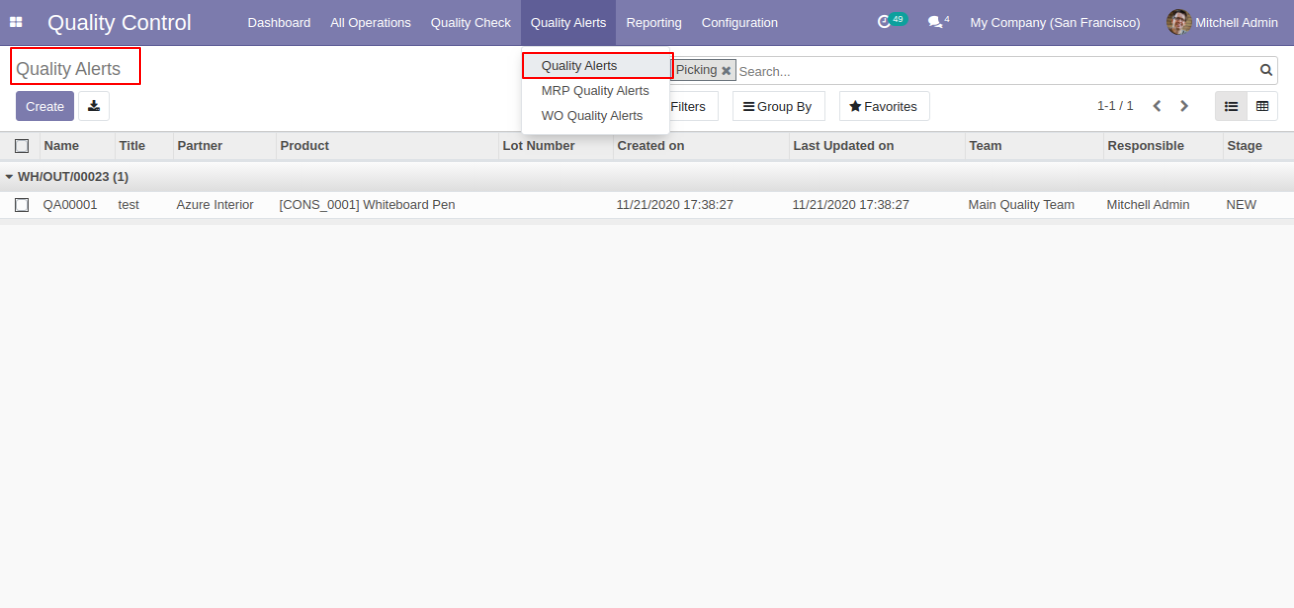
'Quality Alert' Form View
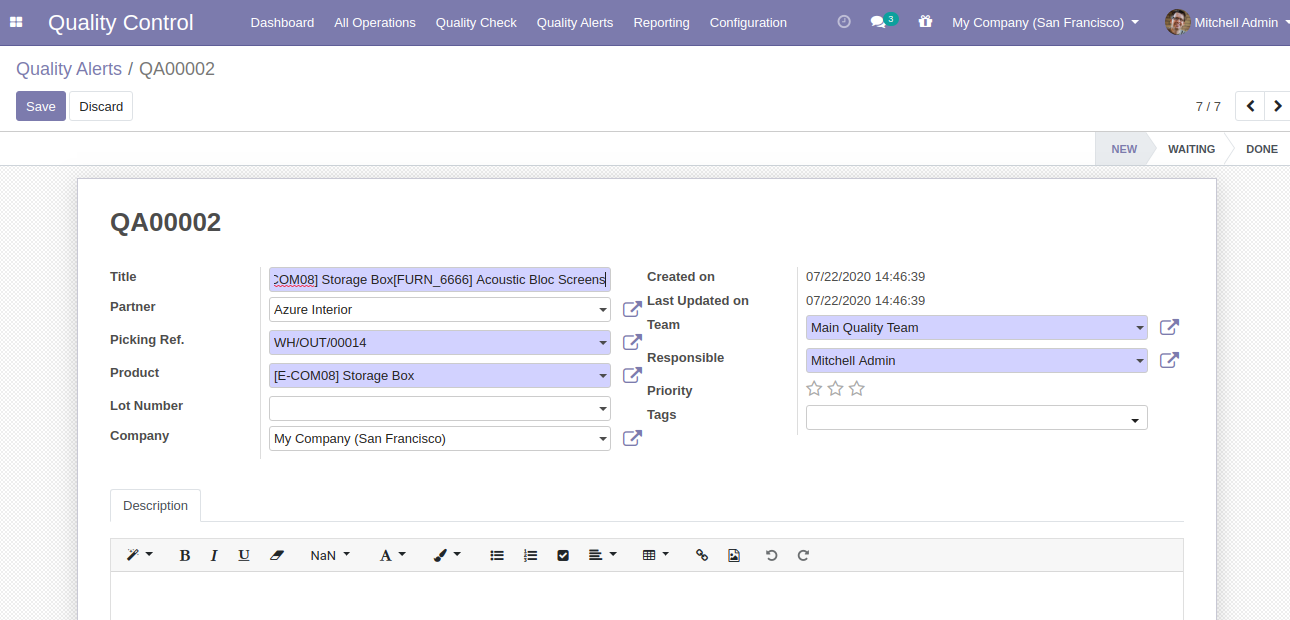
'Quality Check' Analysis Report View.
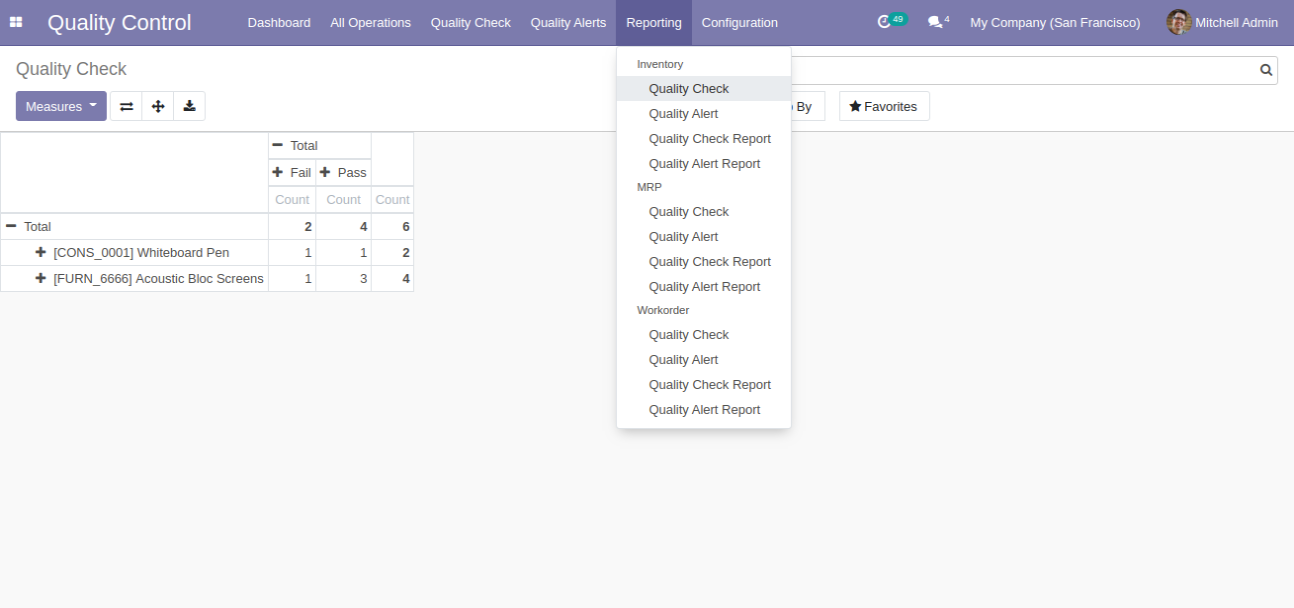
'Quality Alert' Analysis Report View.
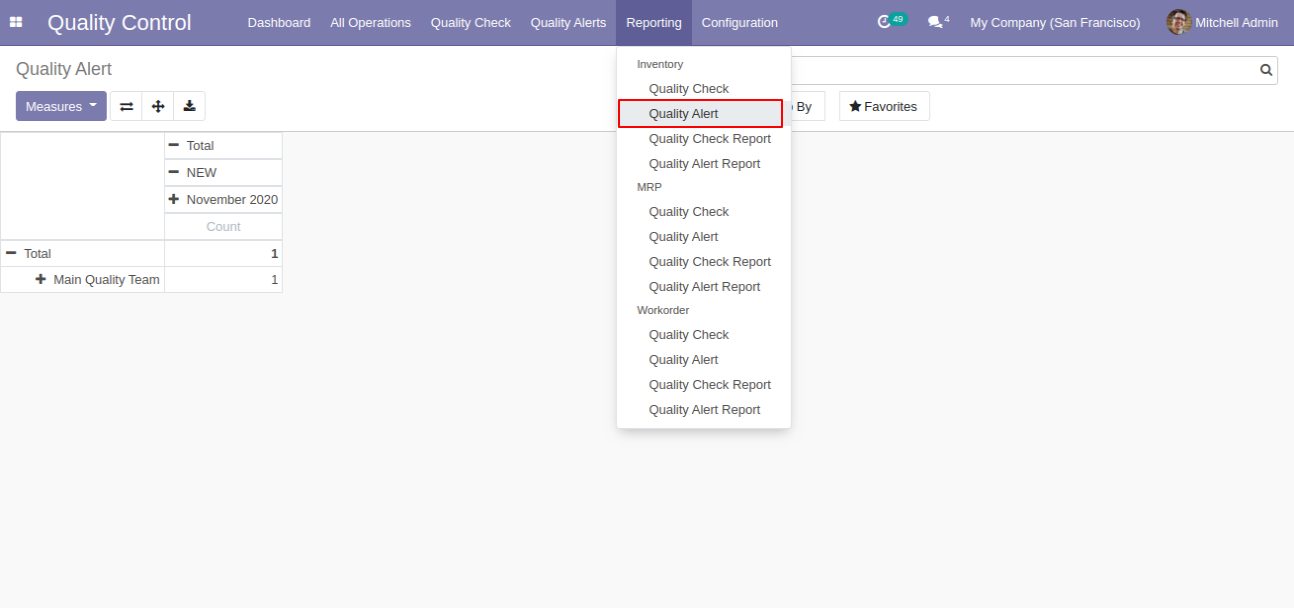
'Quality Check Report' here you can download QC report in pdf.
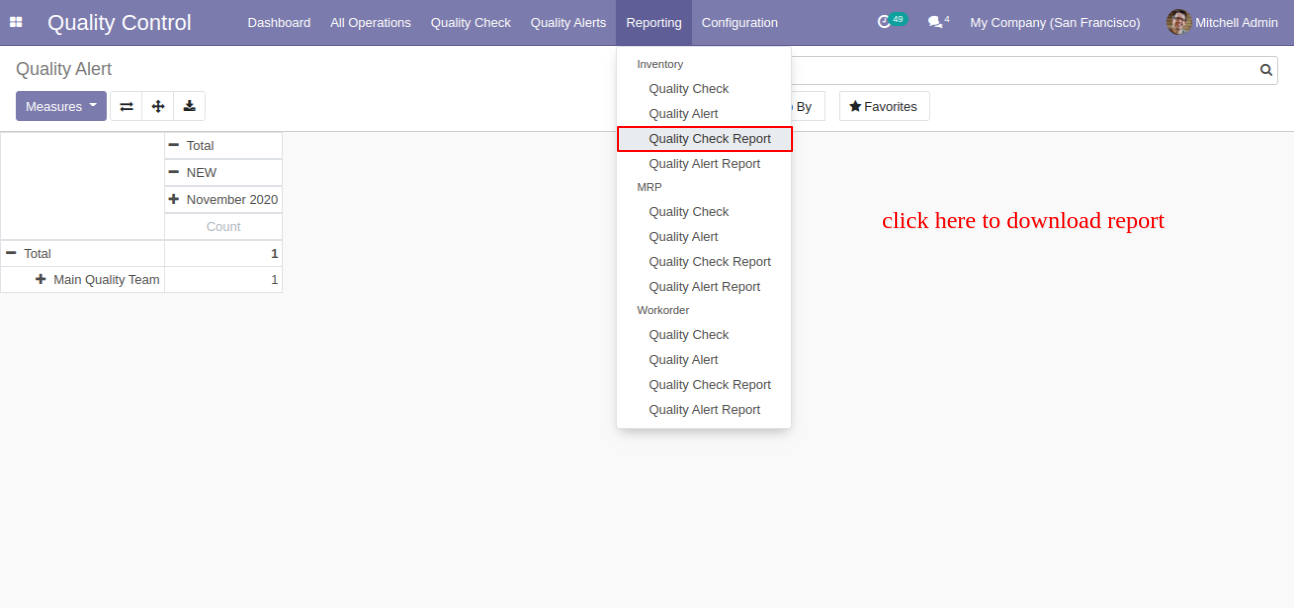
After click on the 'Quality Check Report,' this popup window appears. Where you can customize reports like start and end date, product wise, group by, and status also.
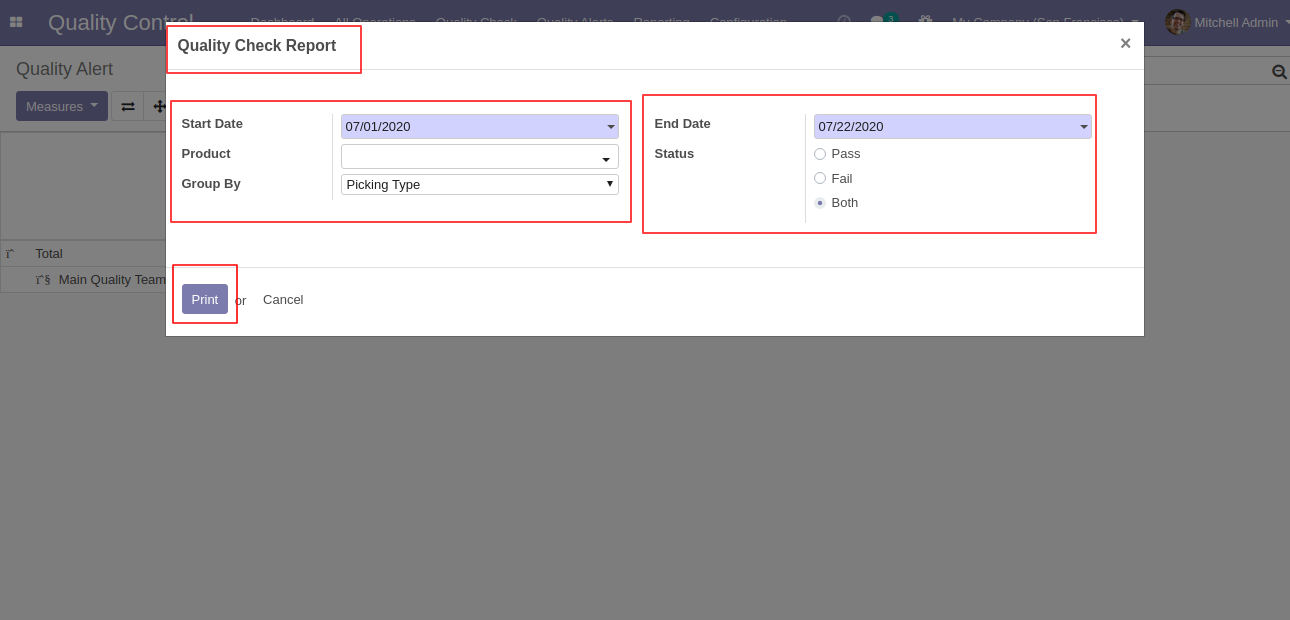
'Quality Check Report' group by 'Picking Type'.
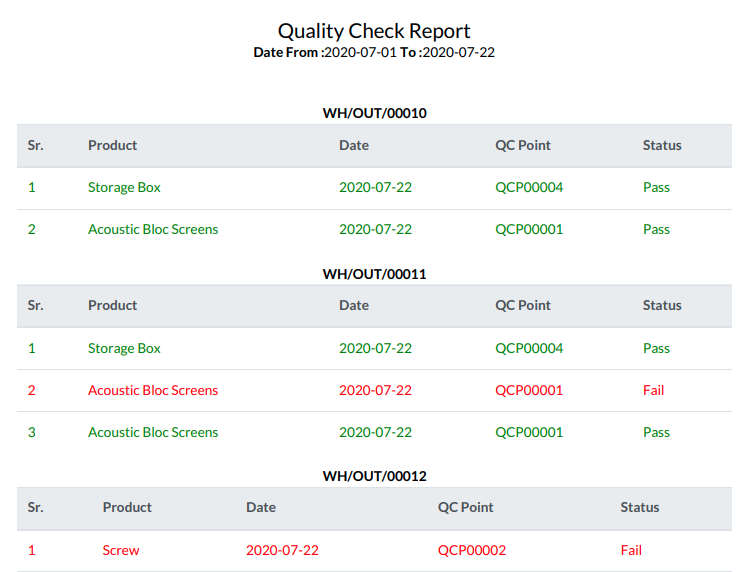
Select 'Product' in the group by.
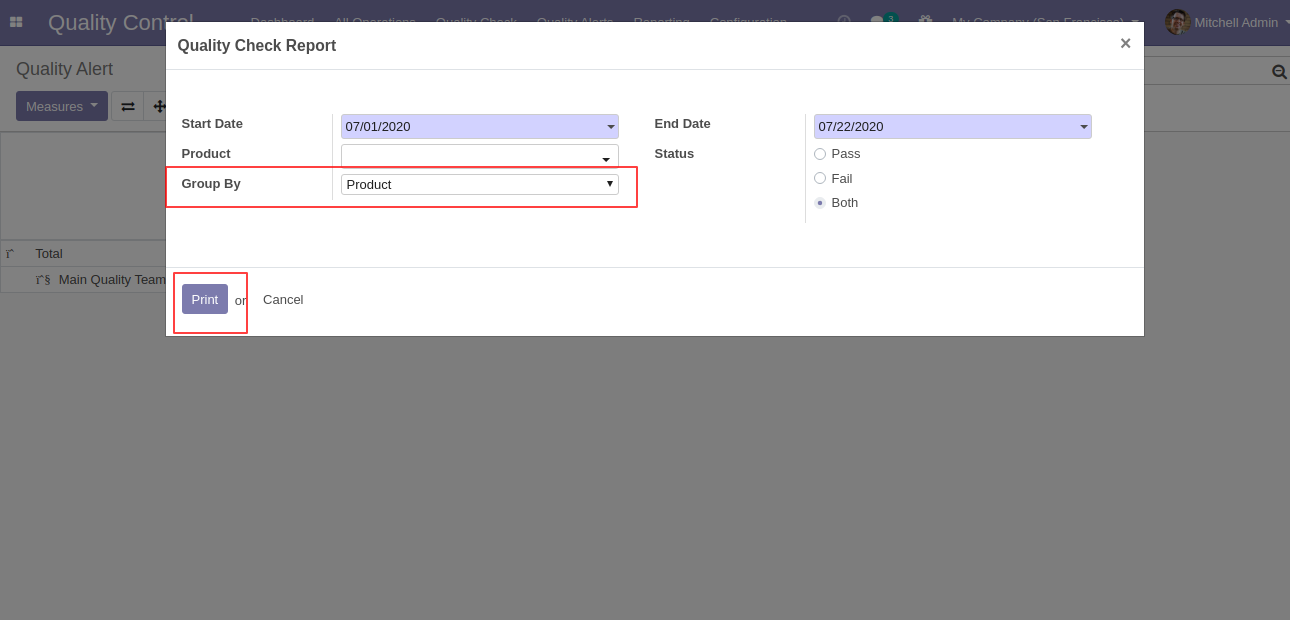
'Quality Check Report' group by 'Product'.
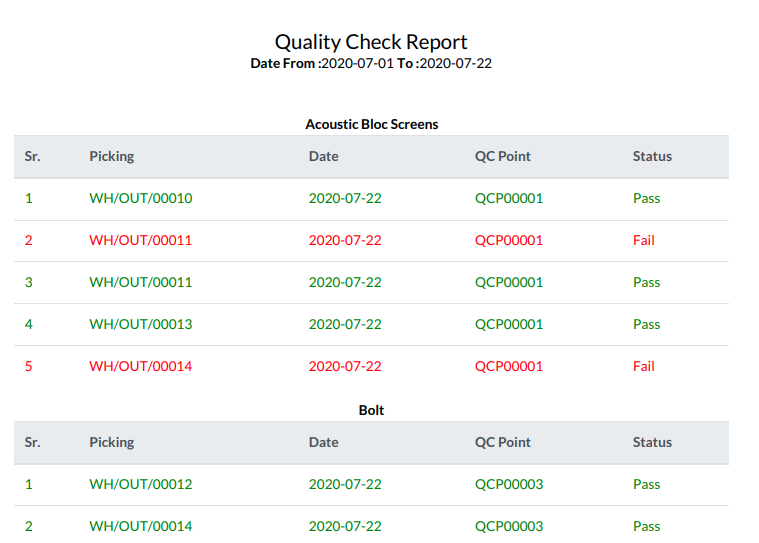
In wizard only select status 'Both'.
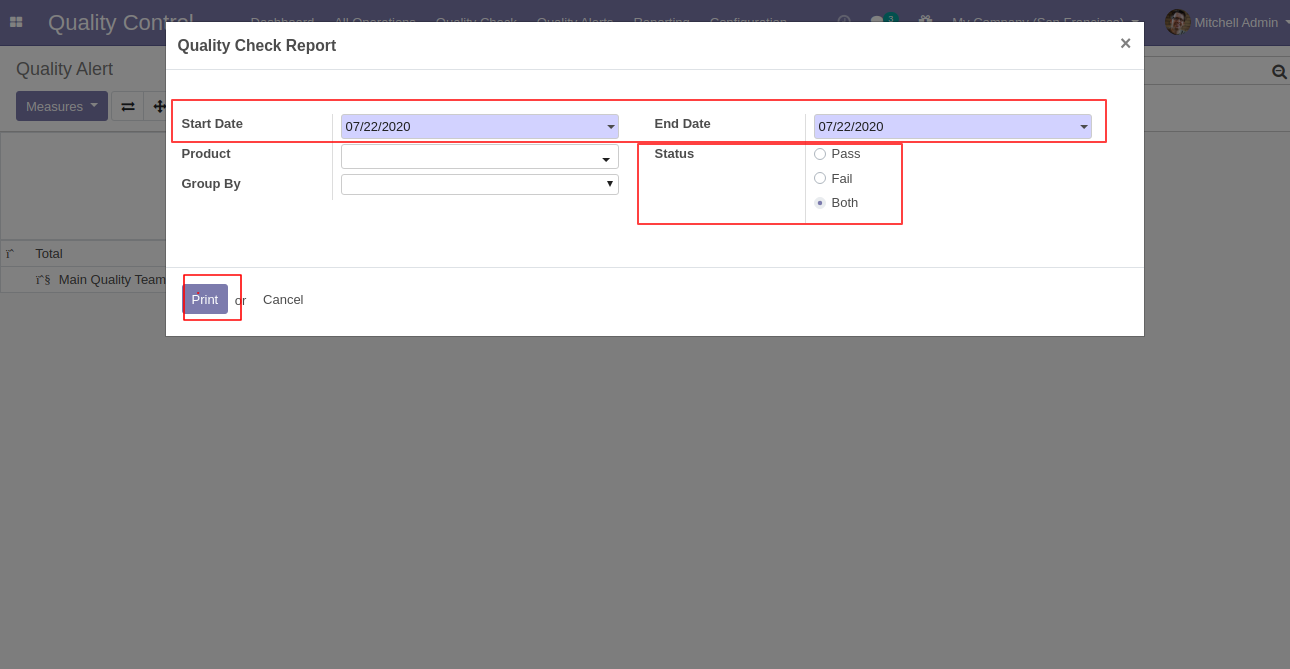
'Quality Check Report' for all products with both status.
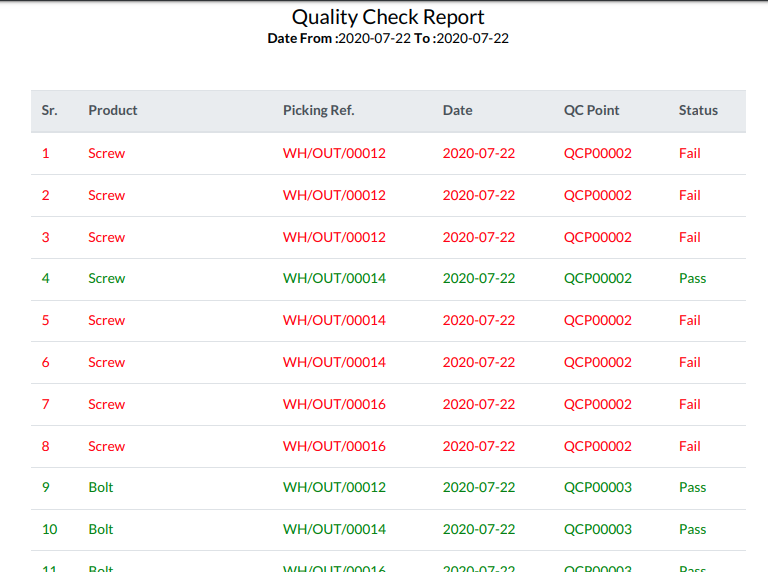
'Quality Alert Report' by-product and responsible person with the stage.
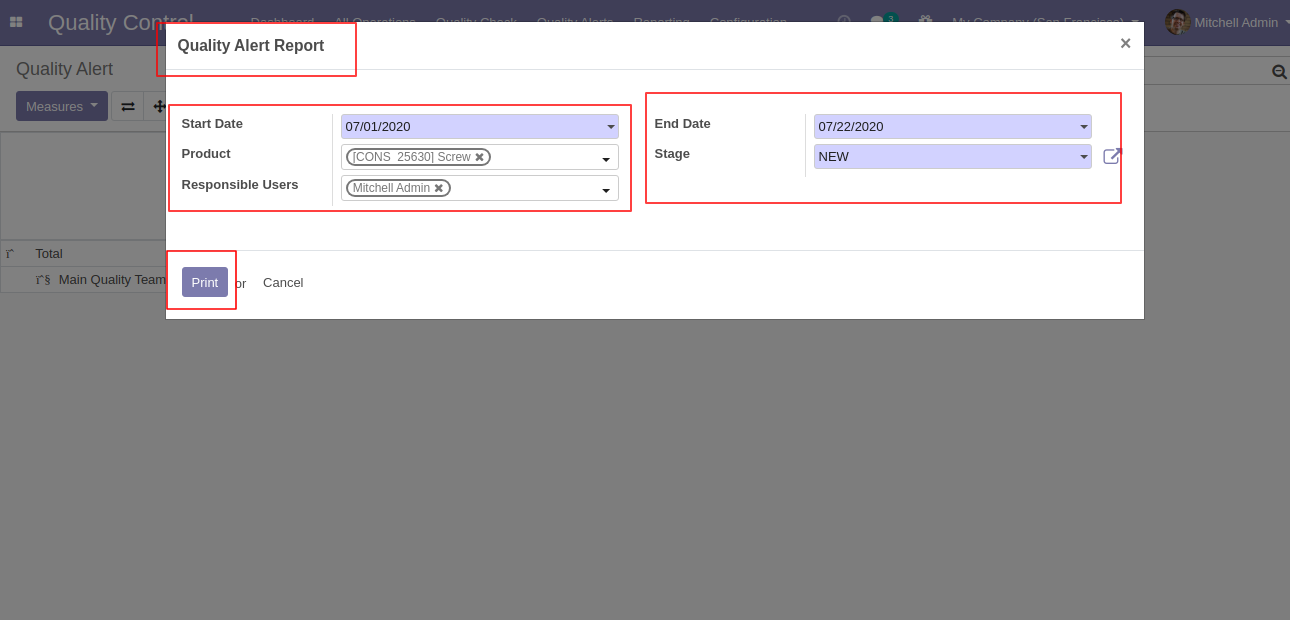
'Quality Alert Report' PDF report looks like below.
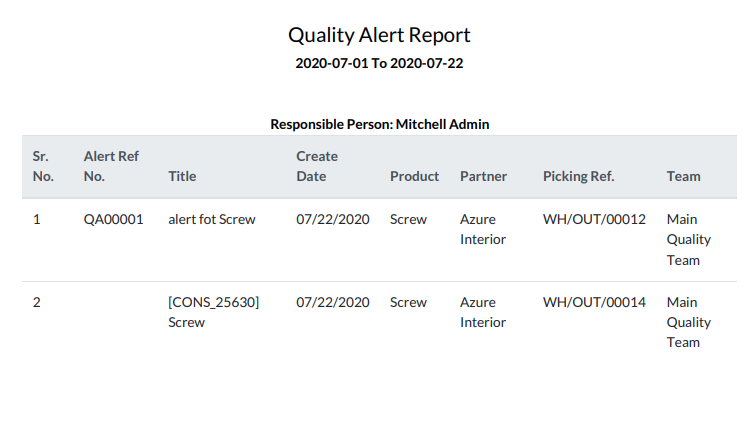
'Quality Point' form view. Here you can create quality point for multiple products and multiple operations. Just select more then one products and operatios as well.
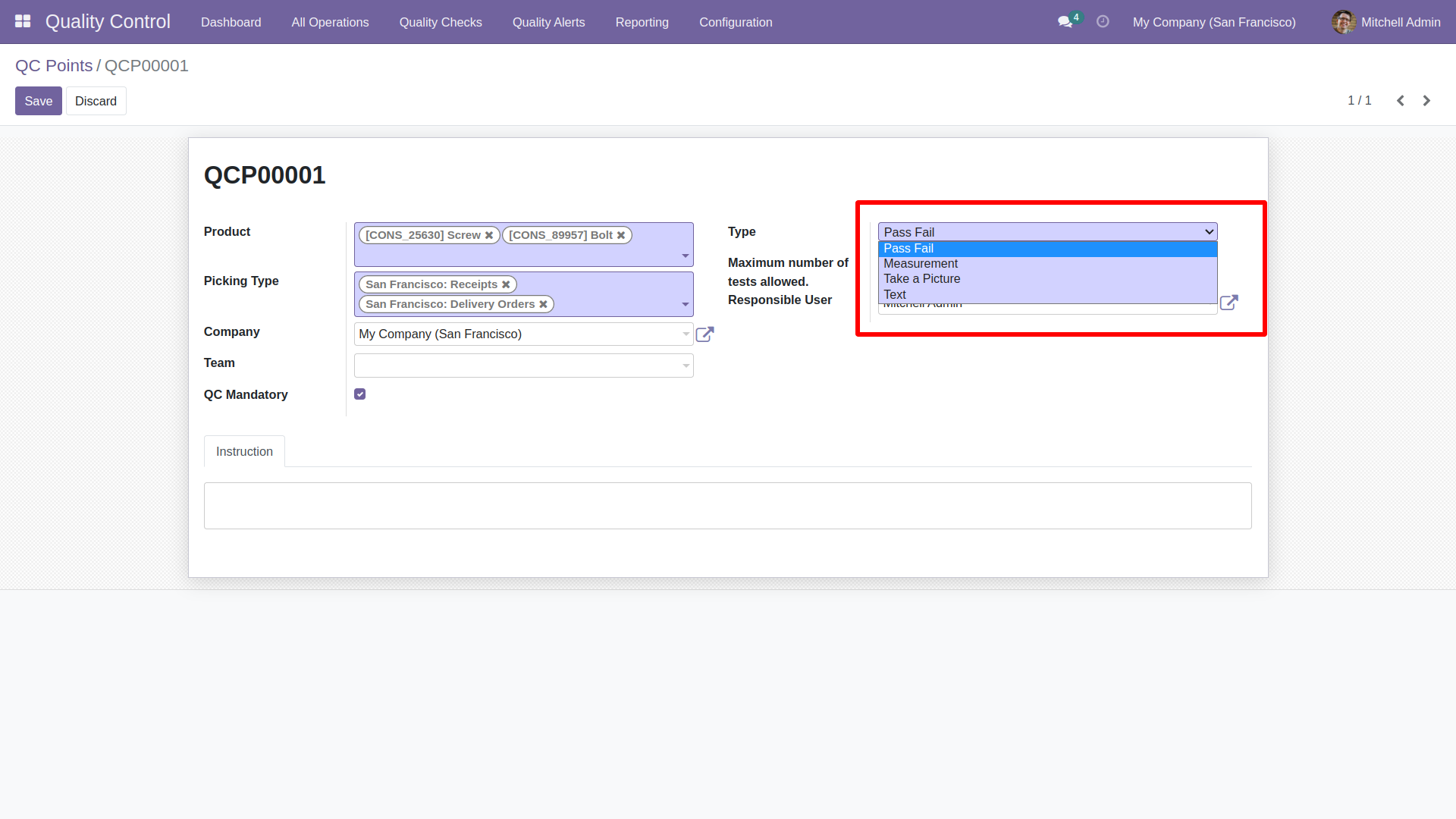
Now make delivery orders and click on 'Right Icon' in delivery move line and this window will popup out. Here you can see "1/2" that means here you have two attempt for test this products.
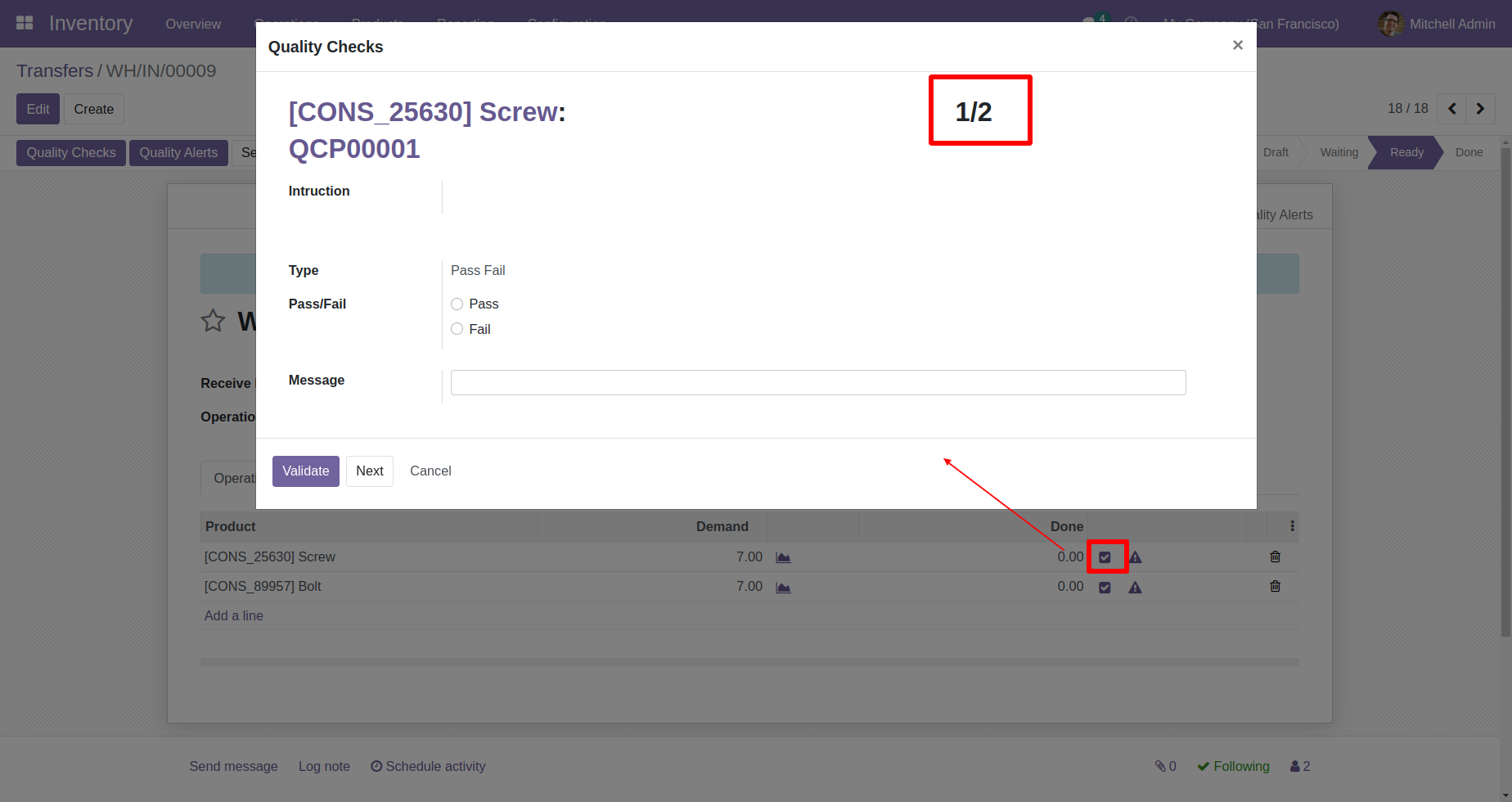
Same for another producs in delivery move line.
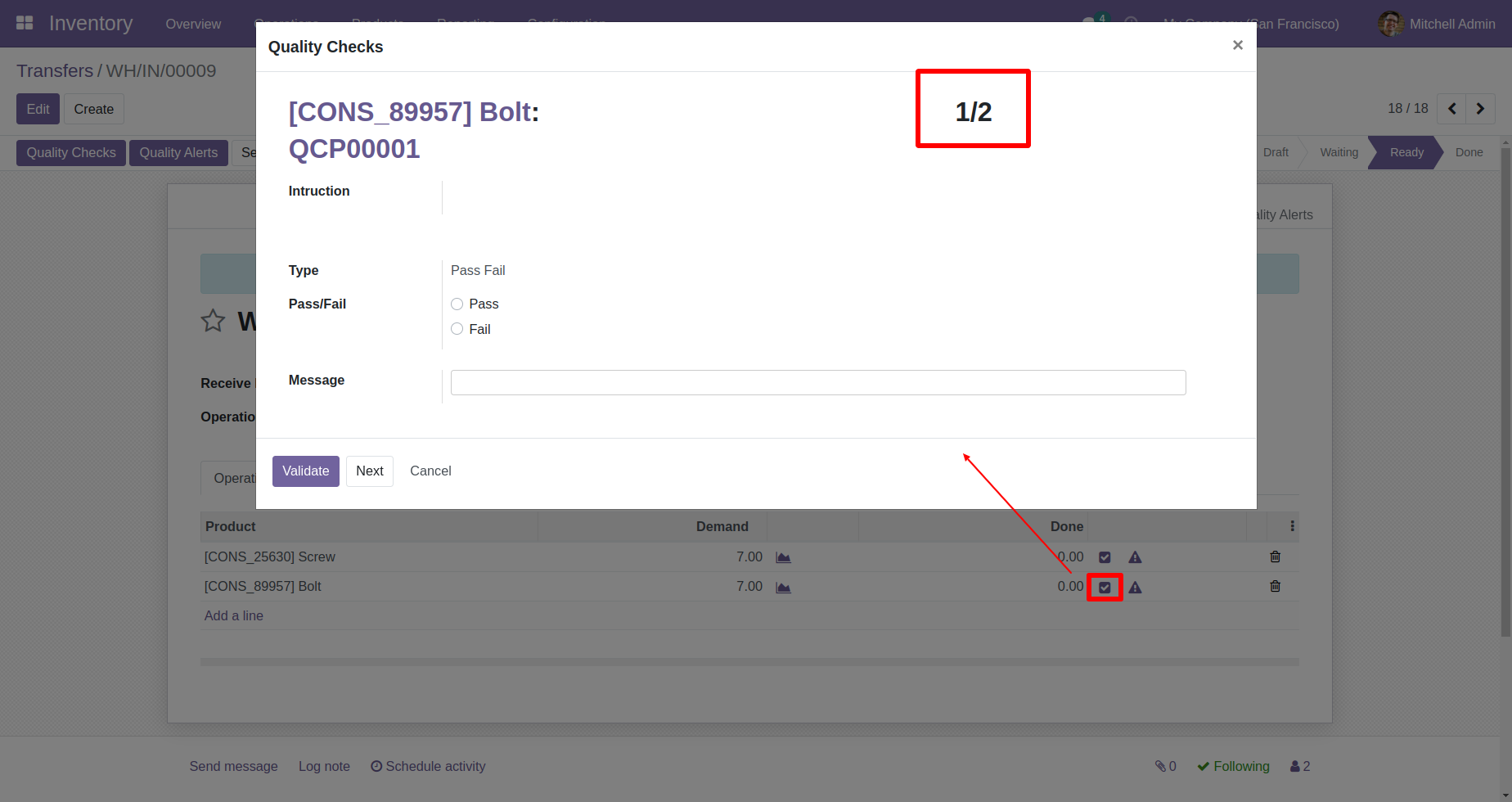
Now, If you click 'Quality Check' from the header. so you have to perform total 4 time quality check. 2 - 2 quality check of each products (as we set in quality points).
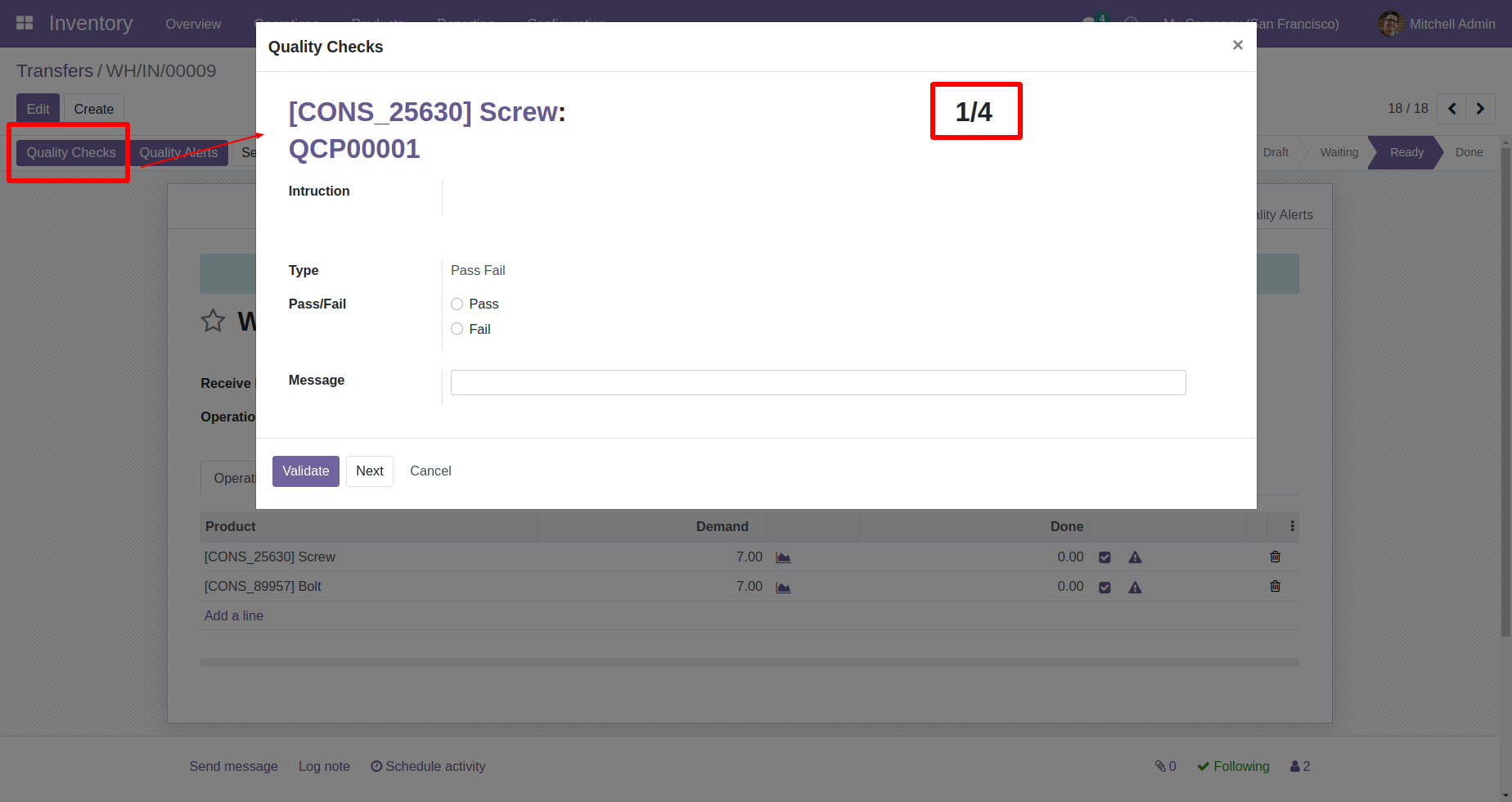
If QC is still pending then it will display this warningn message.
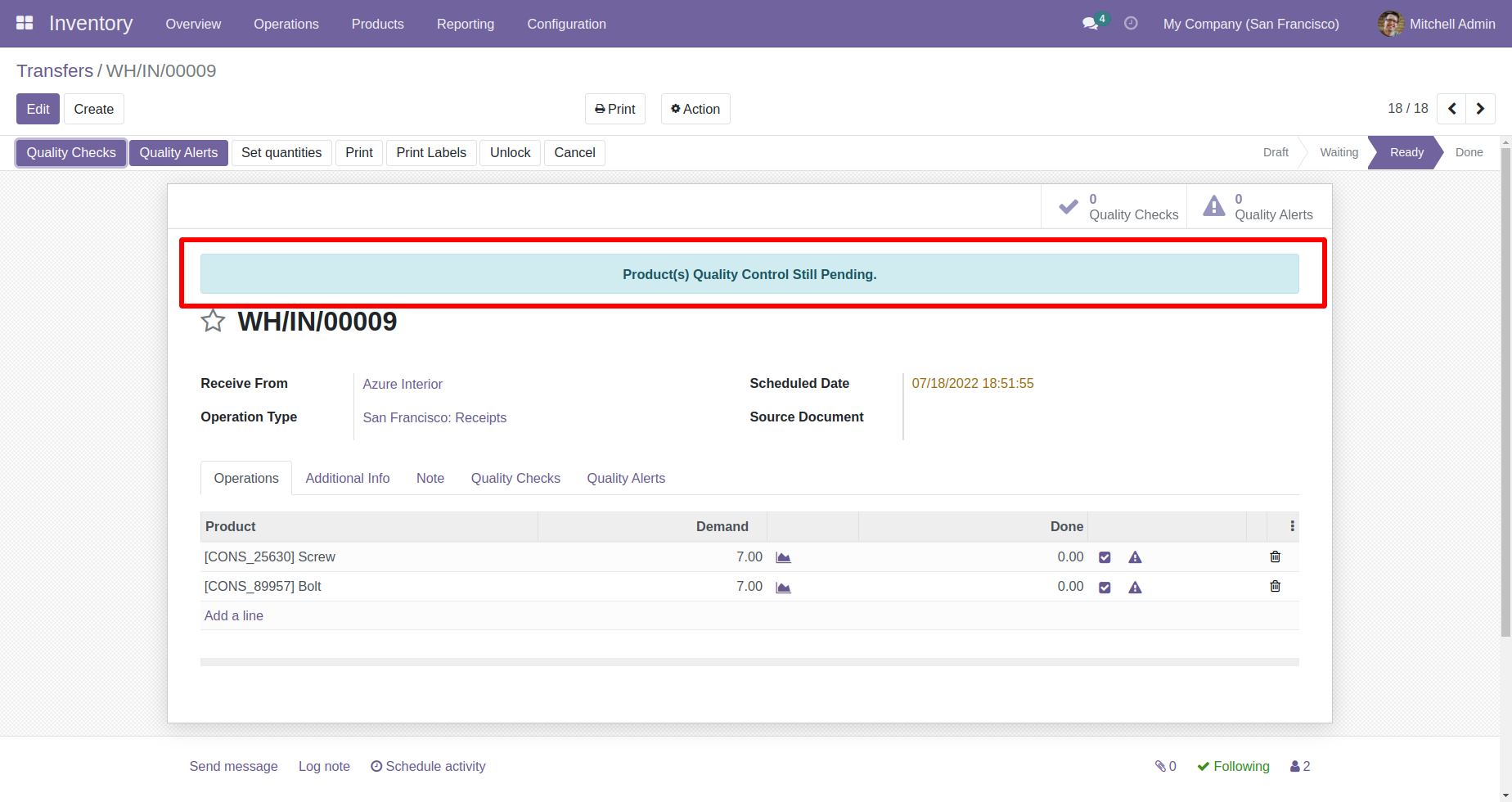
If Quality Check is partially done, then it will display this warnign message.
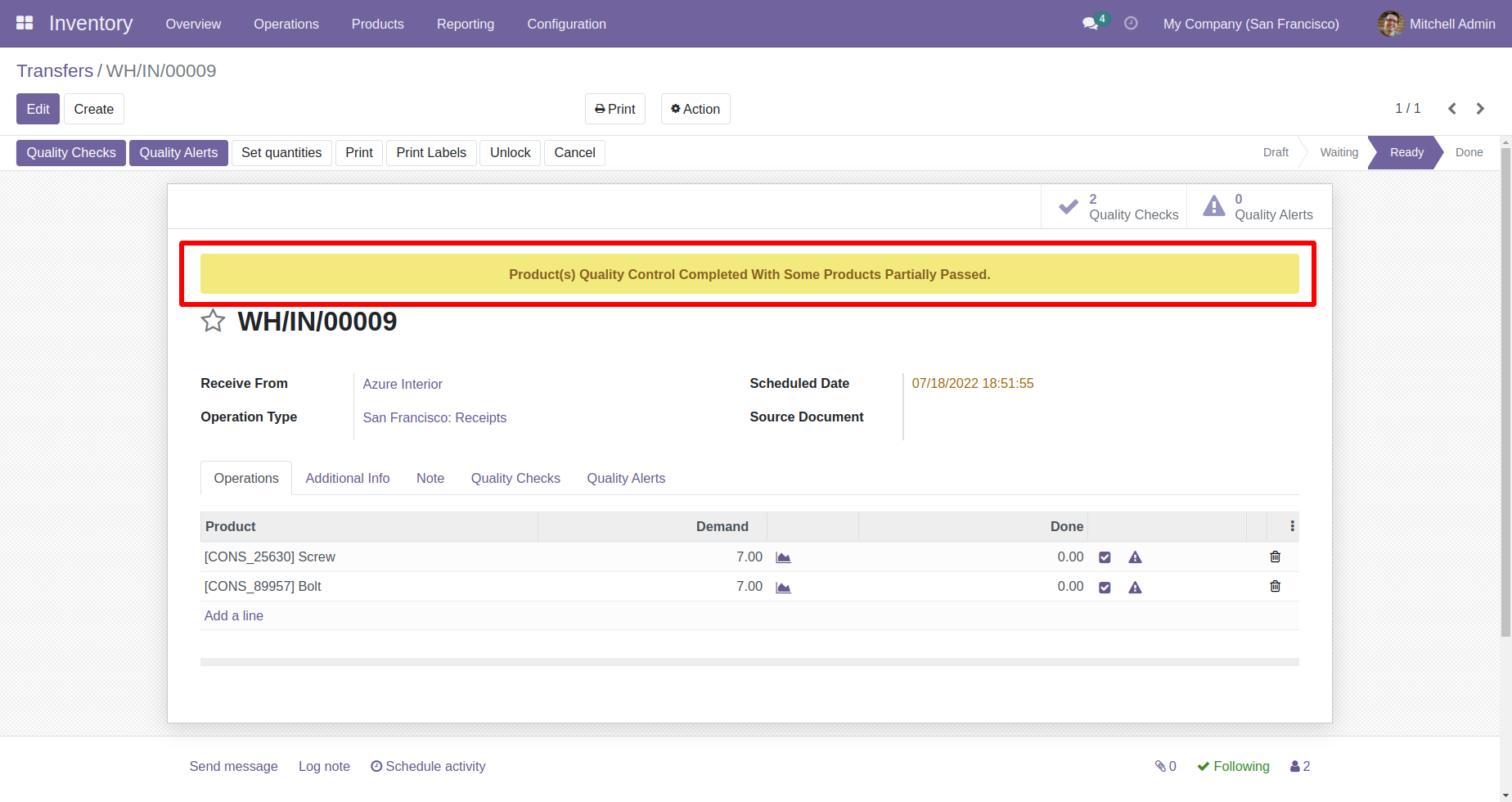
If you done all quality check done success fully then it will display this warning message and you can see the QC in tab 'Quality Check'
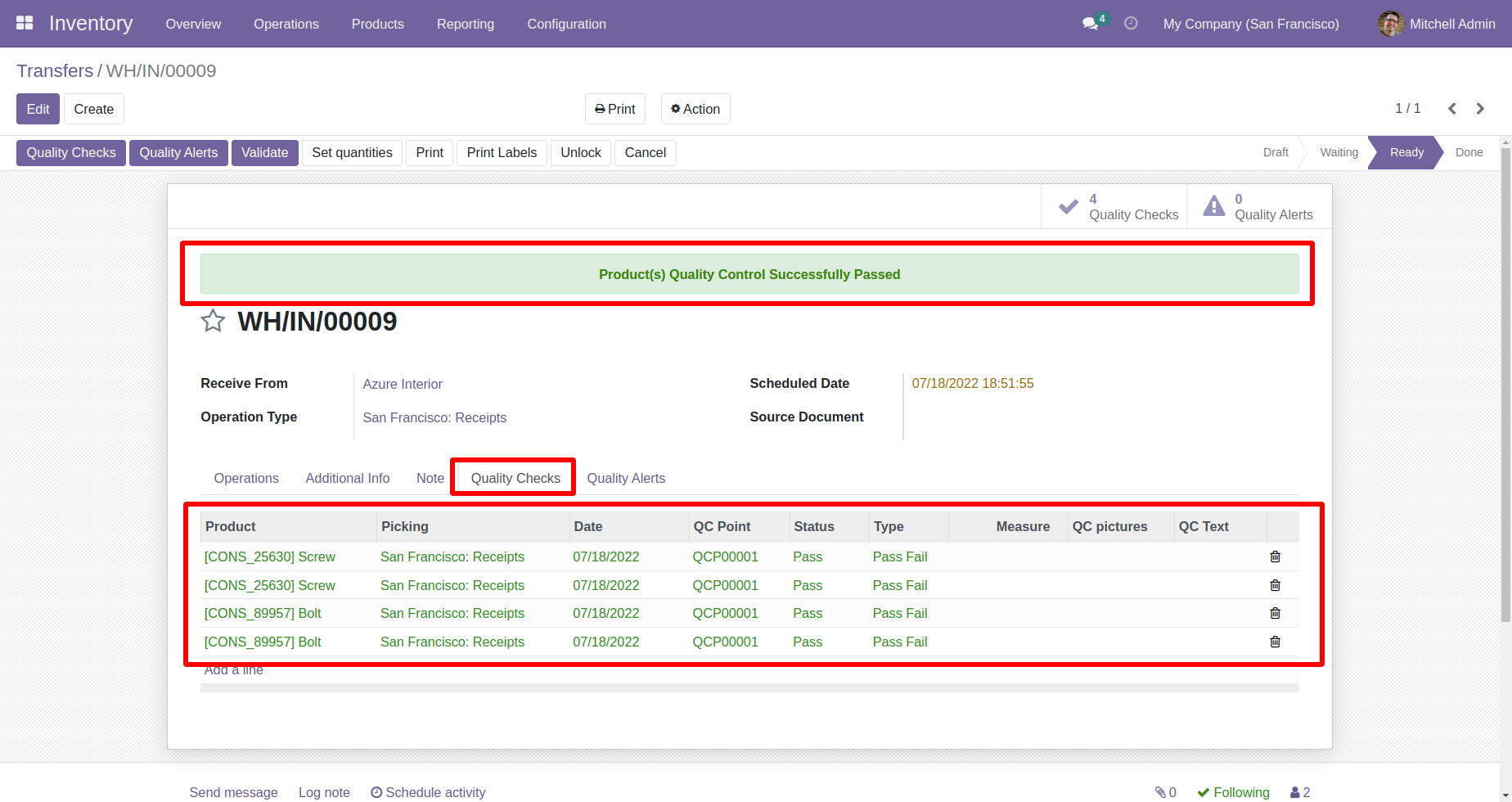
In Quality Point you have to set product and piking type manufacturing.
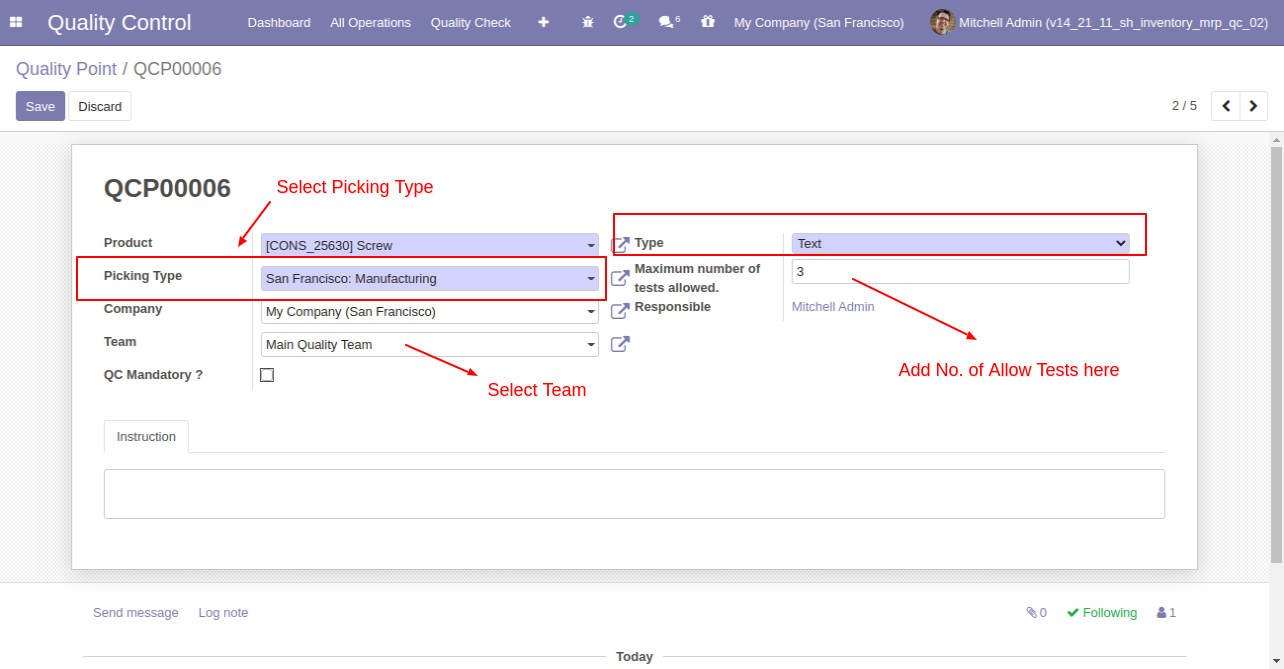
In manufacturing order form view, there are two buttons "Quality Alerts" and "Quality Check", there are two smart buttons as you can see the quality alert and quality check, also see global alert warning label on form top.
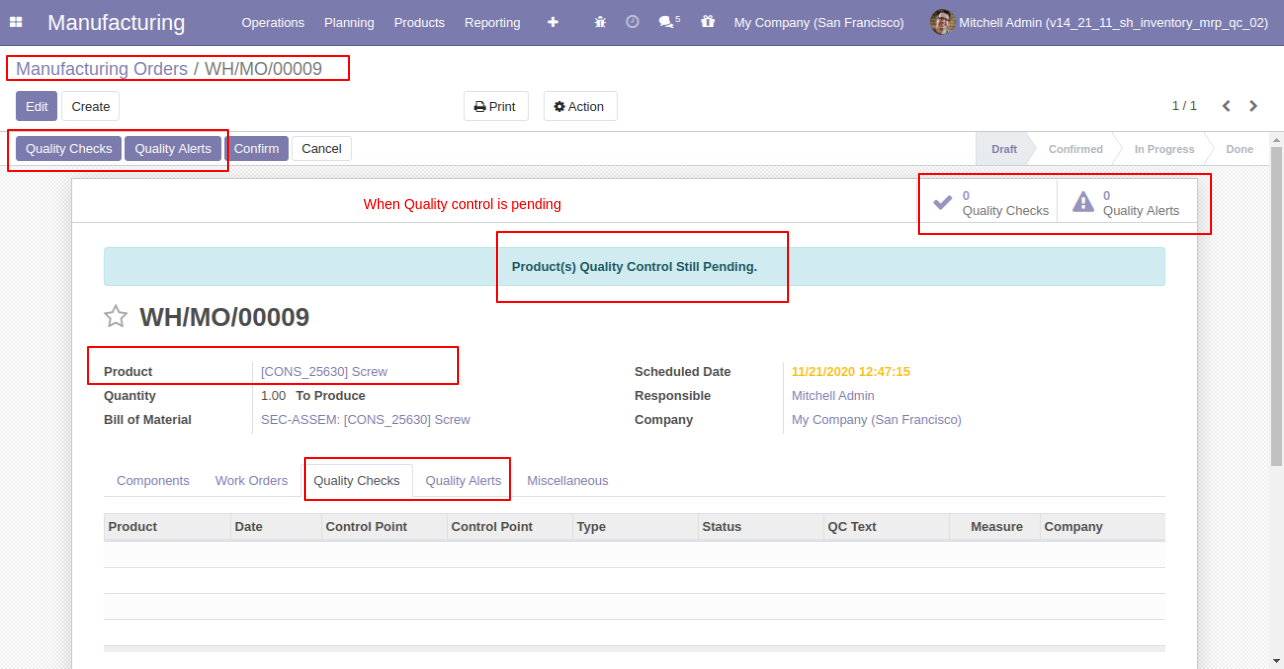
While clicking on "Quality Check" and check type "Text Only", In the wizard you have to add text and click Pass or Fail.
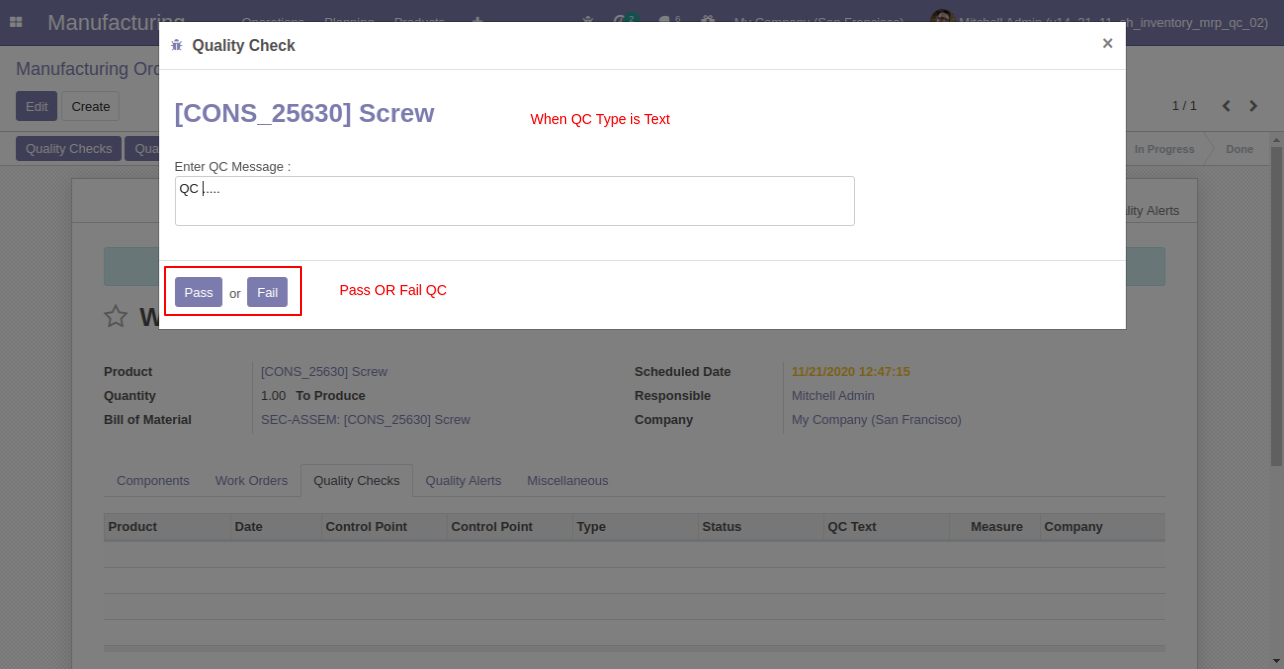
"Quality Points" Form View. Where you can define the quality points of each product with severals points.
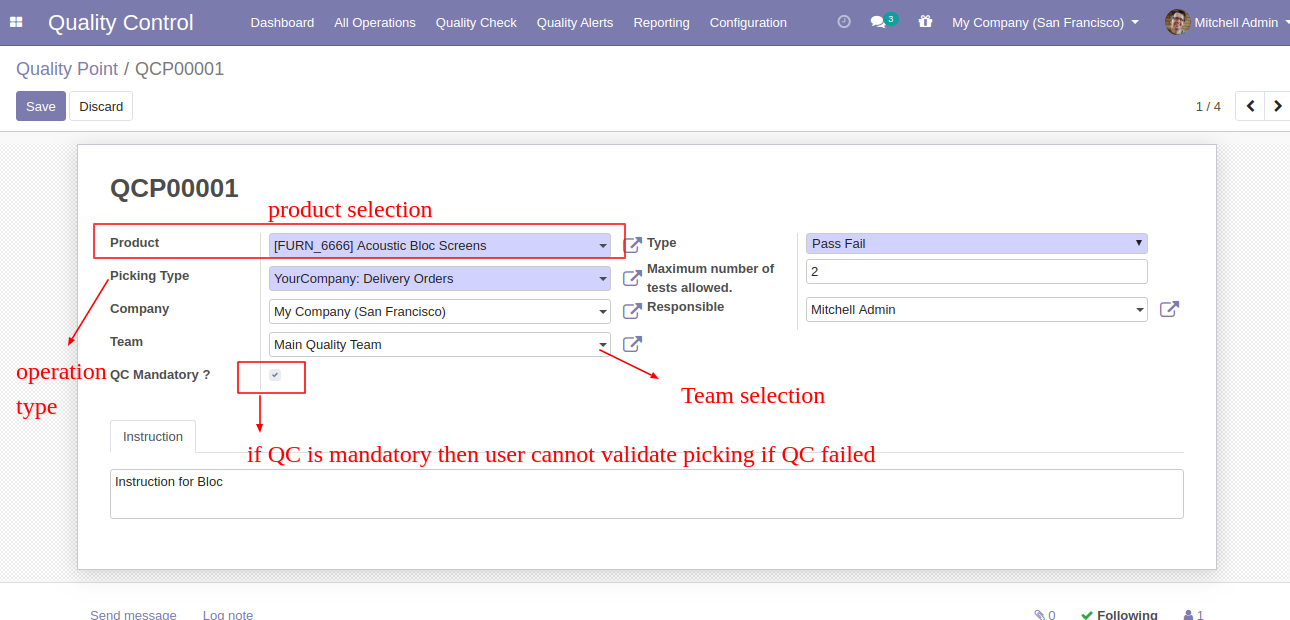
If Pass, Then that line will glow green and status is a pass.
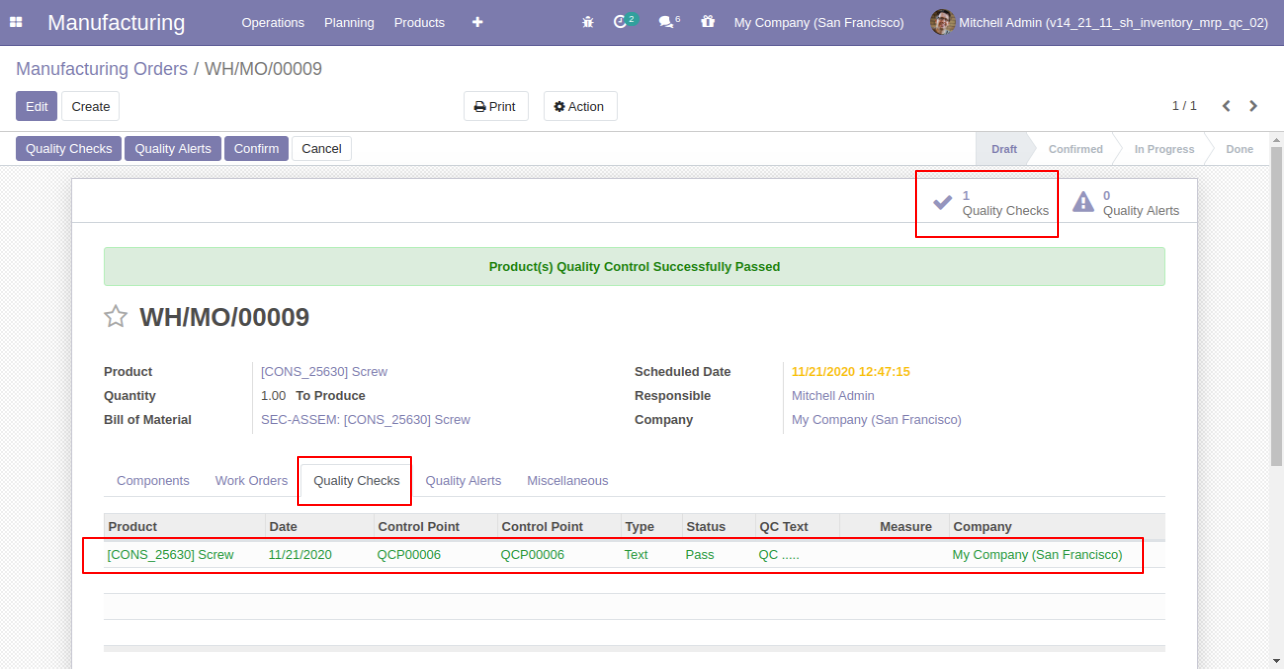
While clicking on "Quality Check" and check type "Measurement", In the wizard you have to add measurement in define criteria and click validate.
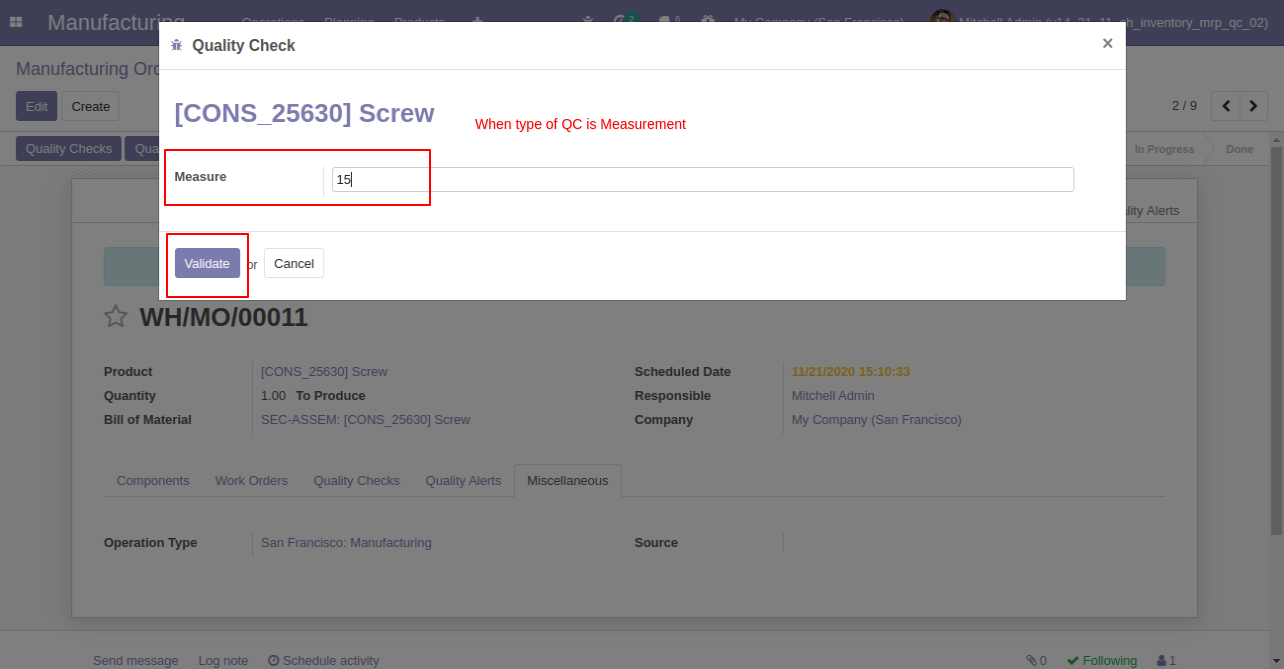
If enter measurement does not match criteria then it will popup this message where you have to select, If enter measurement is correct then click 'Confirm Measure' else click 'Correct Measure' and it will redirect to you on the previous popup.
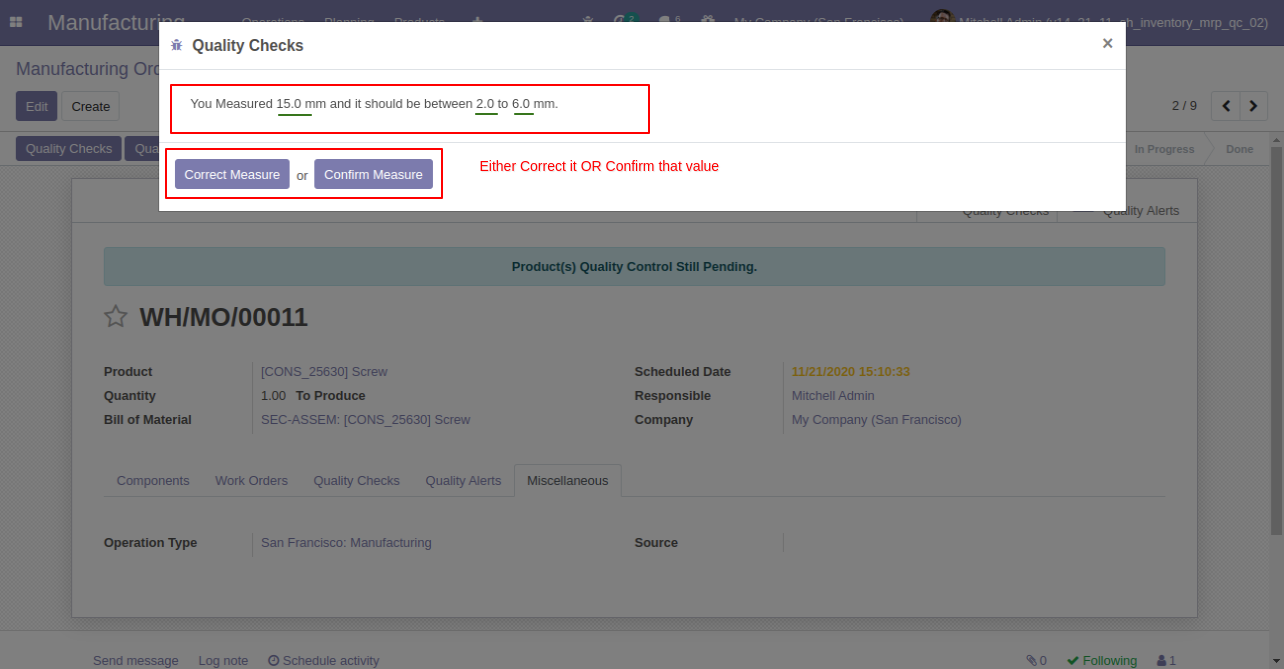
When your maximum number of quality check is exceeded that time this warning popup will display.
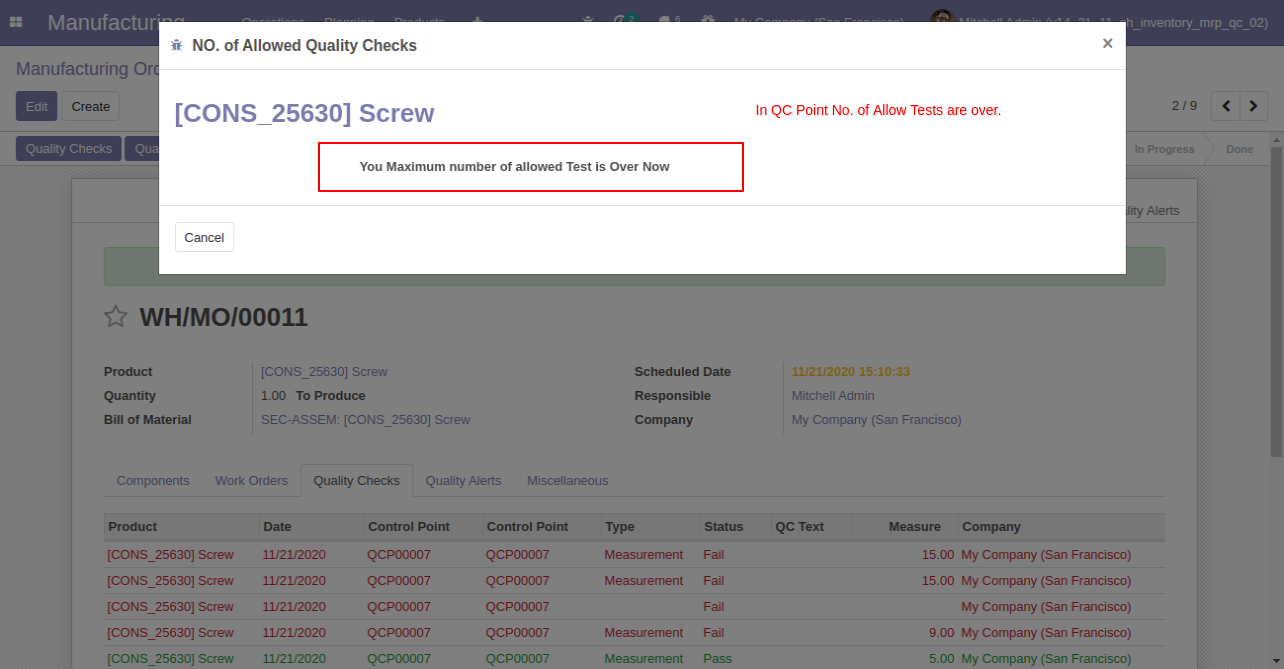
When Quality Check type 'Pass' or 'Fail'.
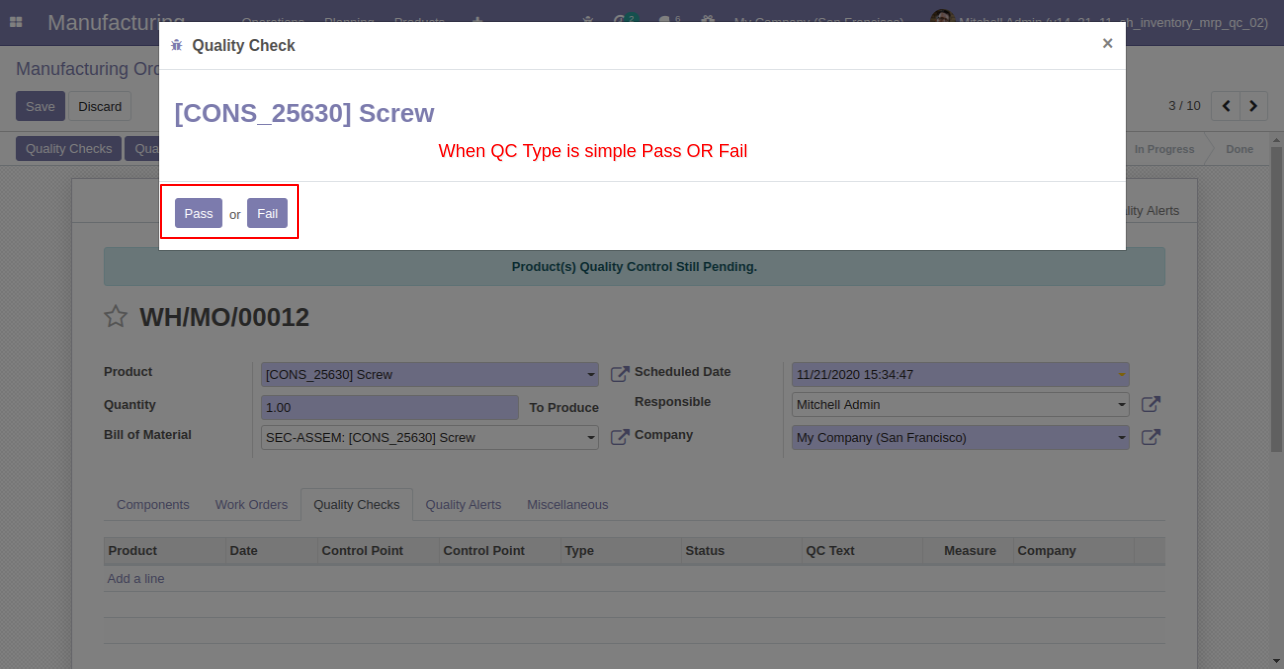
Quality Check Type "Take a Picture", Than responsible person has to add pictures of products.
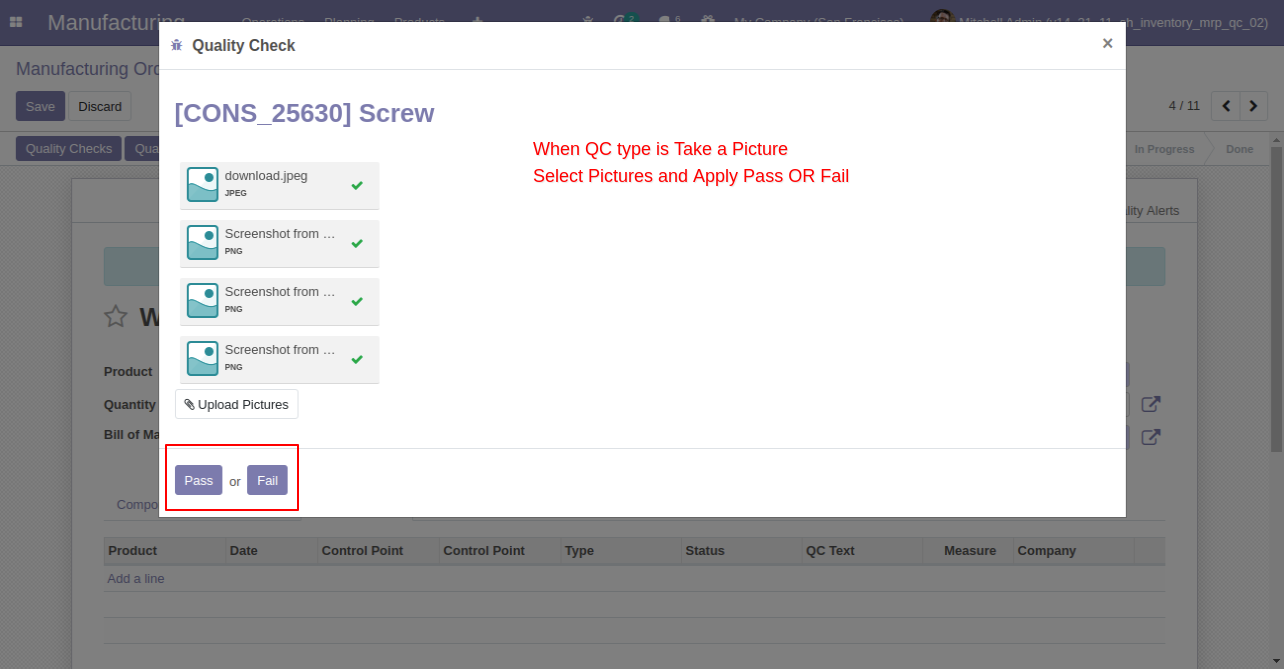
Here users have buttons for 'Quality Alert' and one tab also.
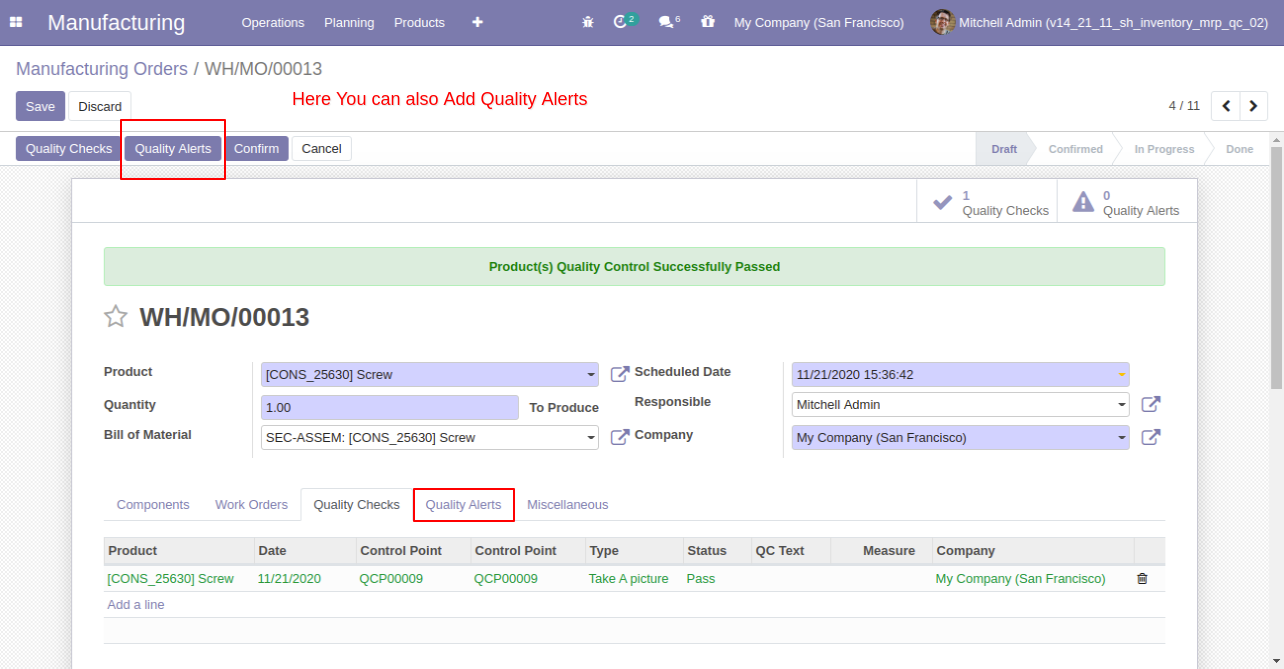
This is the 'Quality Alert' popup. Where you can see a list of all products and names of the responsible person, and priority.
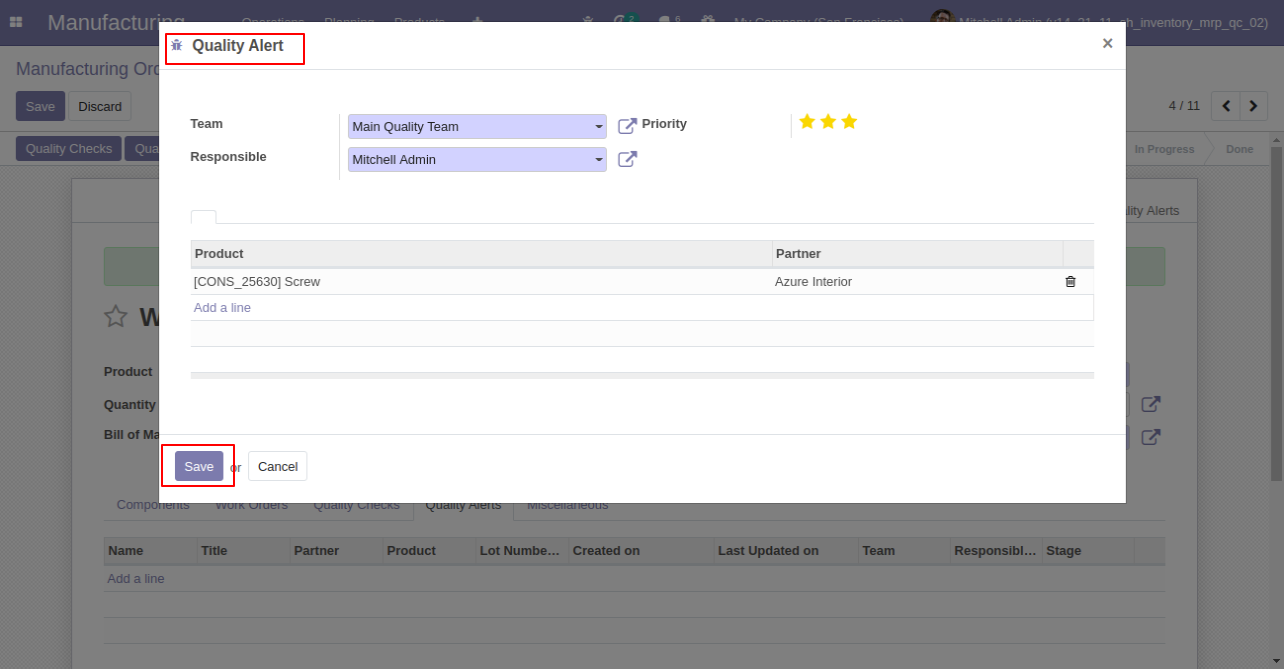
MRP Quality Alert Menu and Tree View. Where you can see the list of MRP's quality alerted.
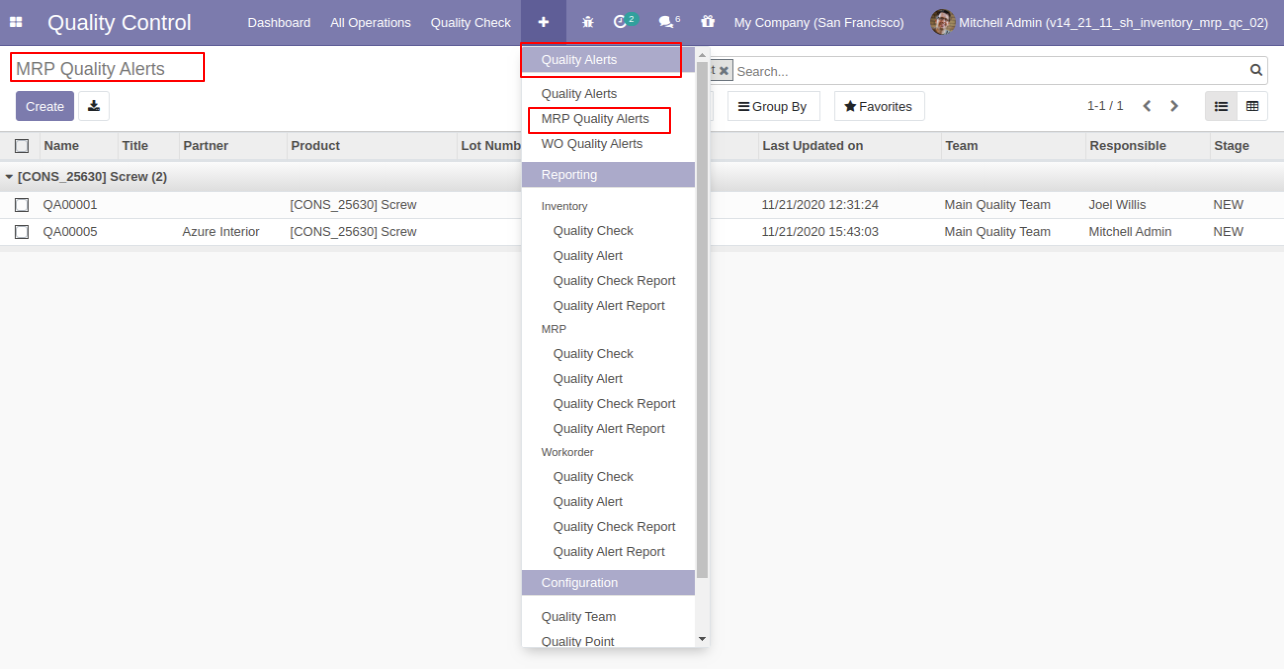
MRP Qulaity Alert Form View.
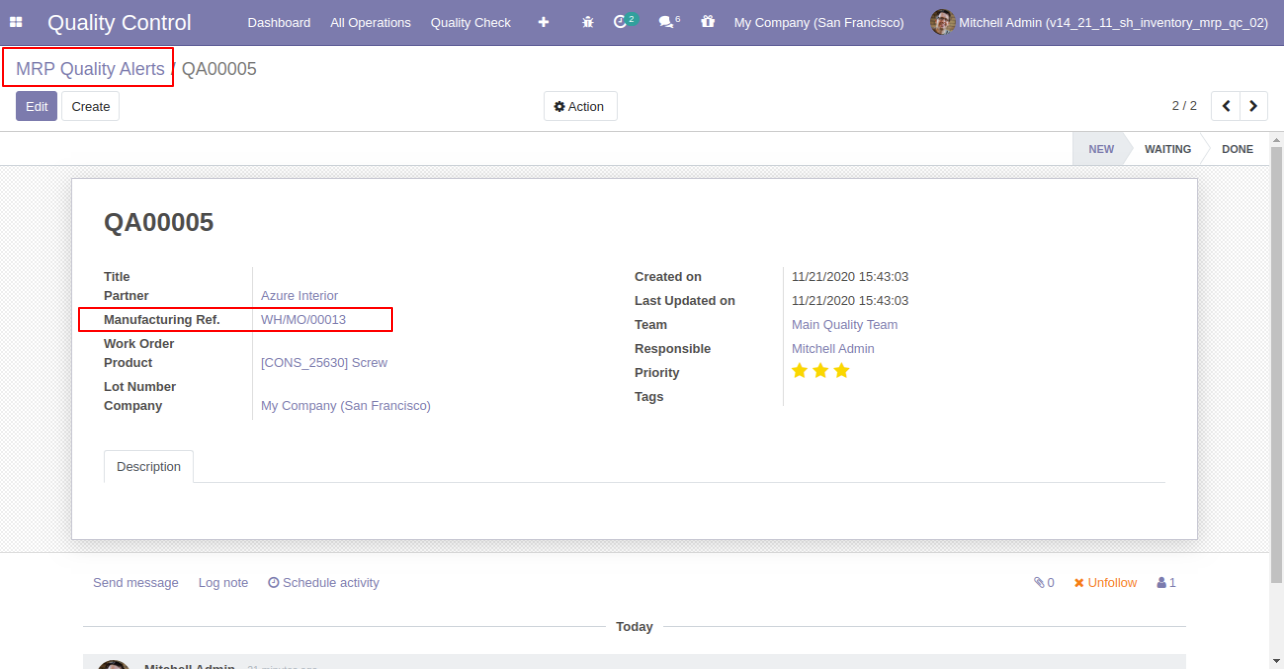
MRP Pending QC Menu and Tree View.
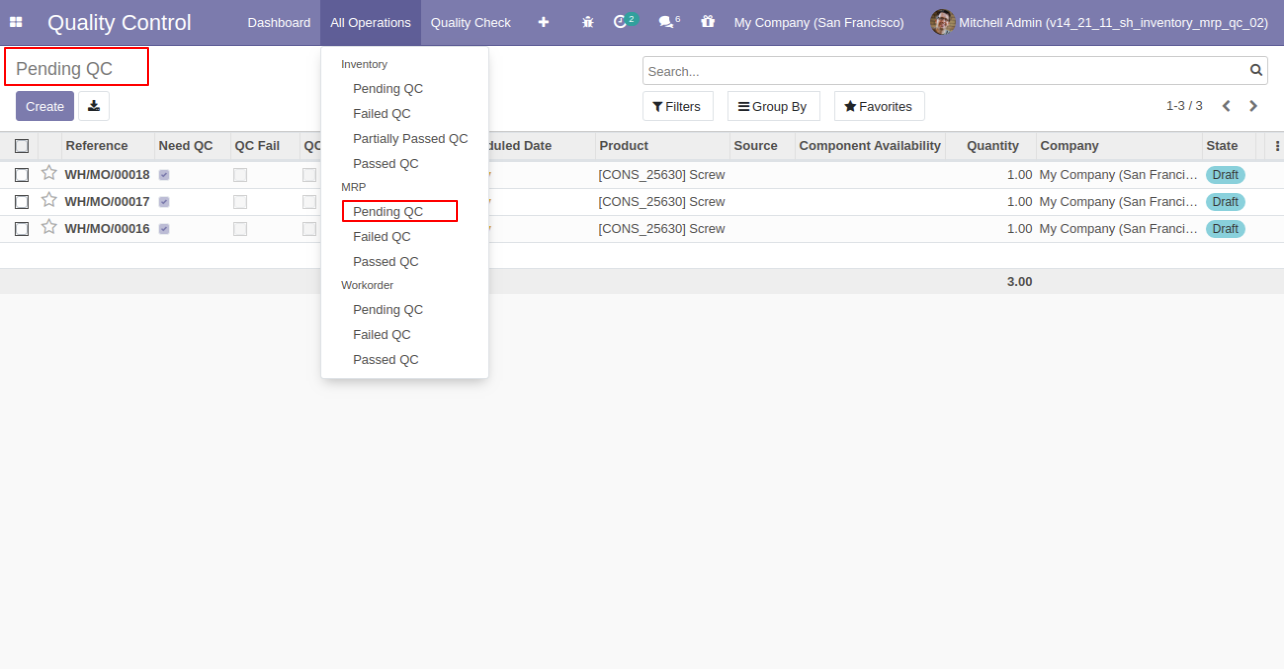
MRP Failed QC Menu and Tree View.
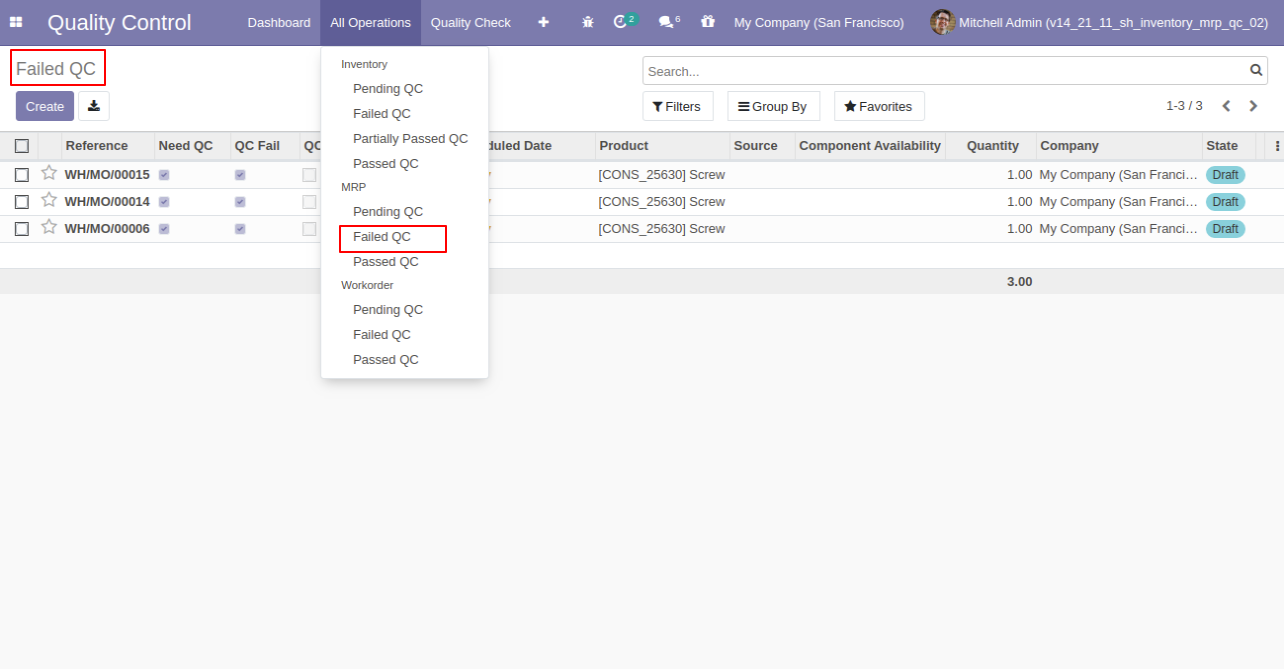
MRP Passed QC Menu and Tree View.
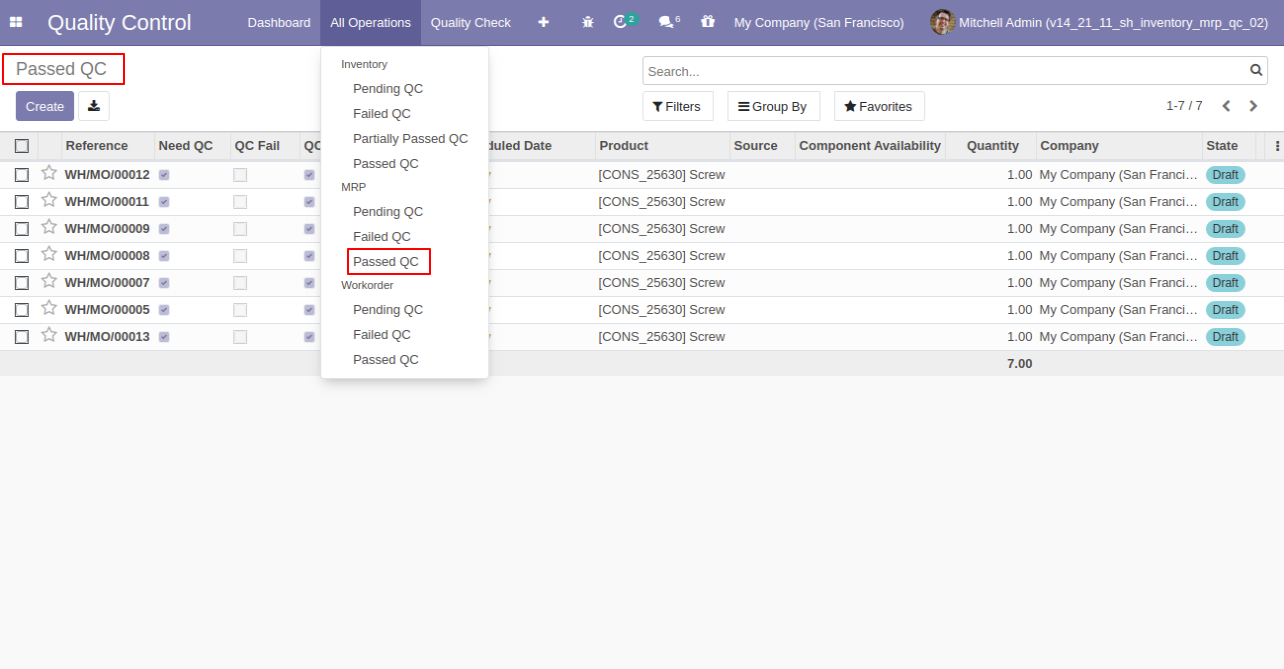
MRP Quality Check Menu and Tree View.
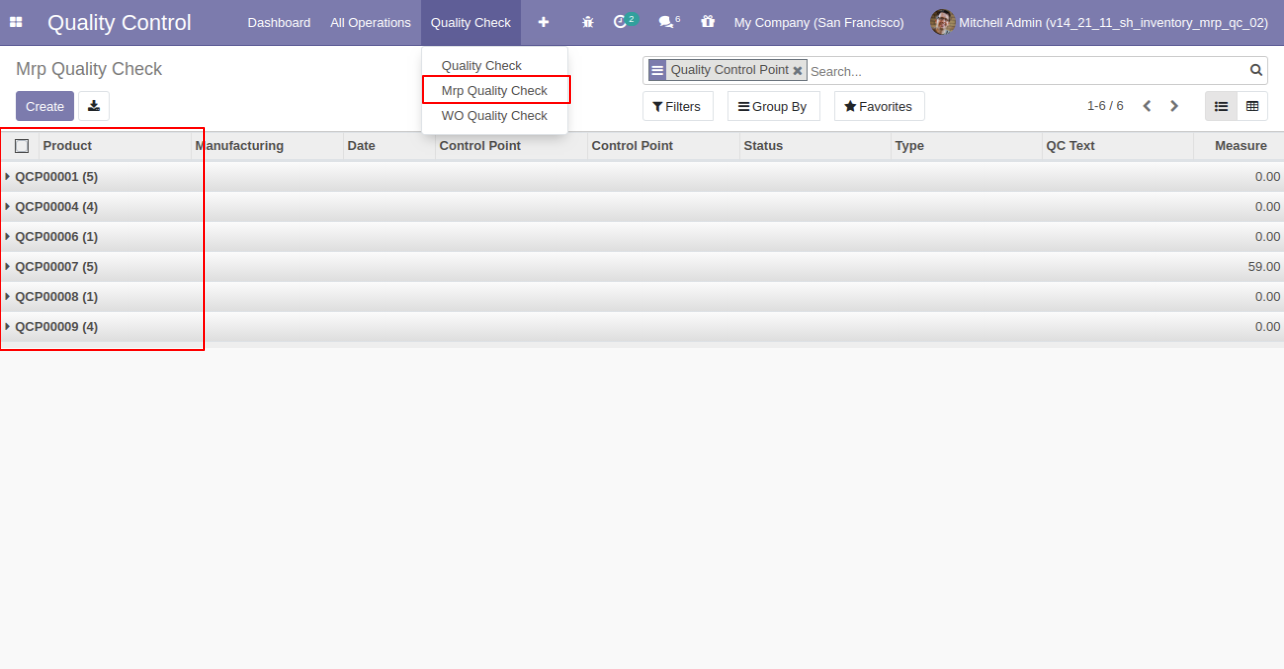
MRP Quality Check Form View.
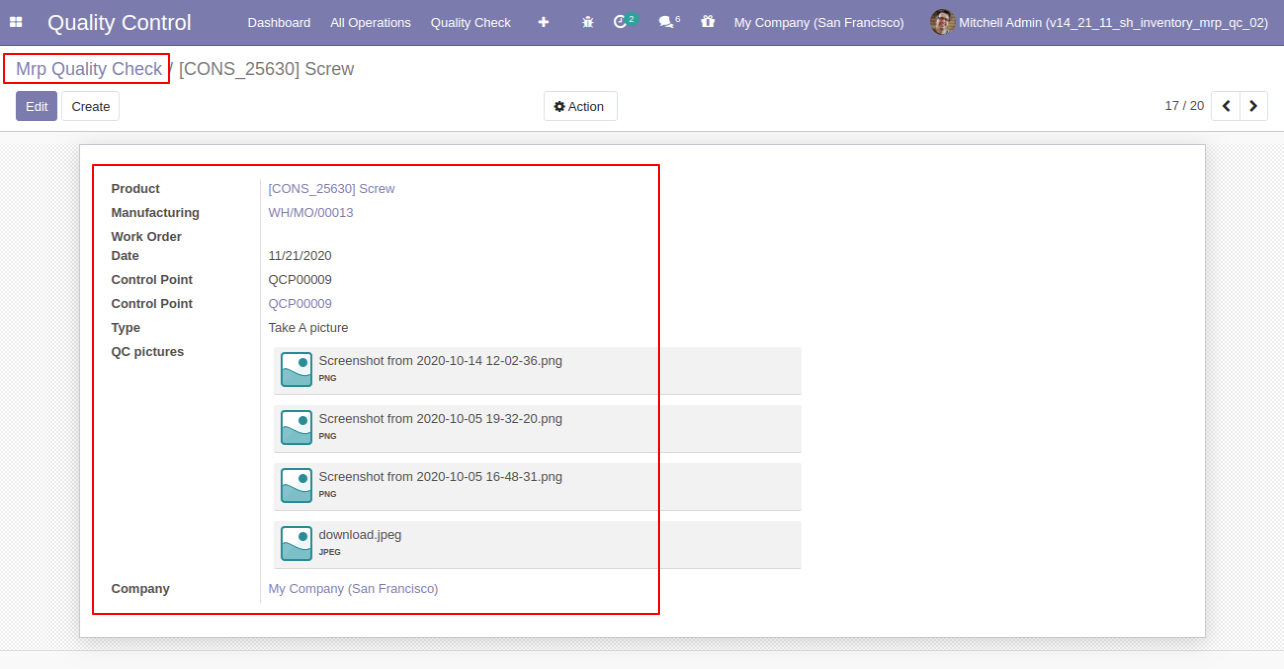
MRP Quality Check Analysis Report View.
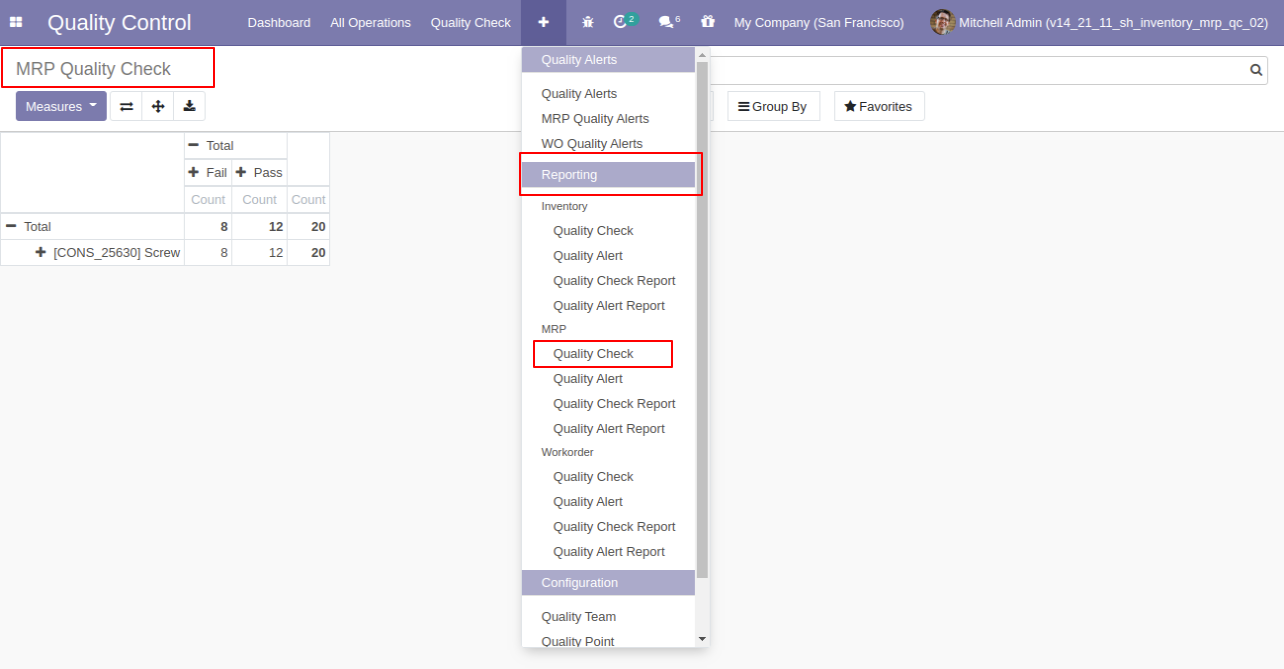
MRP Quality Alert Analysis Report View.
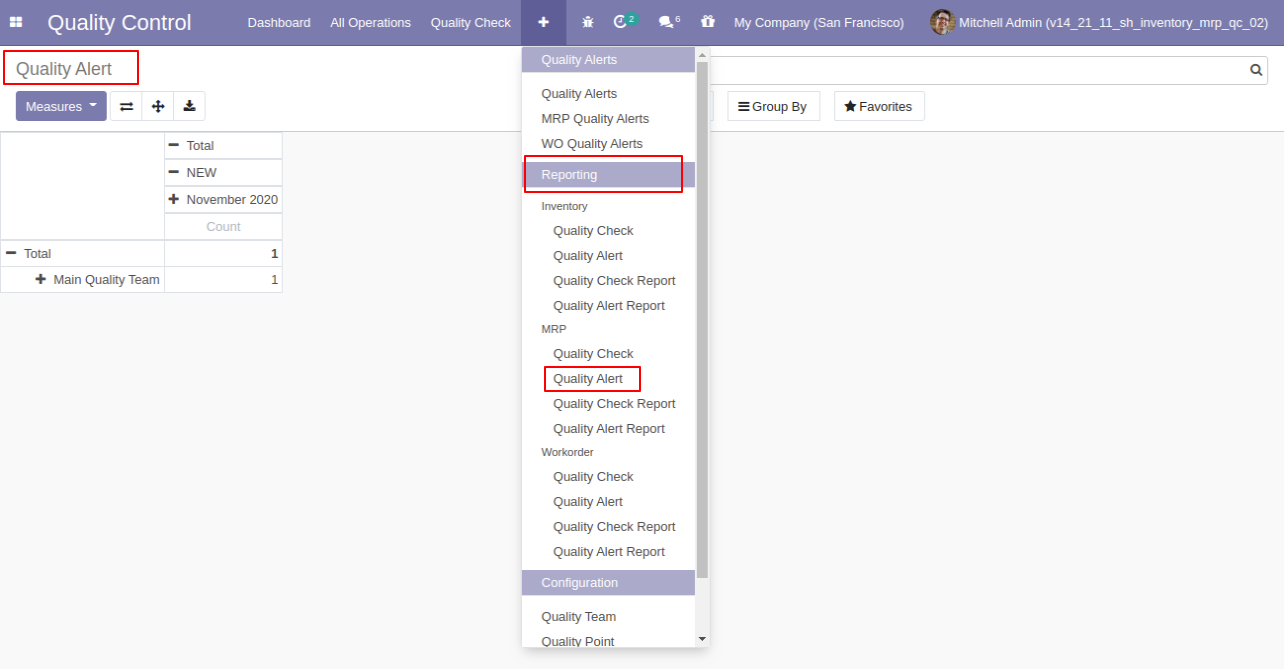
'Quality Check Report' for pdf report.
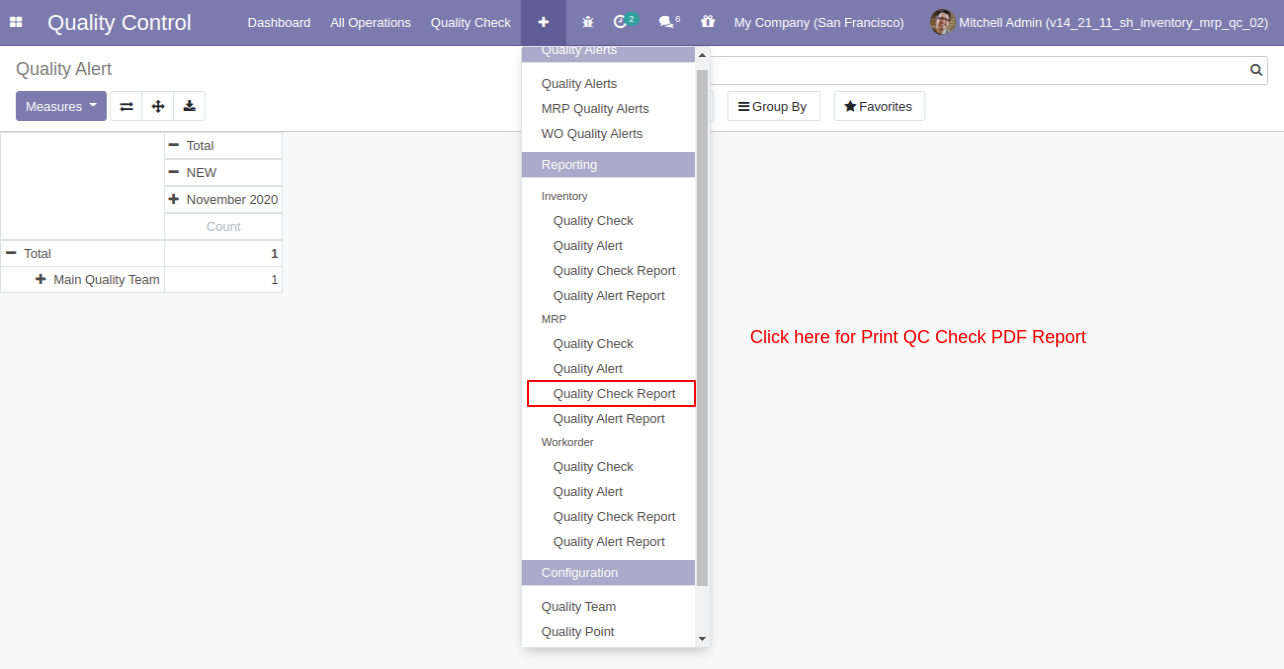
After click on 'Quality Check Report' this wizard will popup, select group by the operation and status both.
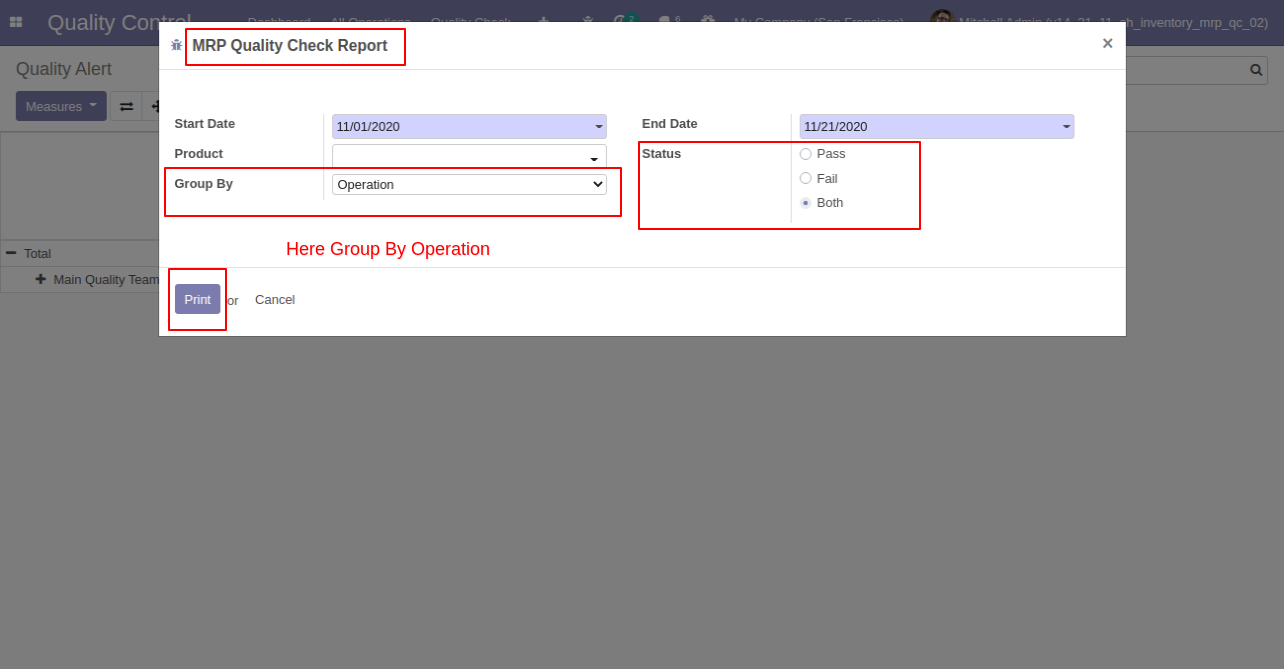
Quality Check PDF report with group by operation.
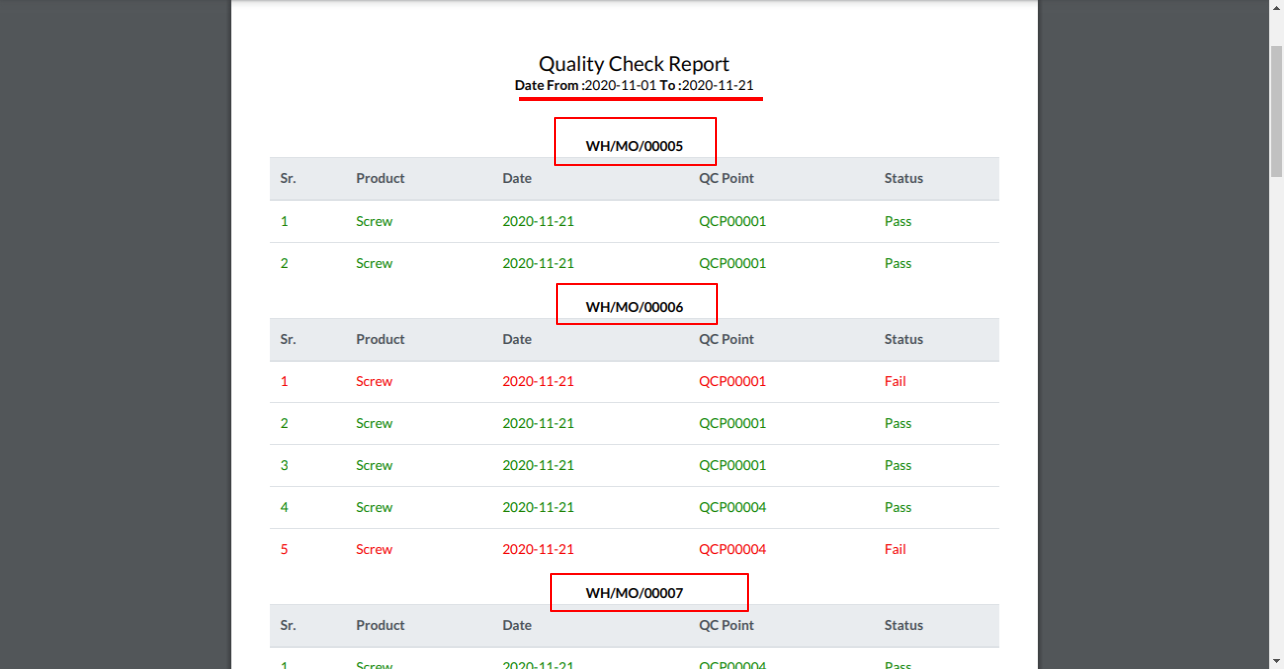
'Quality Check PDF Report' group by product and status both.
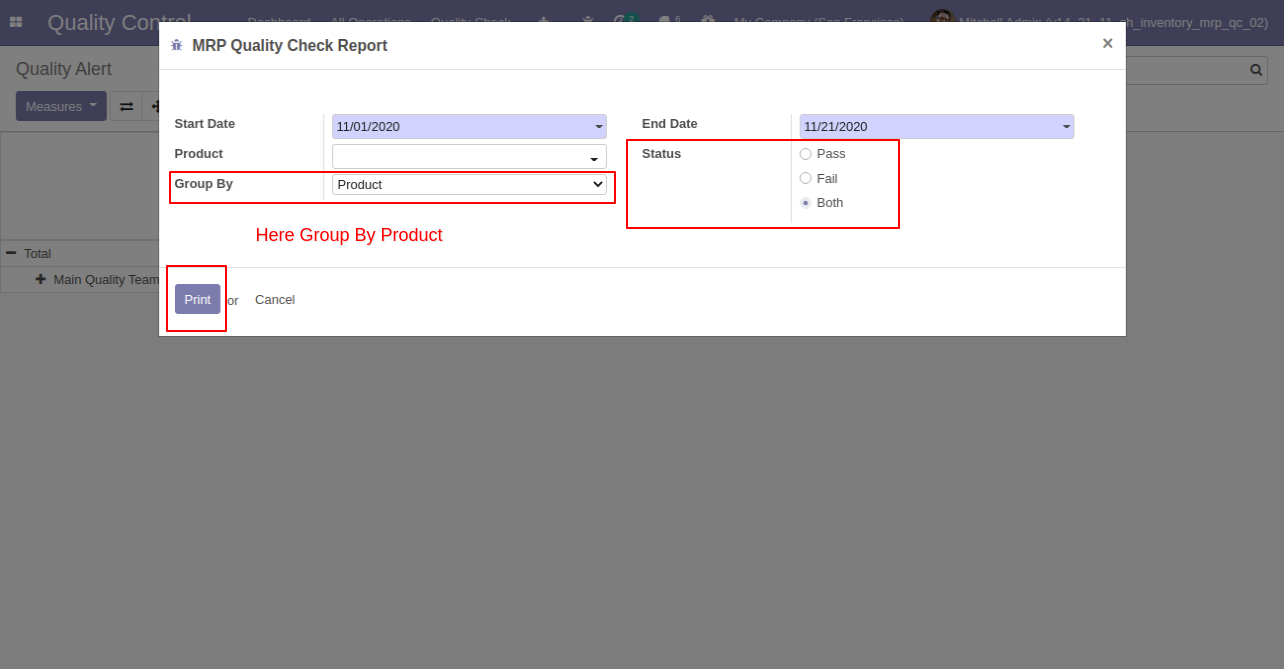
Quality Check PDF Report group by product.
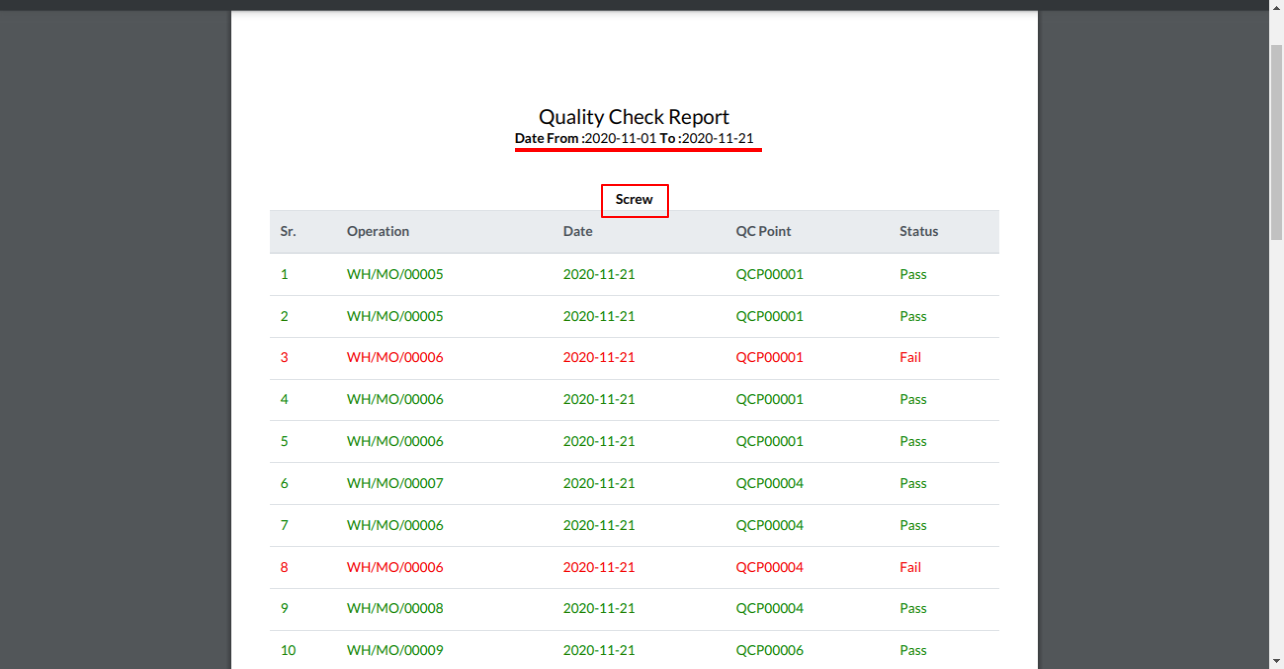
Quality Check PDF report with the only status pass.
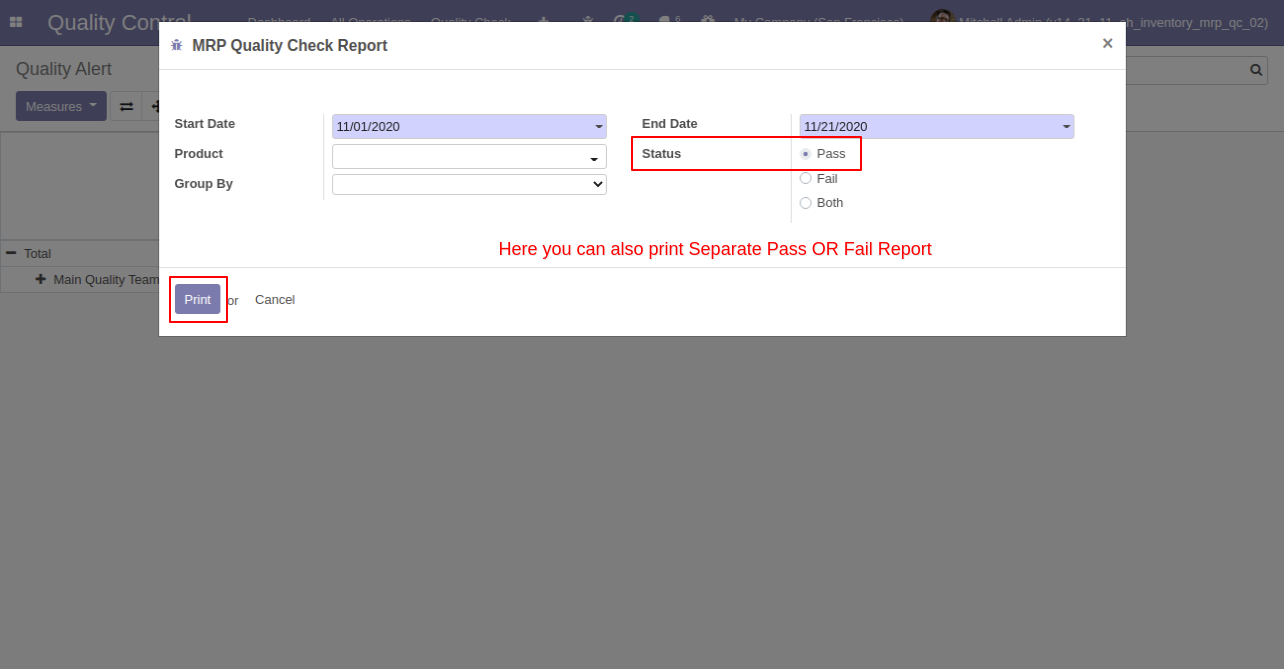
Quality Check PDF report for only pass status.
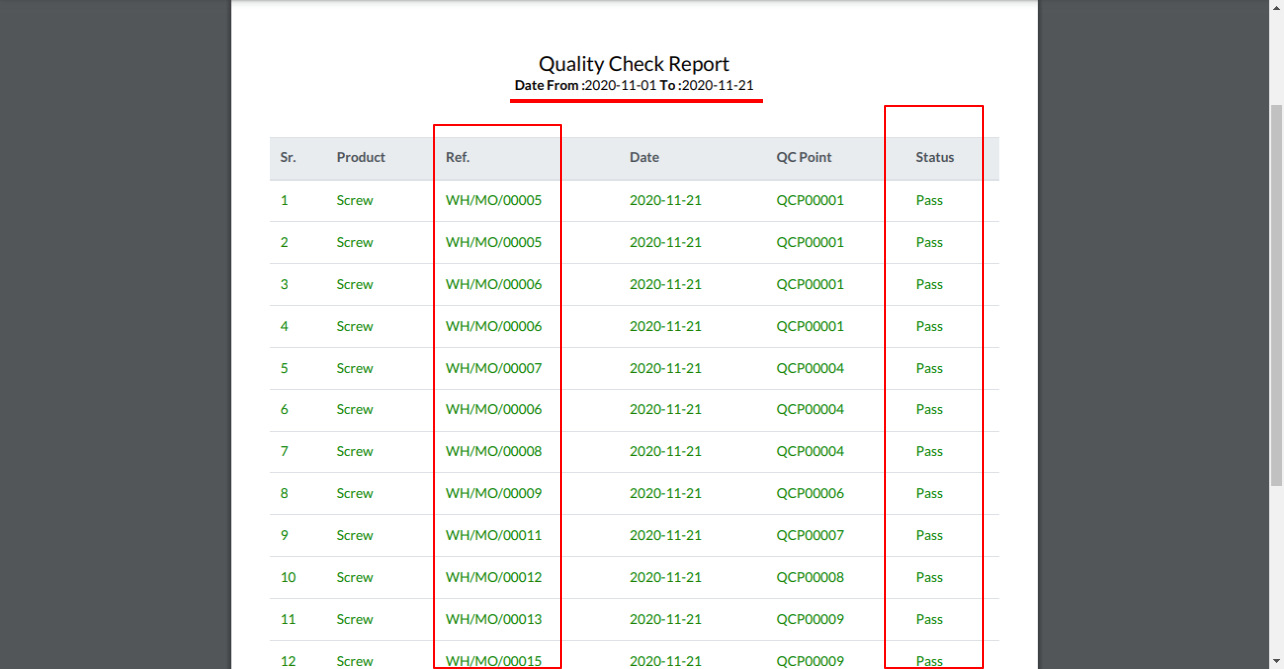
Quality Check PDF report for only fail status.
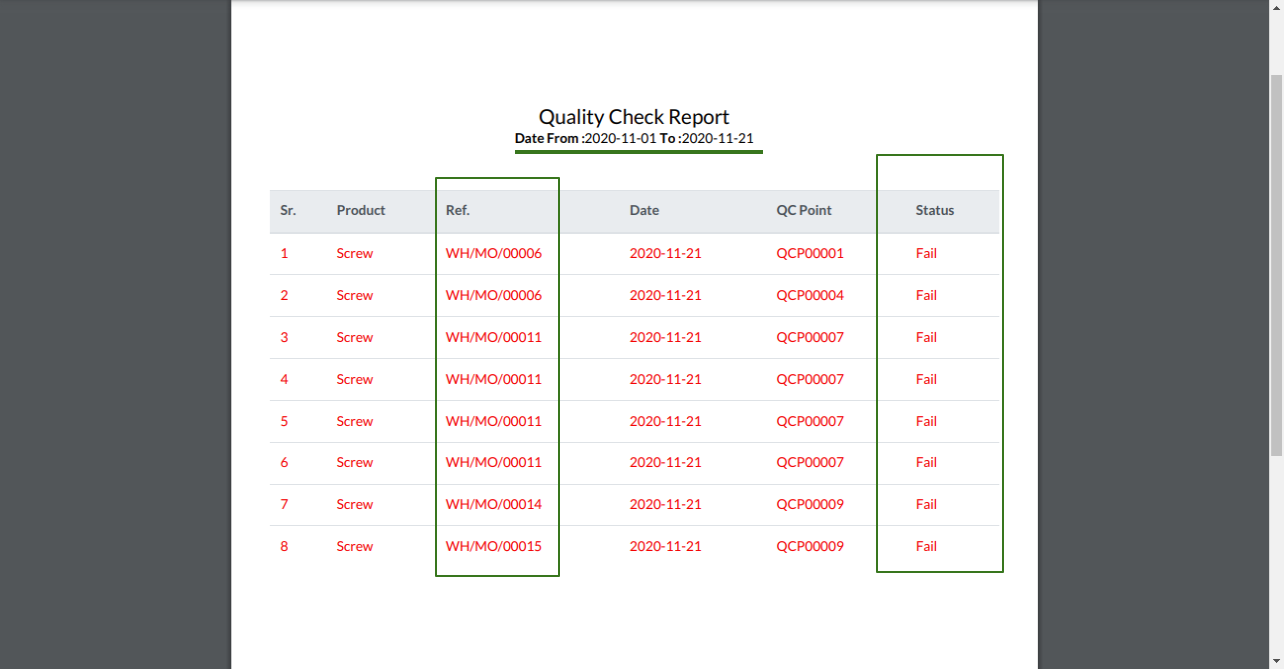
MRP Quality Alert PDF Report Action.
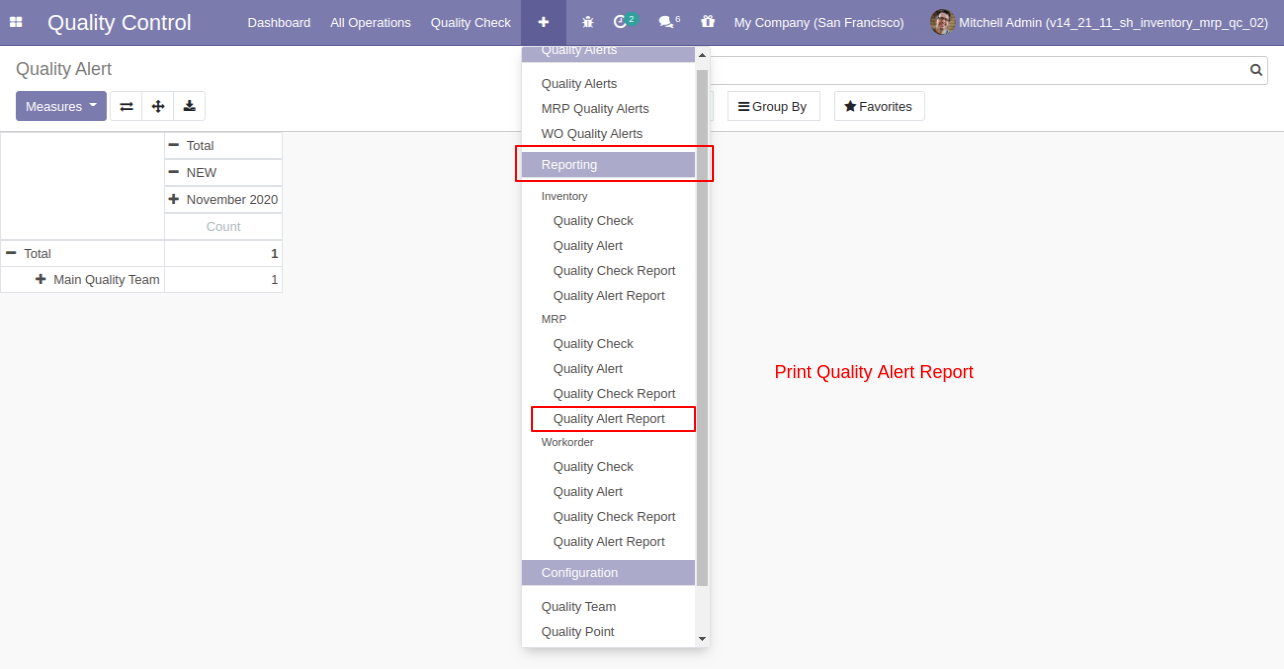
After click on 'Quality Alert Report' this wizard popup where you can filter and group by the report as per your requirements.
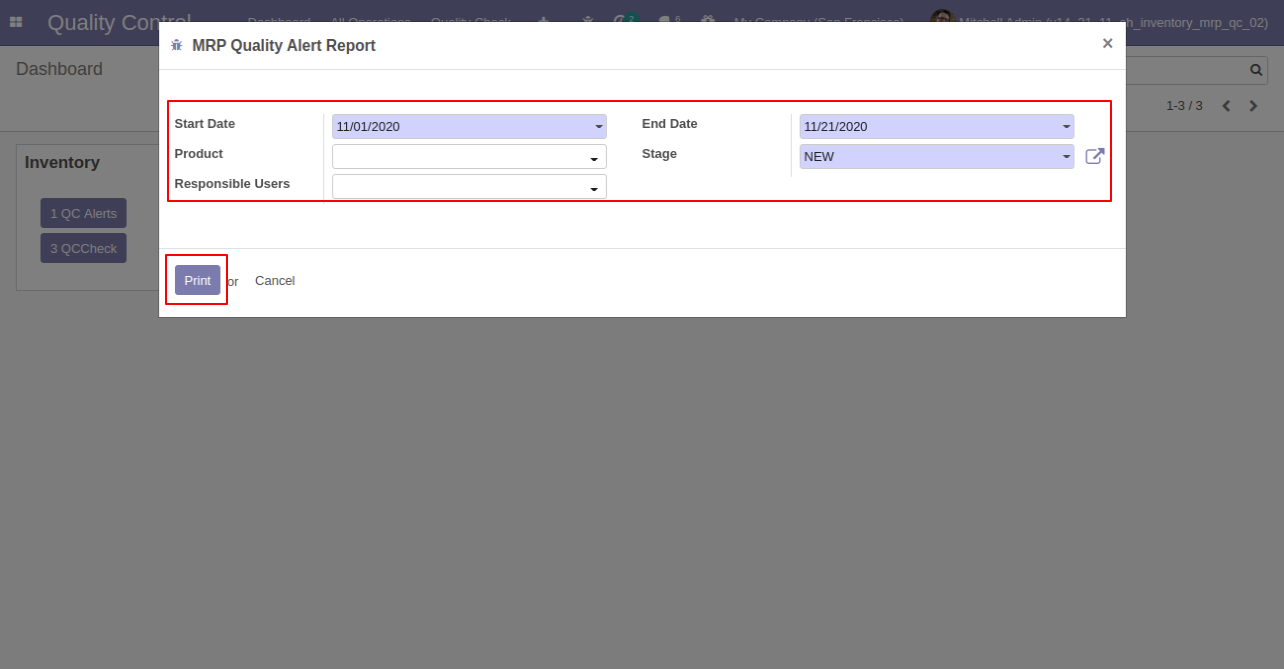
'Quality Alert PDF Report'.
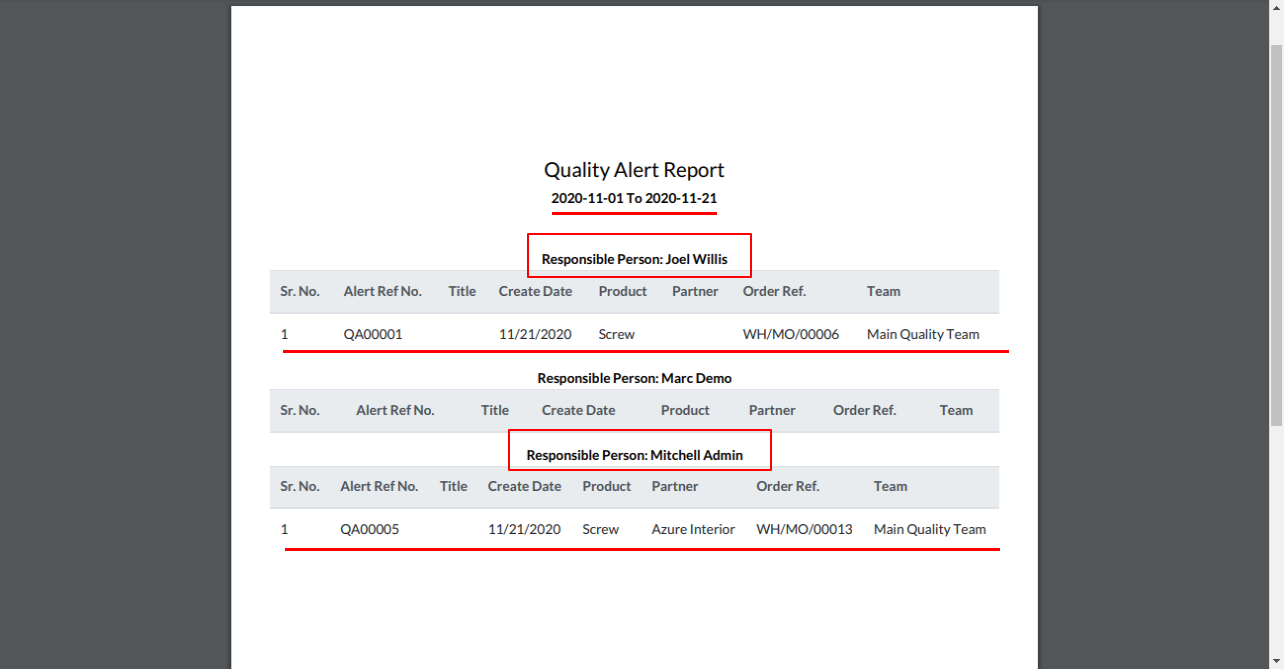
Make QC point for the multiple products and multiple operations.If qc is mandatory then check right QC Mandatory box. Assign QC team here.
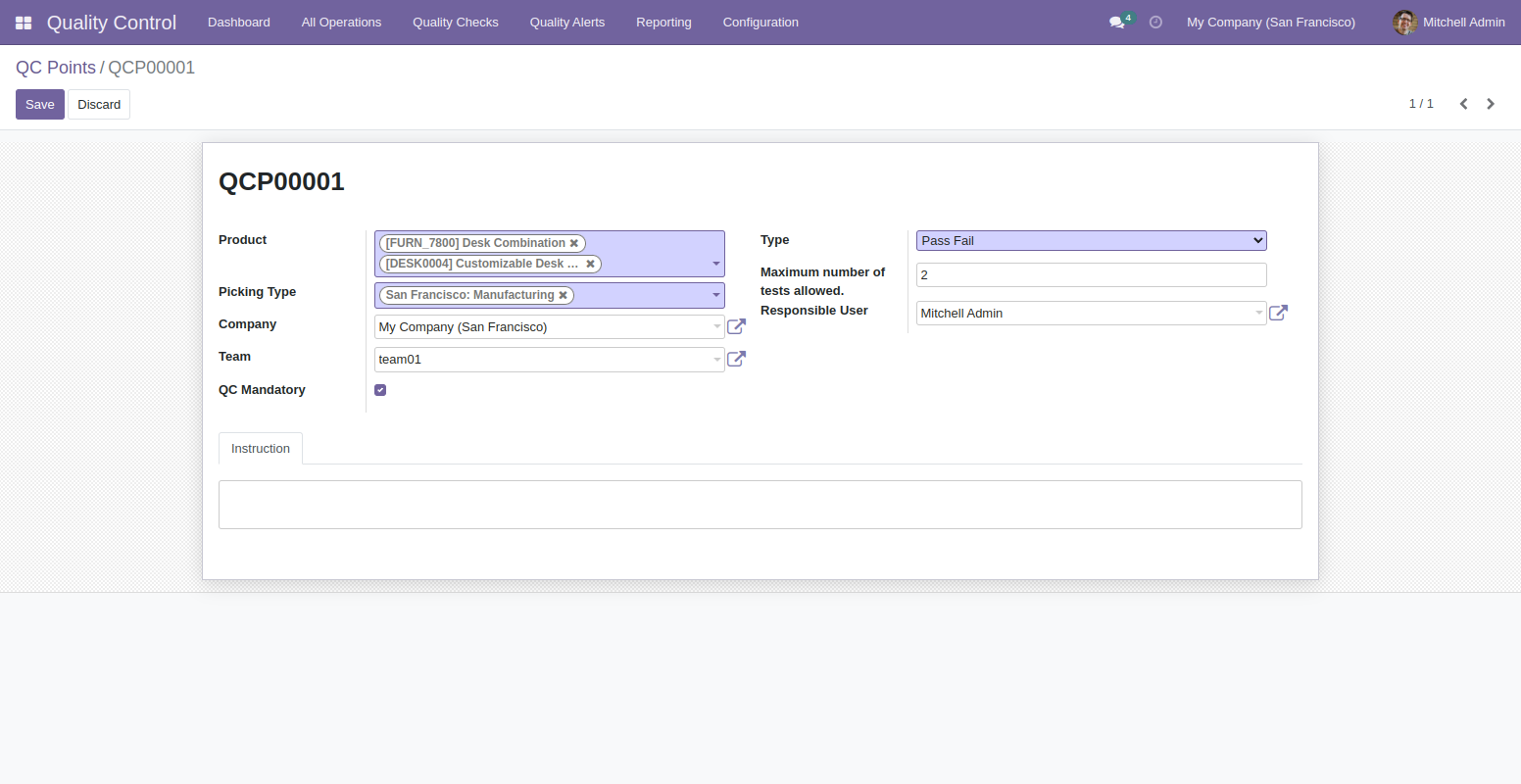
\ After Manufacturing order in in progress stage Quality check and Quality Alert button invisible.

In work-order 'Done' button is invisible until the QC is not done.
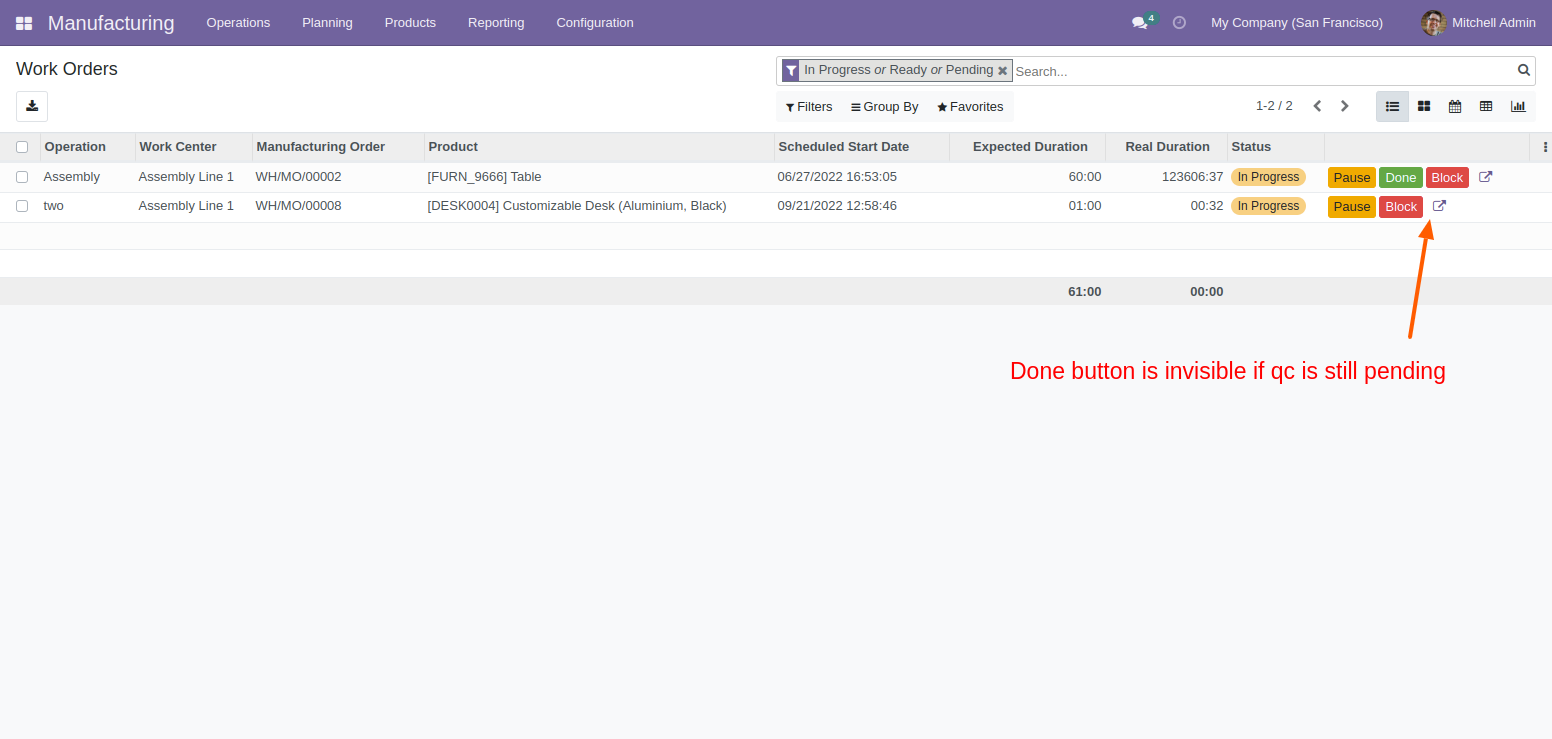
Click on external link button, here you can see the quality check and quality alerts visible for workorder
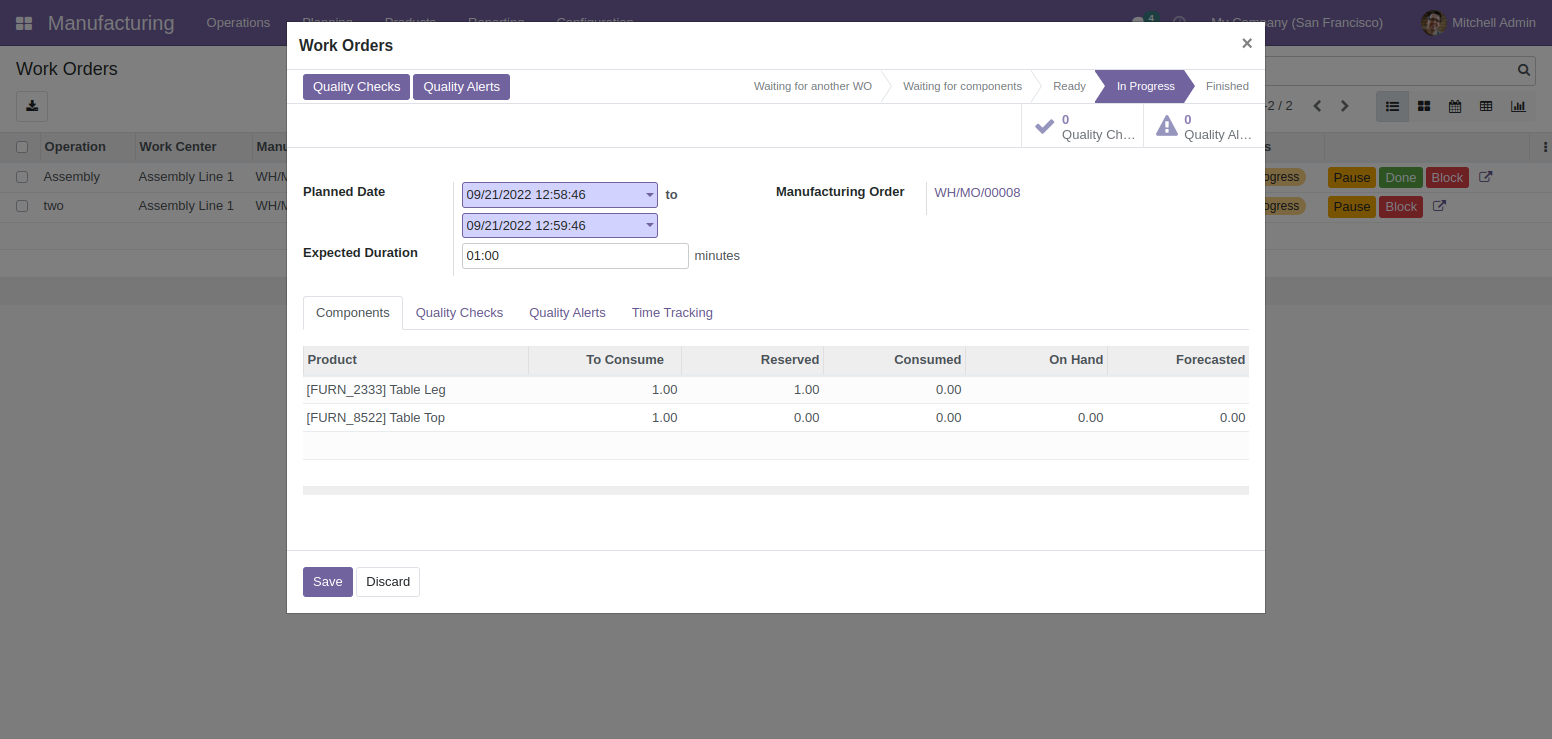
After click on quality check, Quality control wizard open and add quality measurements here.
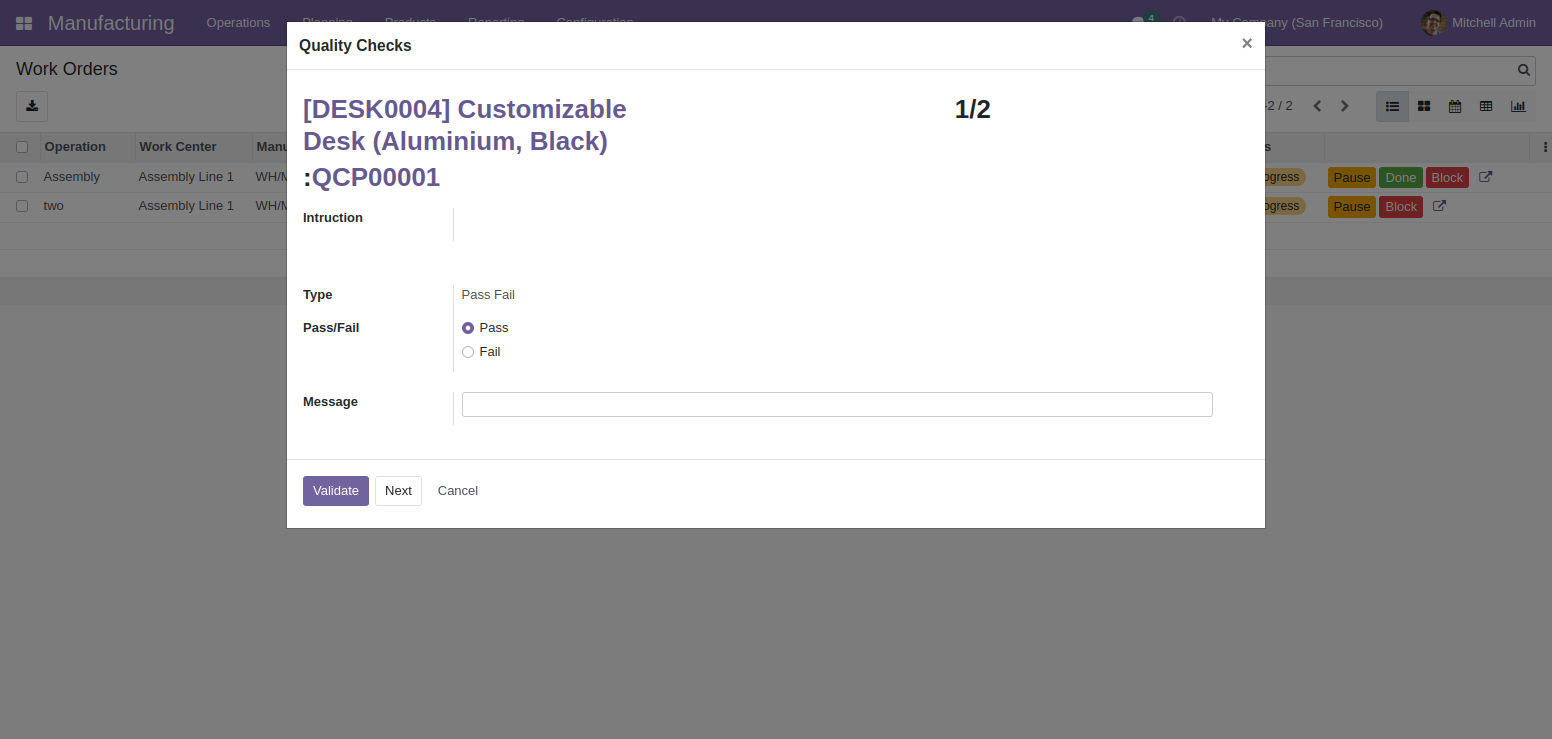
Another quality control wizard open on click 'Next' button because we set maximum 2 quality test allowed.
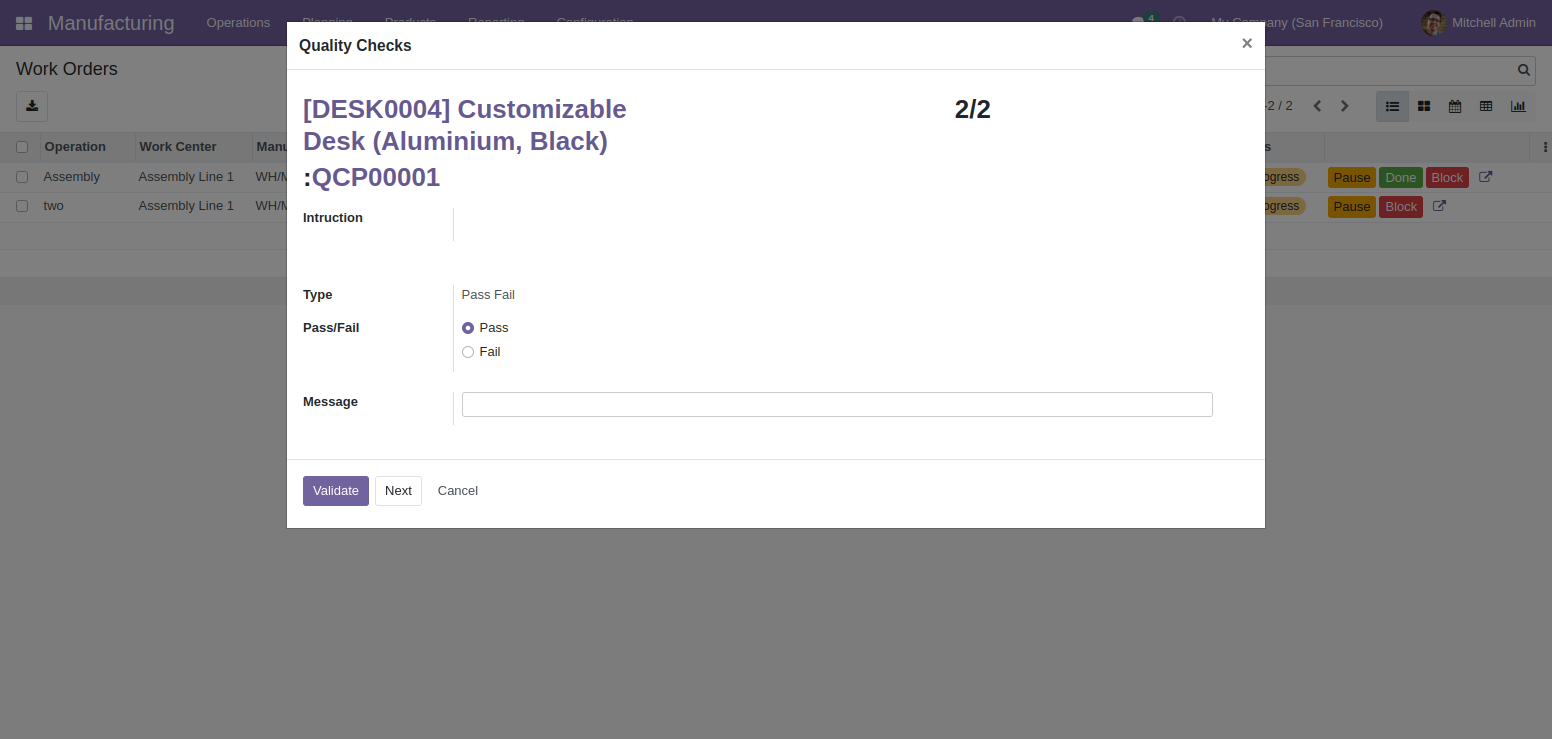
Once quality check done, you can see the done button visible in work order.
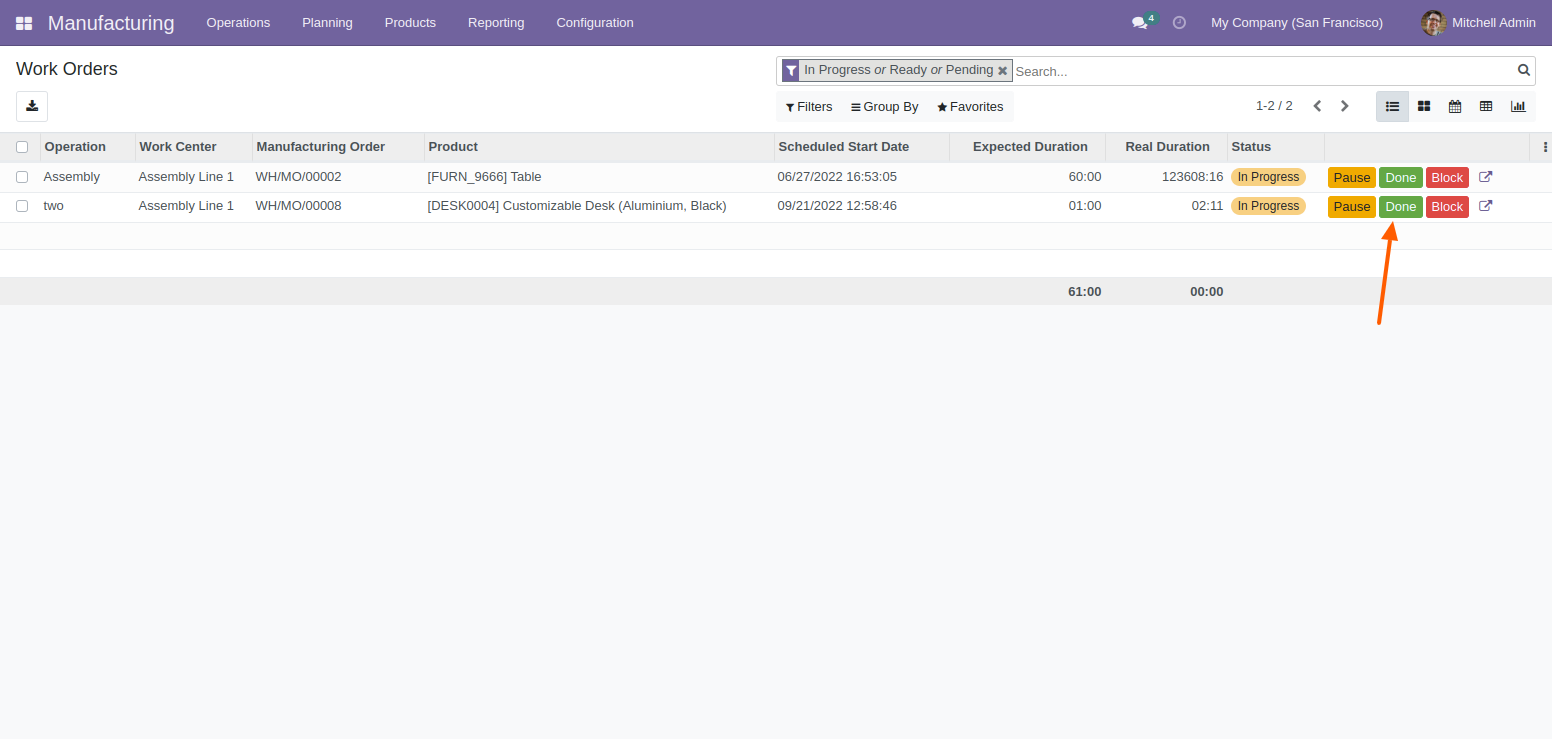
Once Workorder quality check done you can see the Quality check and Quality Alert button visible in manufacturing order.
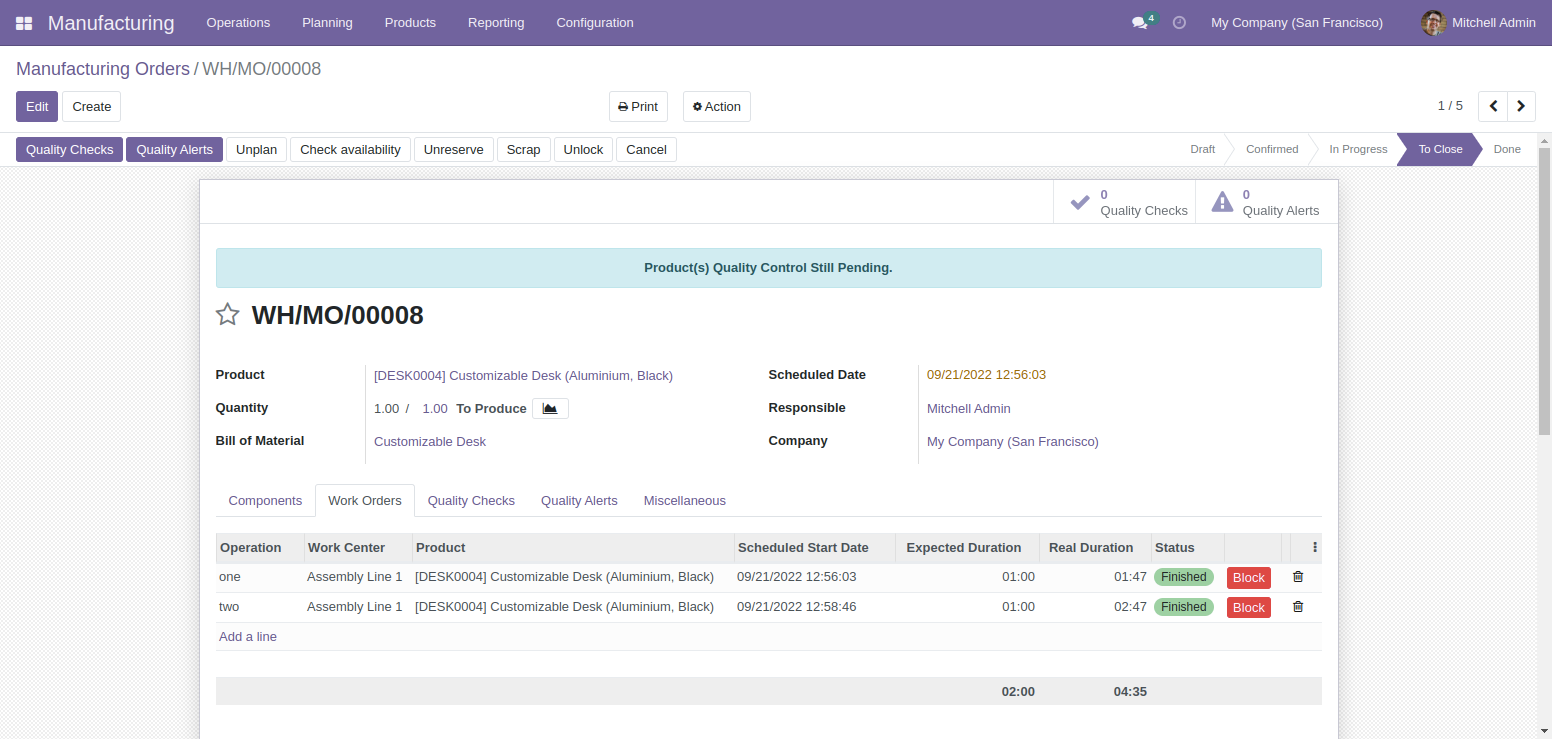
Just check the quality of manufacturing orders.
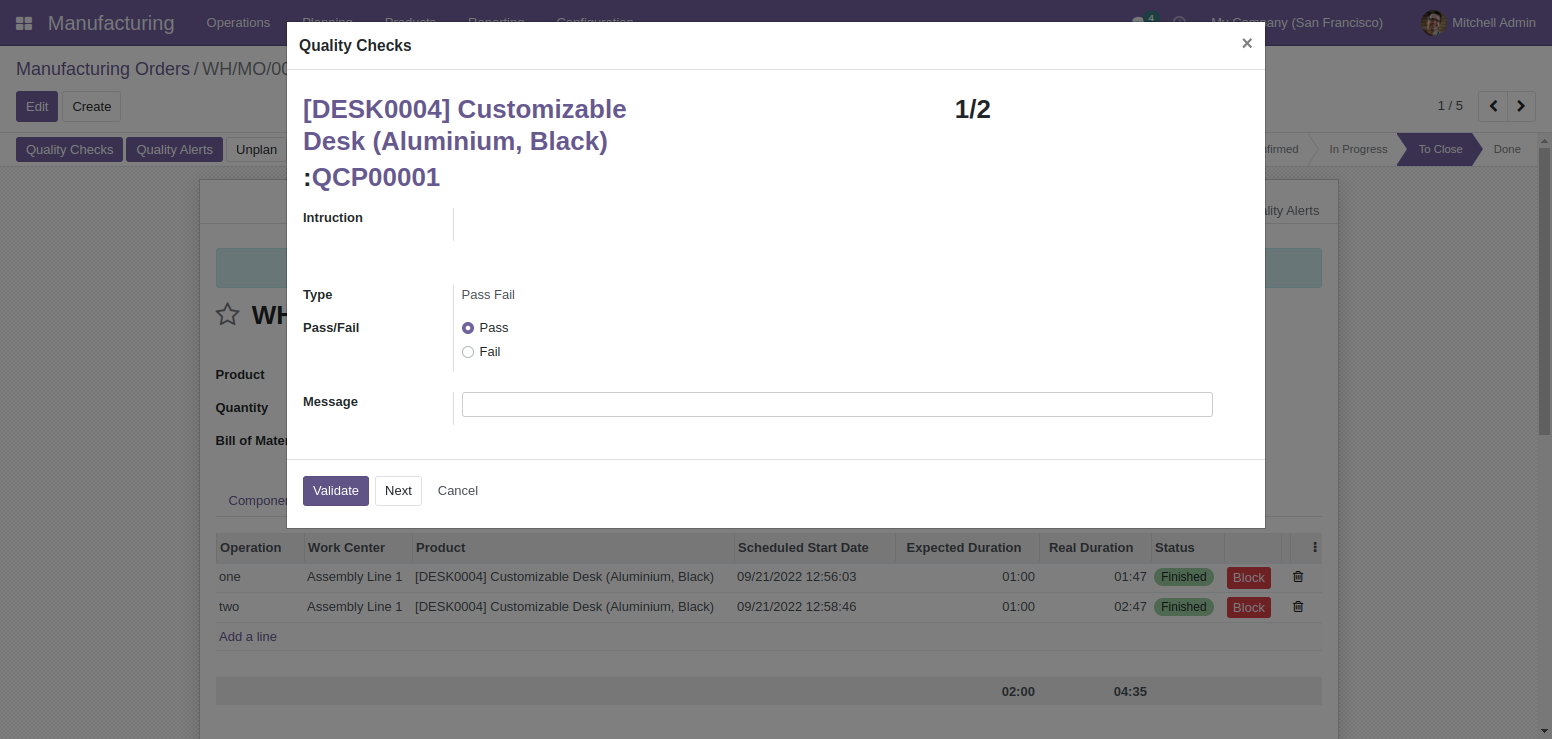
Just check the quality of manufacturing orders.
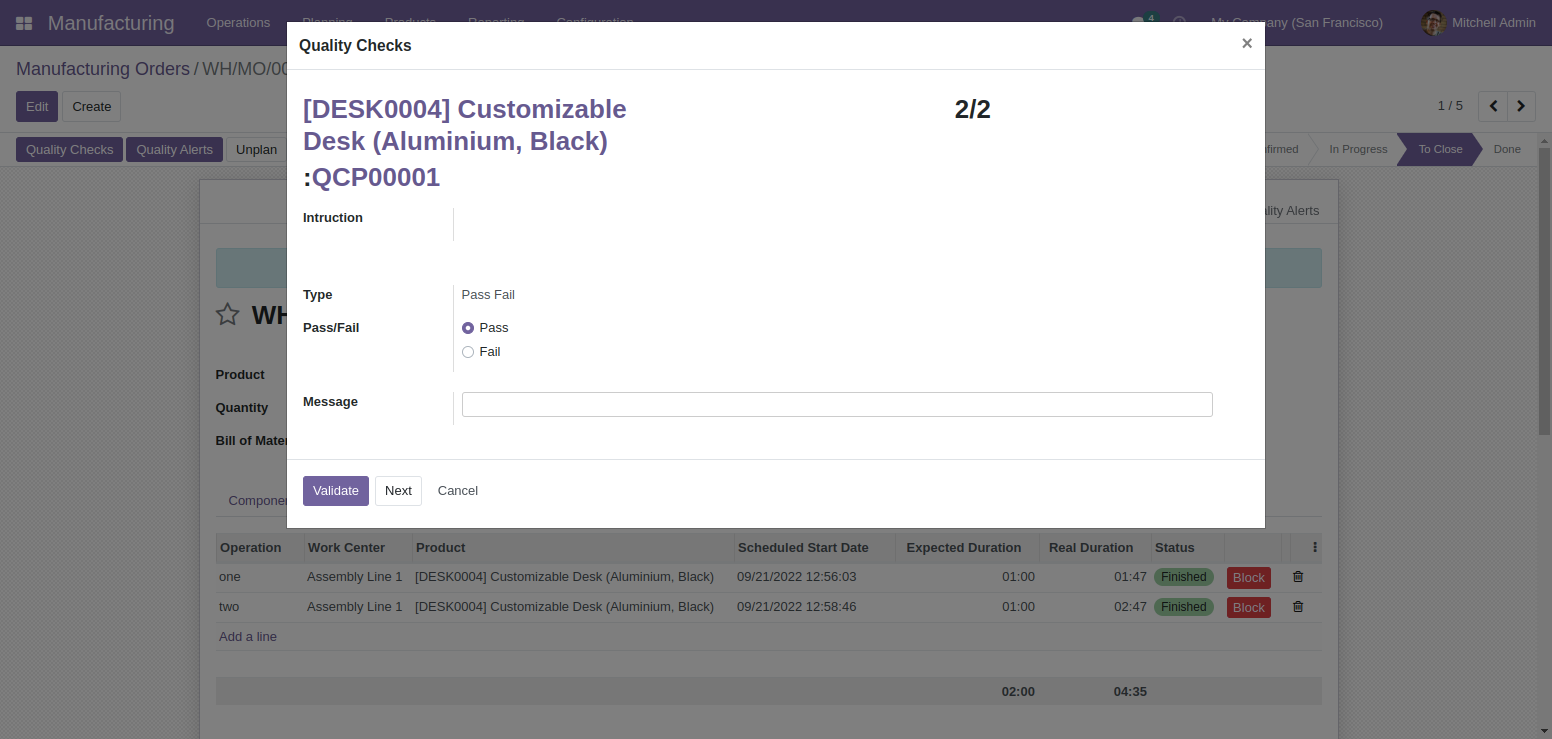
Once quality check done, you can see the done button in manufacturing order.
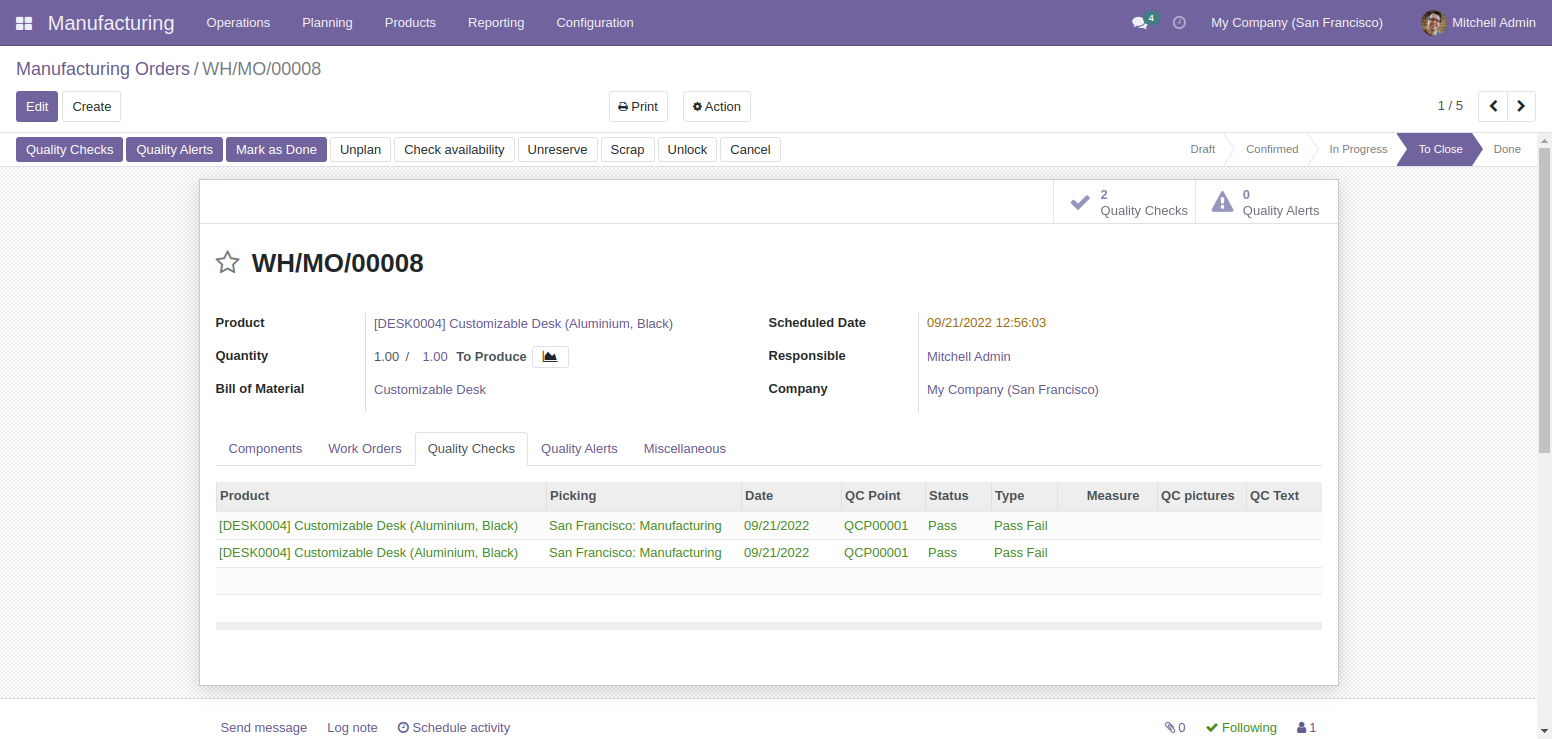
In Quality Point you have to set product and piking type manufacturing.
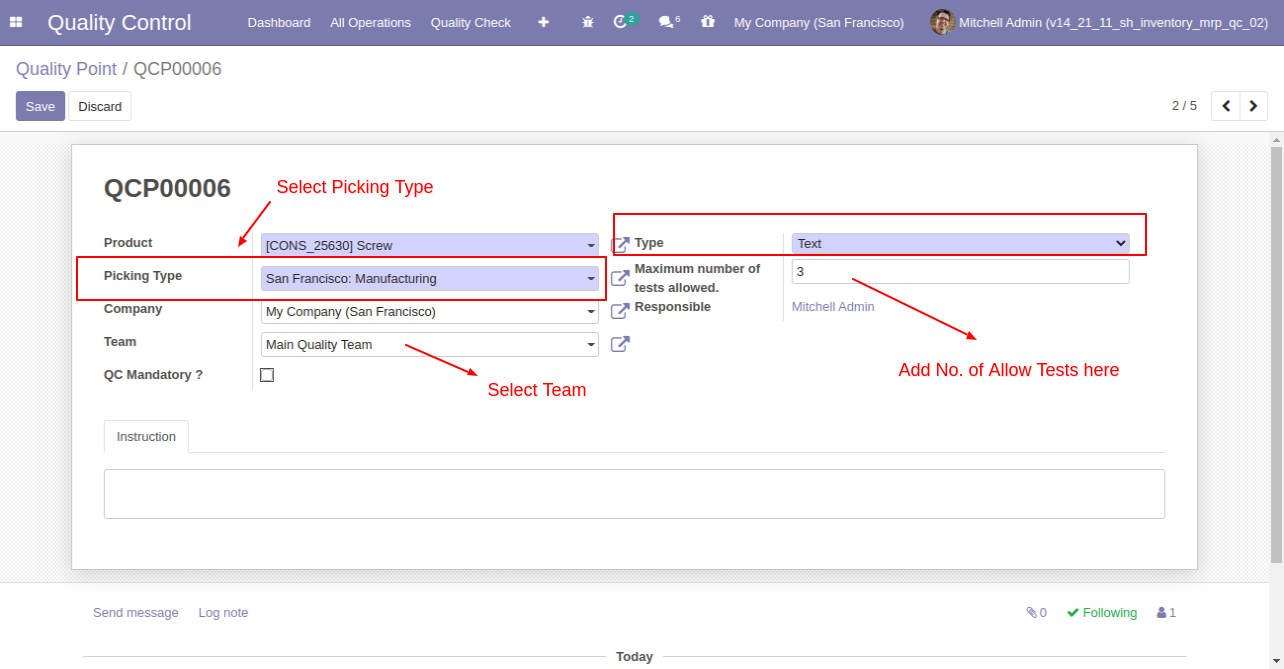
In work orders form view, there are two buttons "Quality Alerts" and "Quality Check", there are two smart buttons as you can see the quality alert and quality check, also see a global alert warning label on form top. There are two tabs for Quality Alert and Checks.
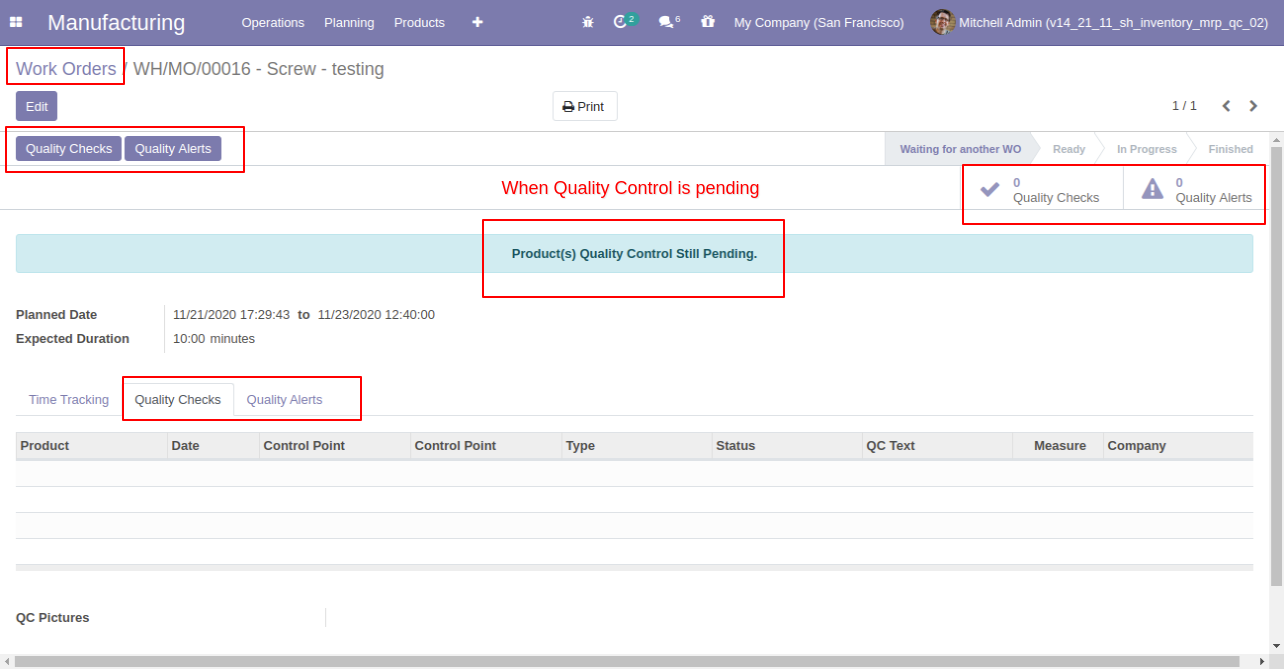
After clicking on the quality check, If check type 'Text Only' and click pass or fail.
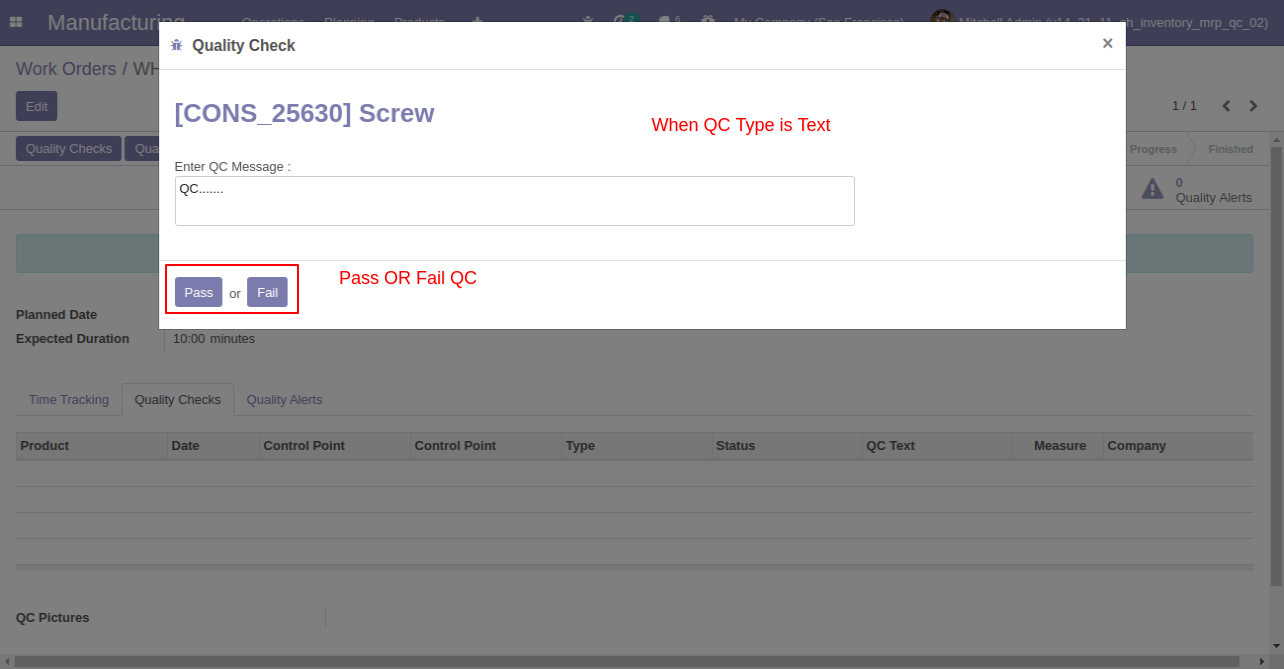
If the quality check passes then in the tab 'Quality Checks' that product line will glow green.
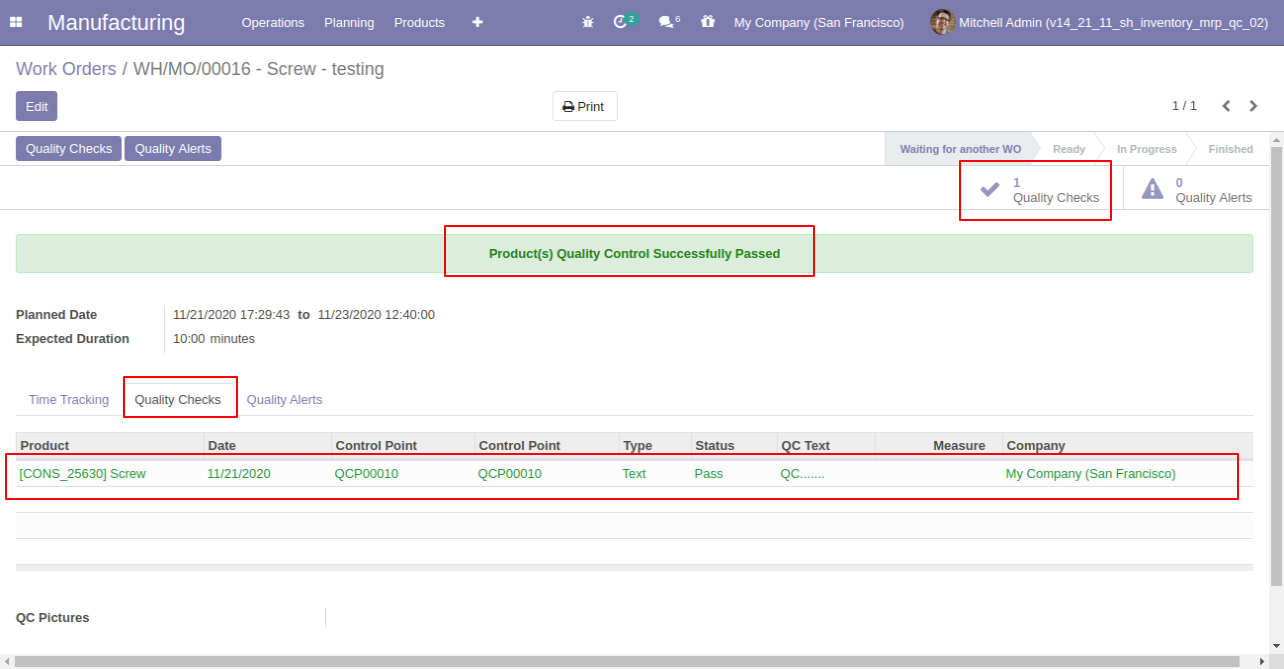
If quality check type 'Measurement' than a responsible person has to add the measurement of product quality.

When your maximum number of quality check is exceeded that time this warning popup will display.
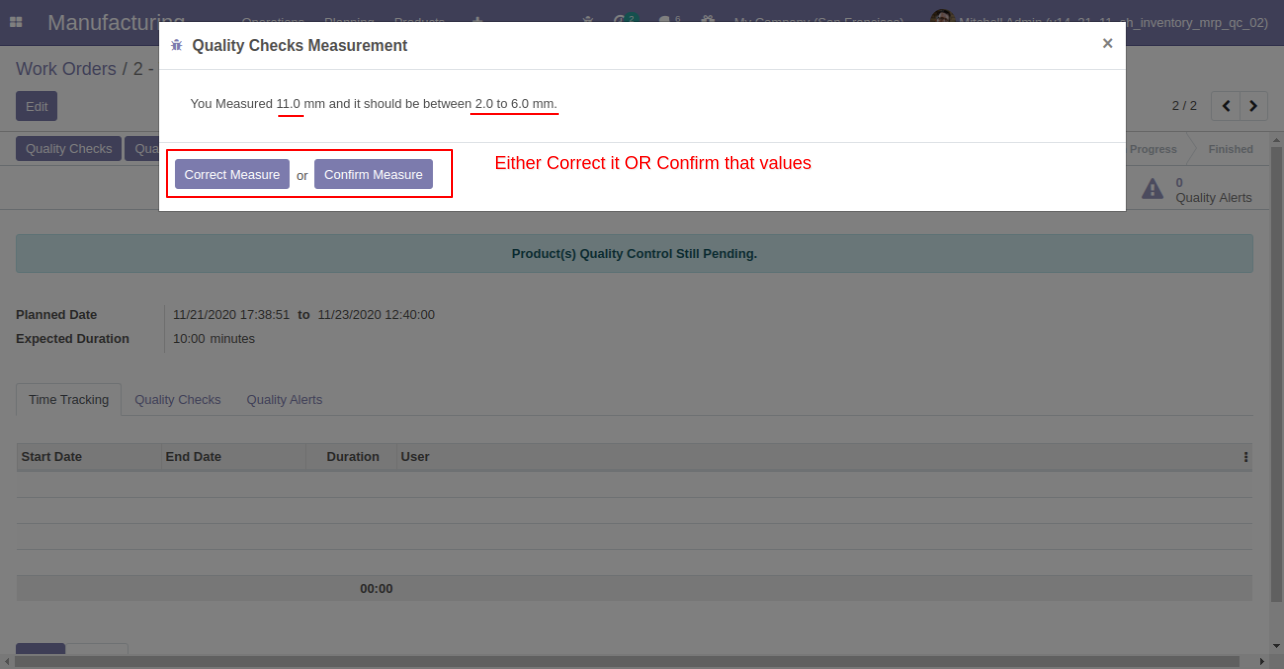
When Quality Check type 'Pass' or 'Fail'. A responsible person has to just click "Pass or Fail".
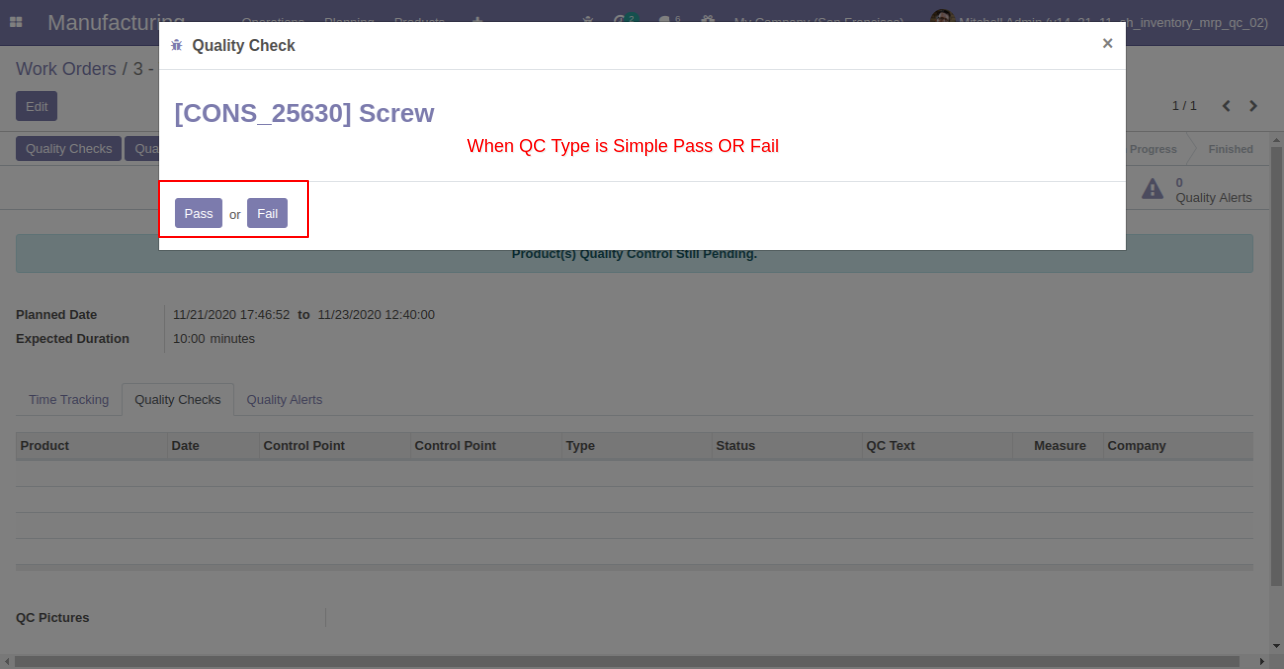
Quality Check Type "Take a Picture", Than responsible person has to add pictures of product quality.
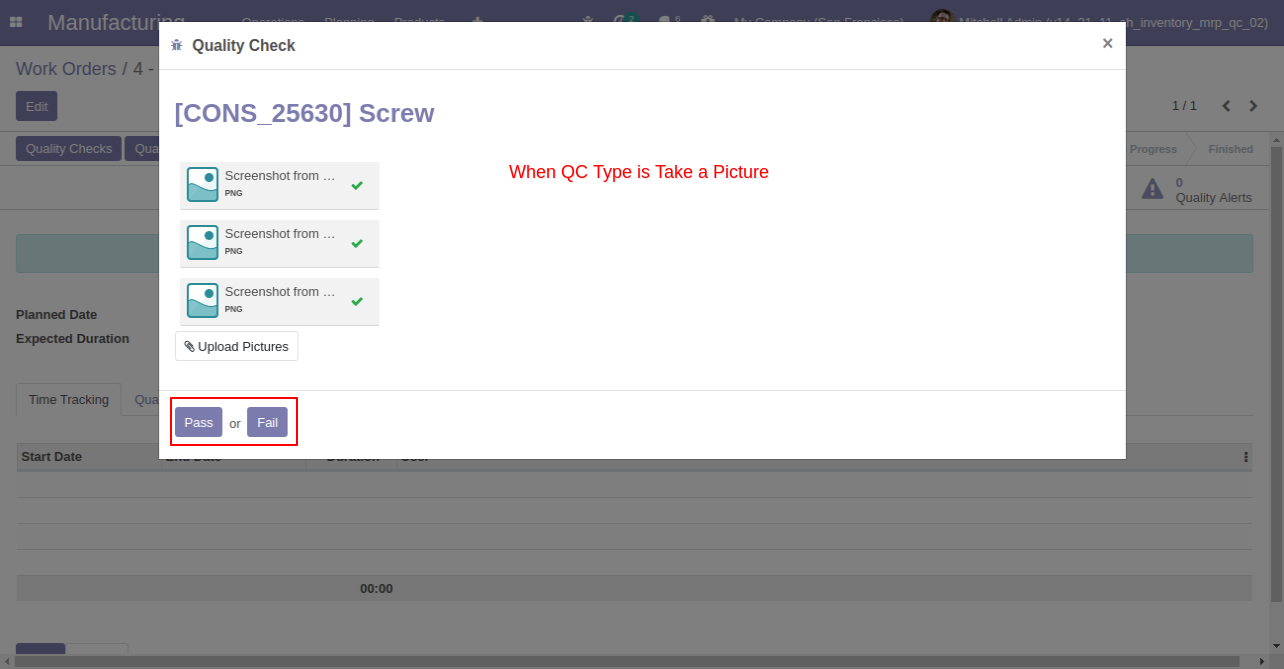
Here users have buttons for 'Quality Alert' and one tab also.
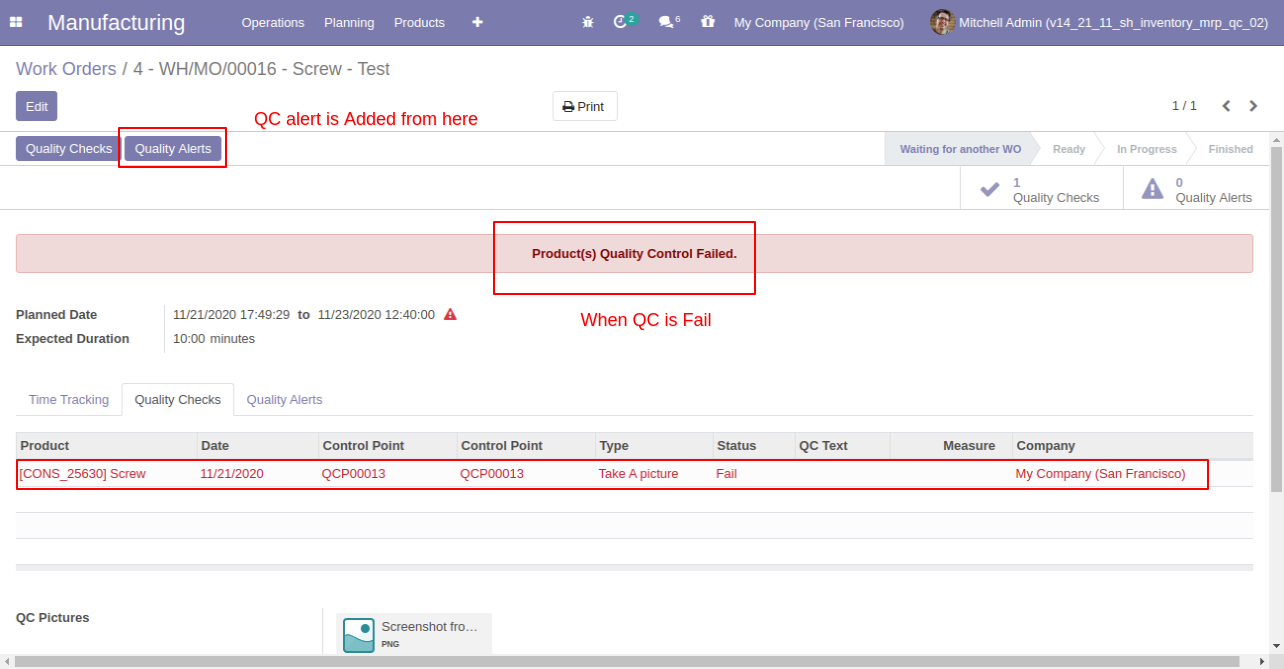
Quality Alert Wizard where you can create a quality alert for that product.
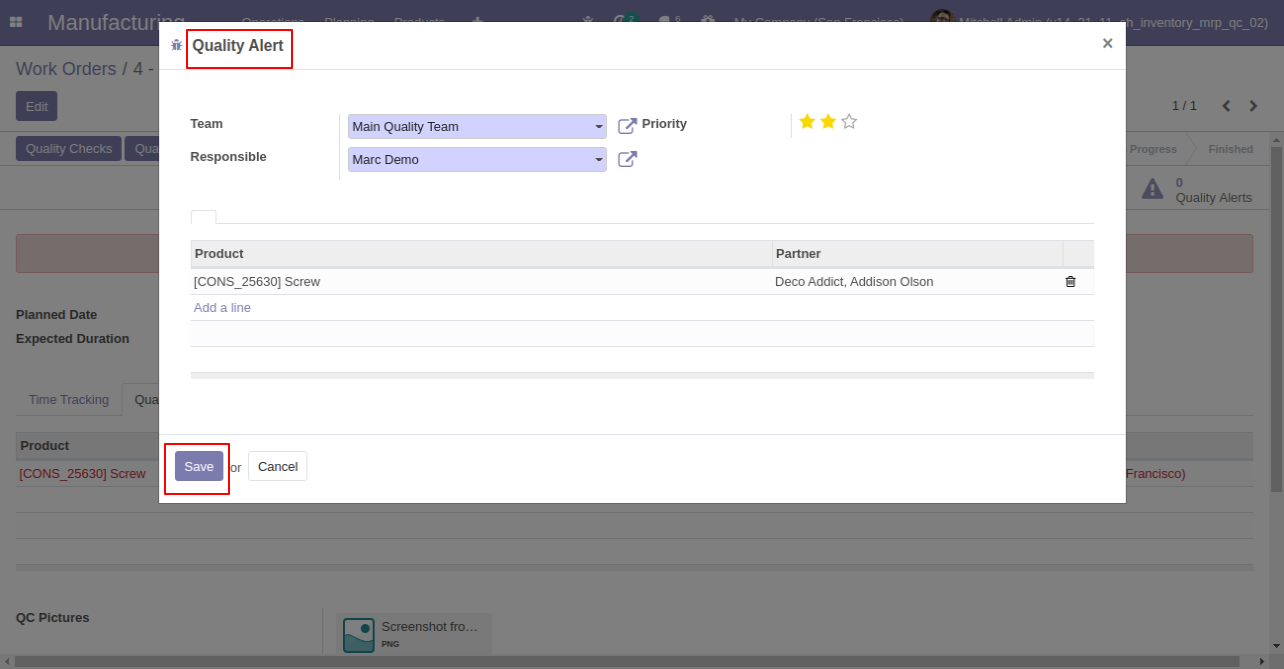
After save that you can see that product in the 'Quality Alert' tab and the smart button also.
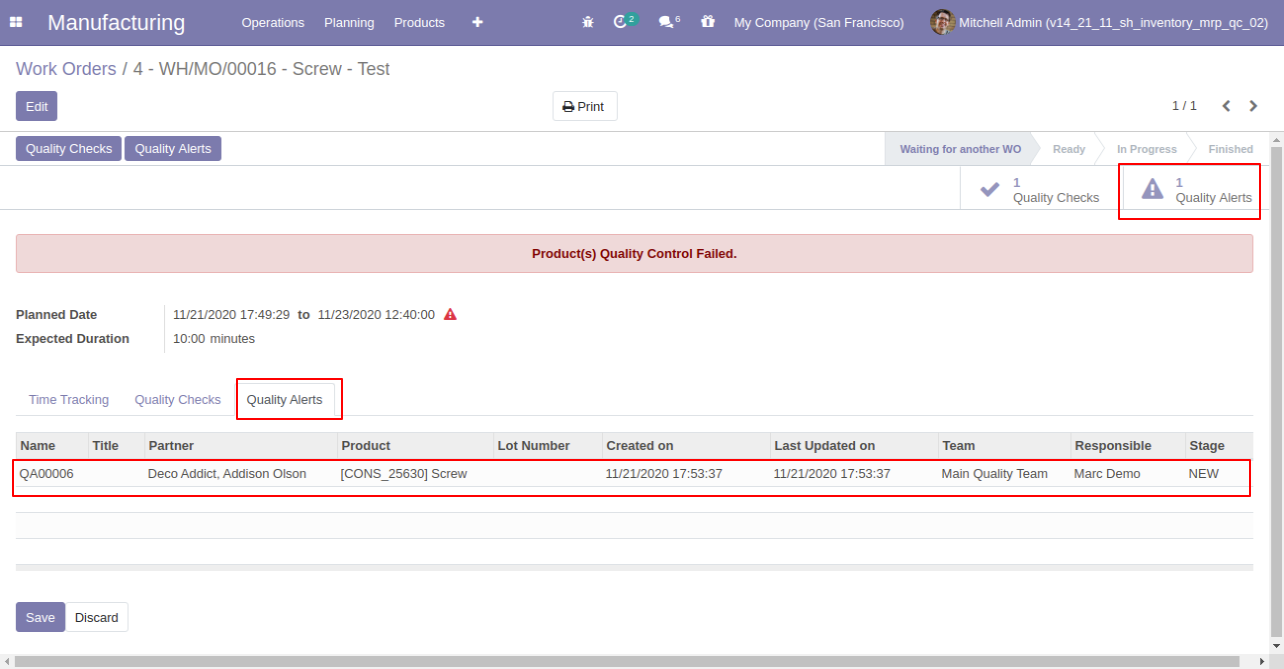
Work Order Quality Alerts Menu and Tree View.
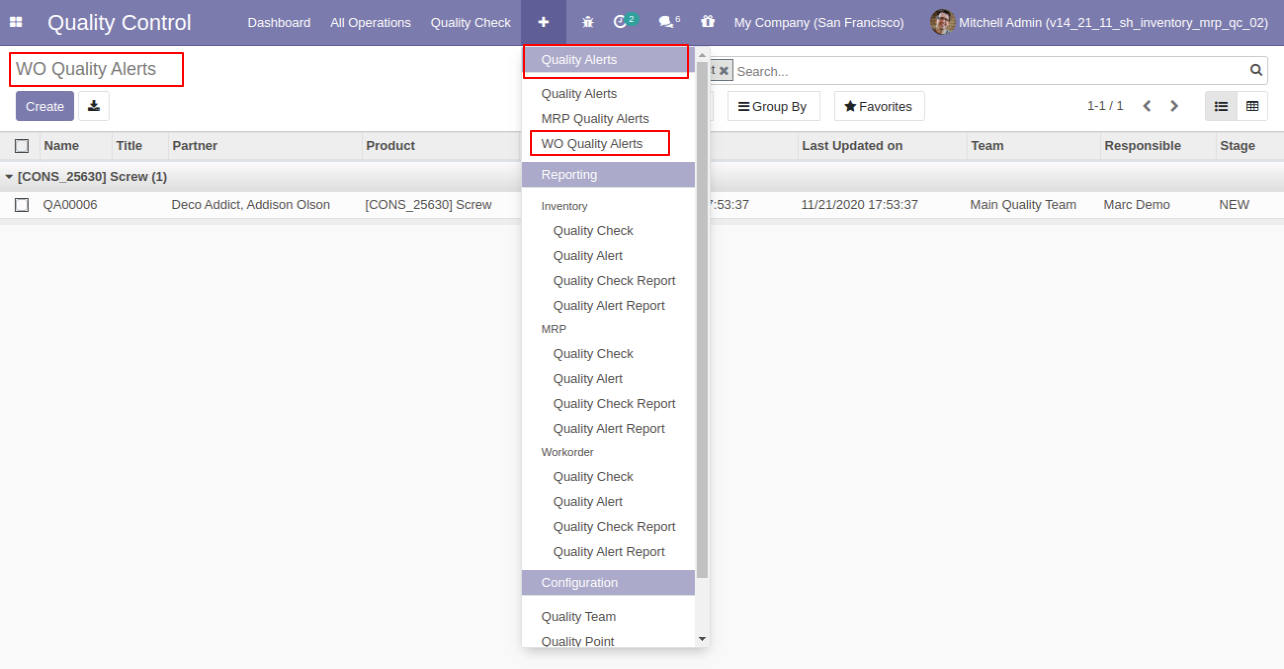
Work Order Quality Alerts Form View.
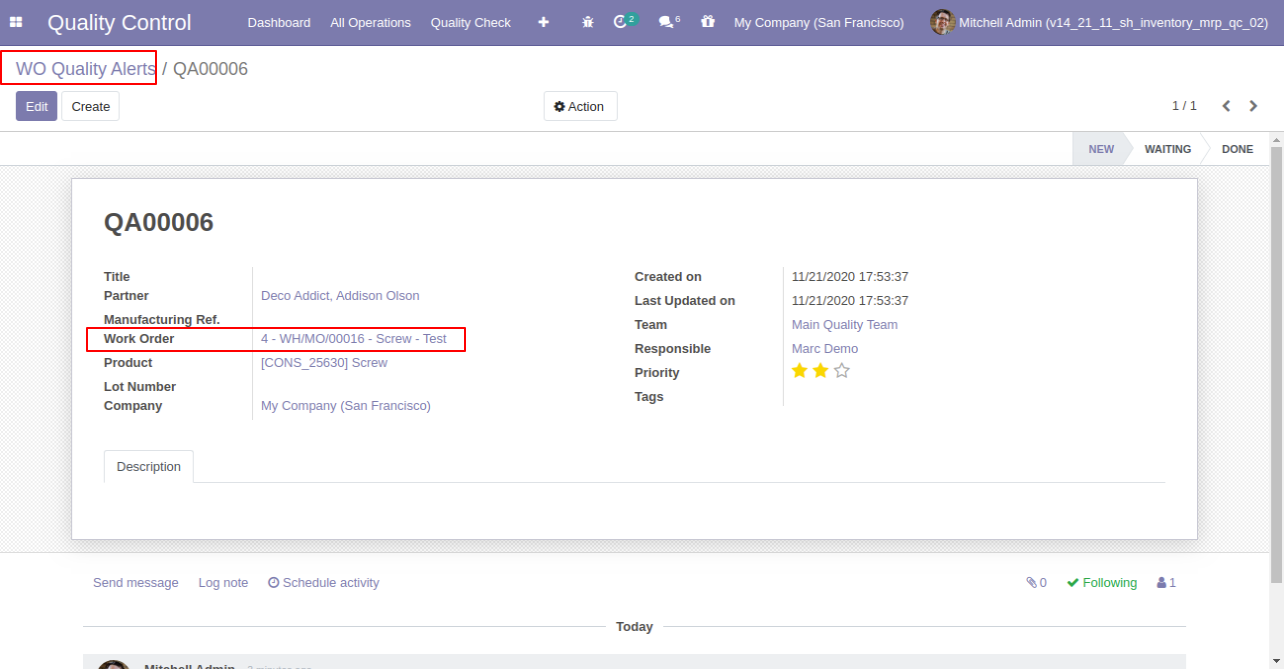
Work Order Pending QC Menu and Tree View.
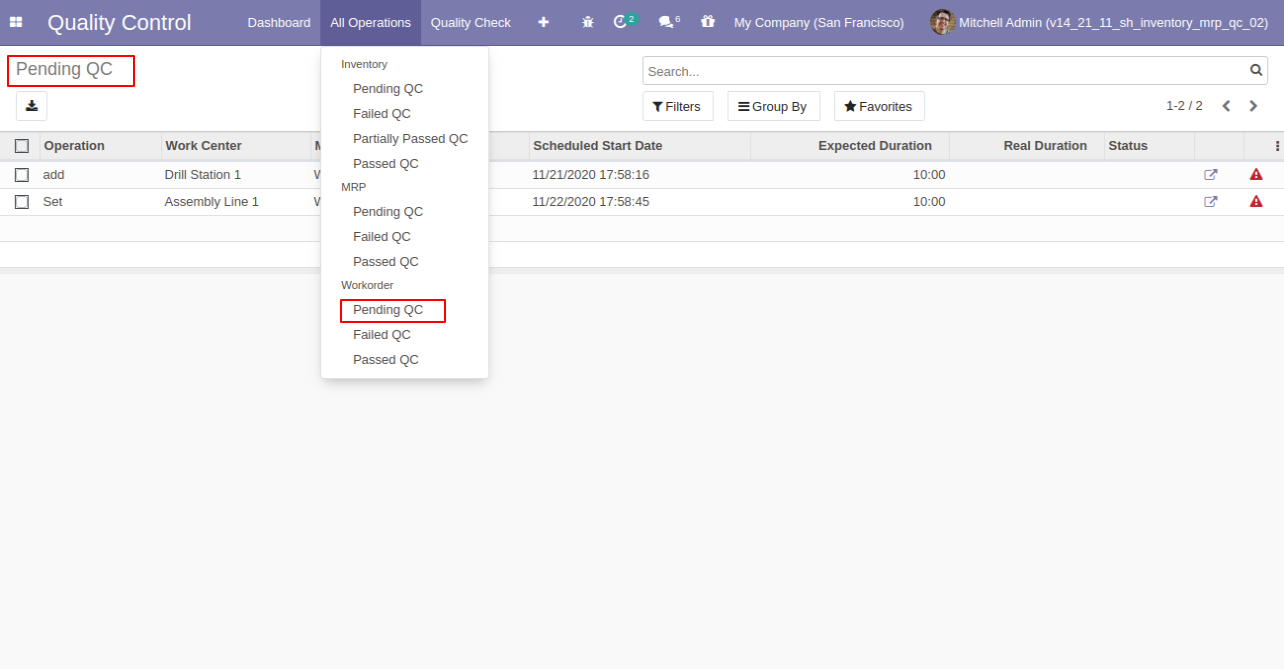
Work Order Failed QC Menu and Tree View.
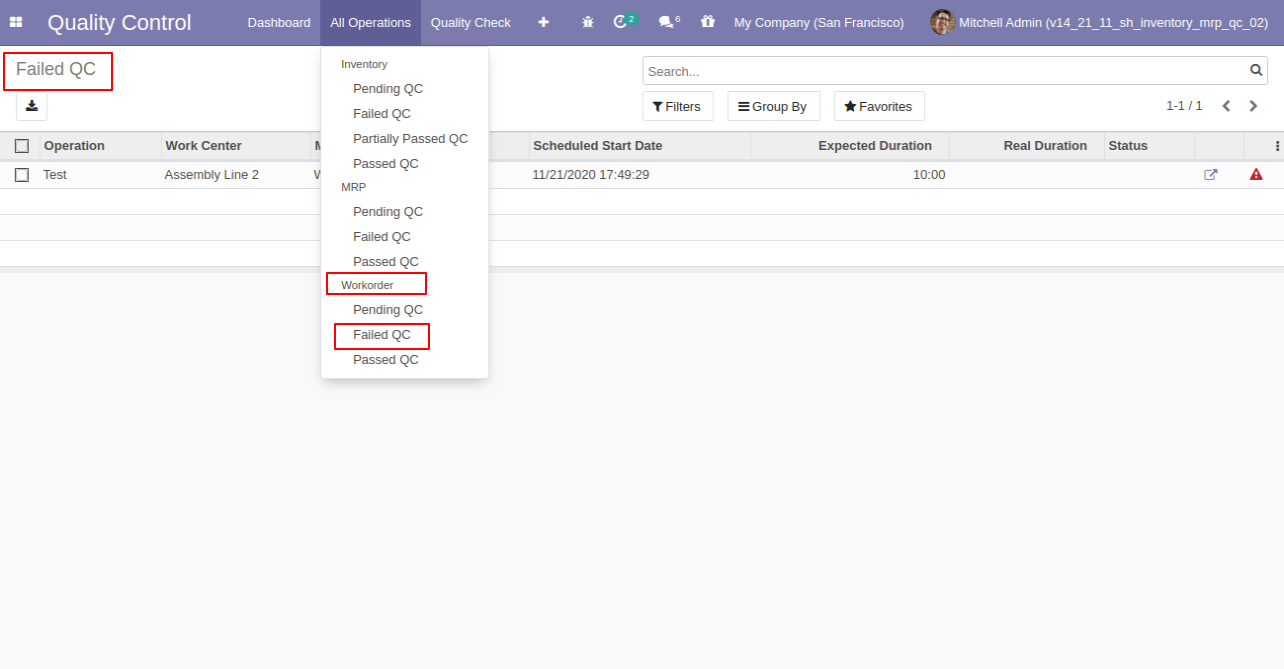
Work Order Passed QC Menu and Tree View.
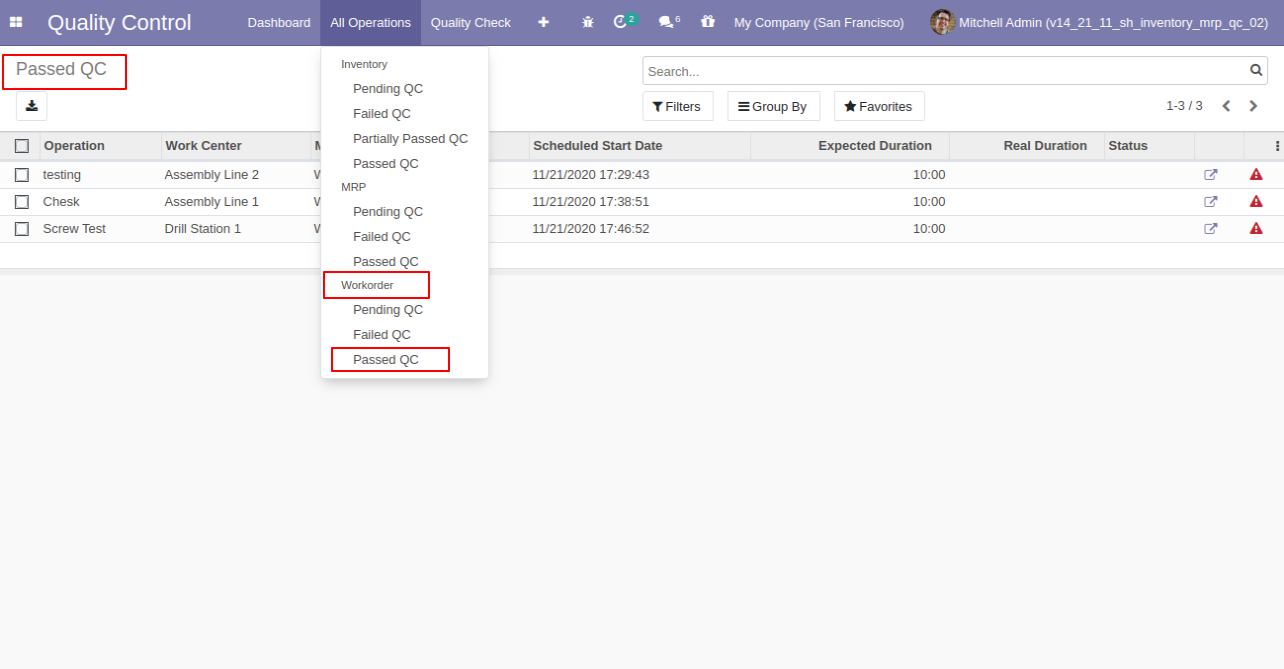
Work Order Quality Check Menu and Tree View.
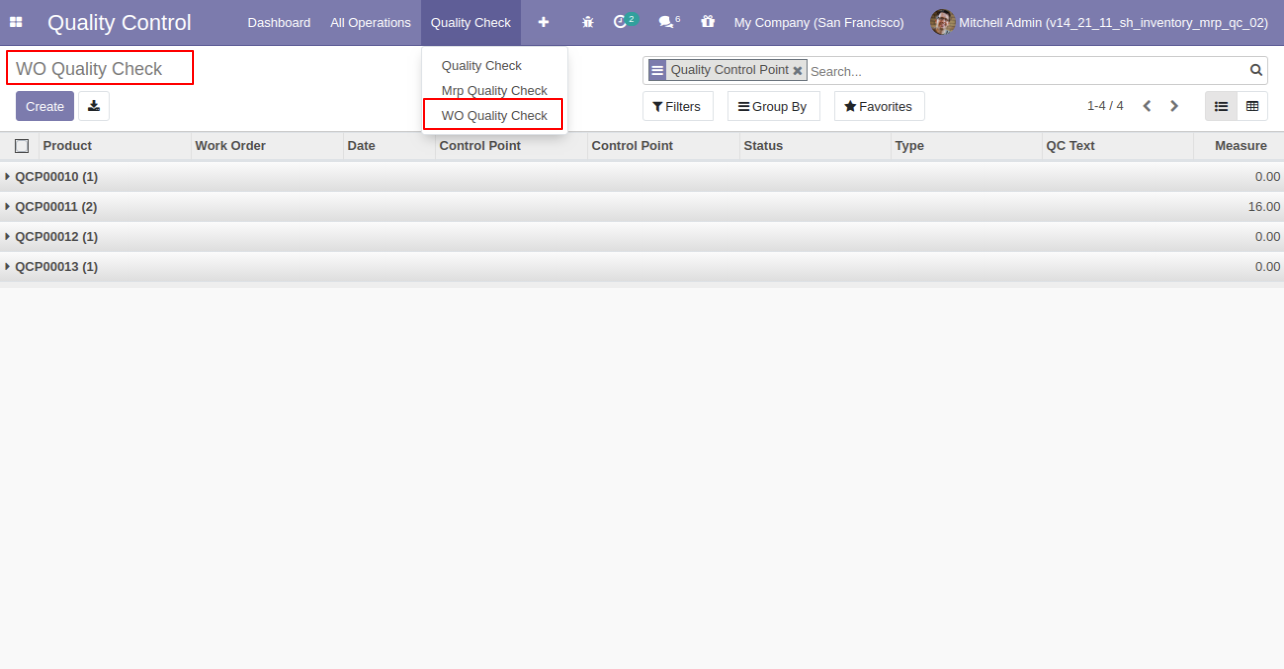
Work Order Quality Check Form View. Where you can see the work order detail and type of QC.
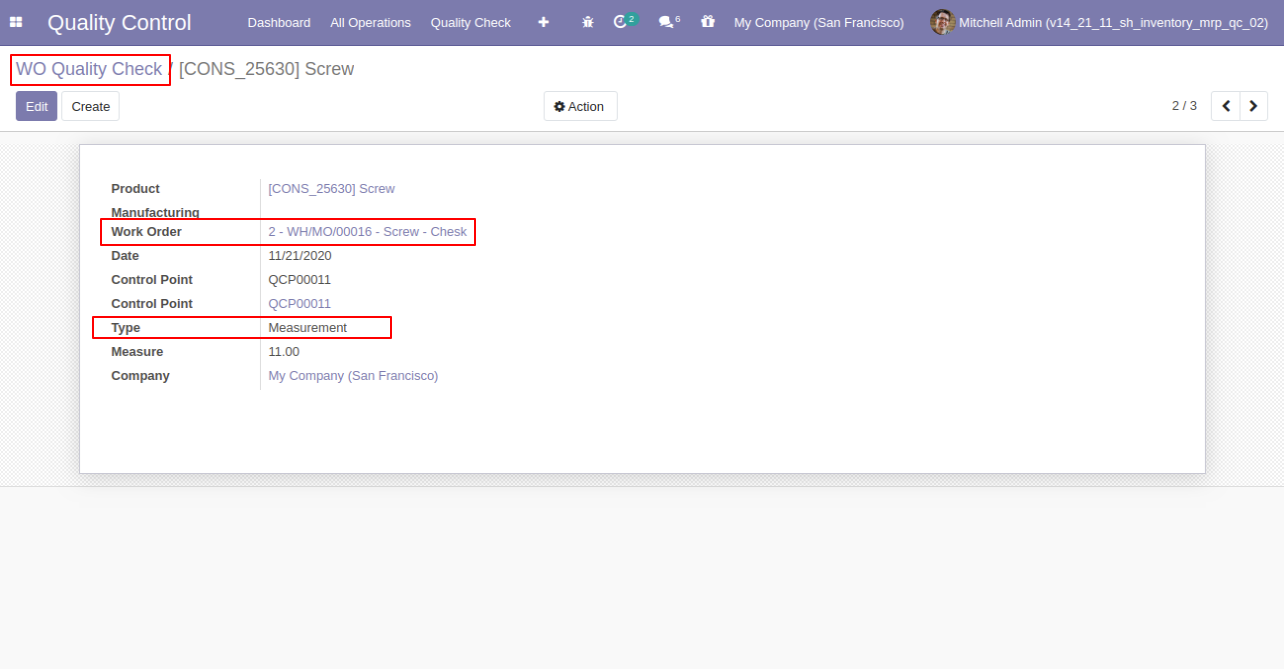
Work Order Quality Check Analysis Report Menu and View.
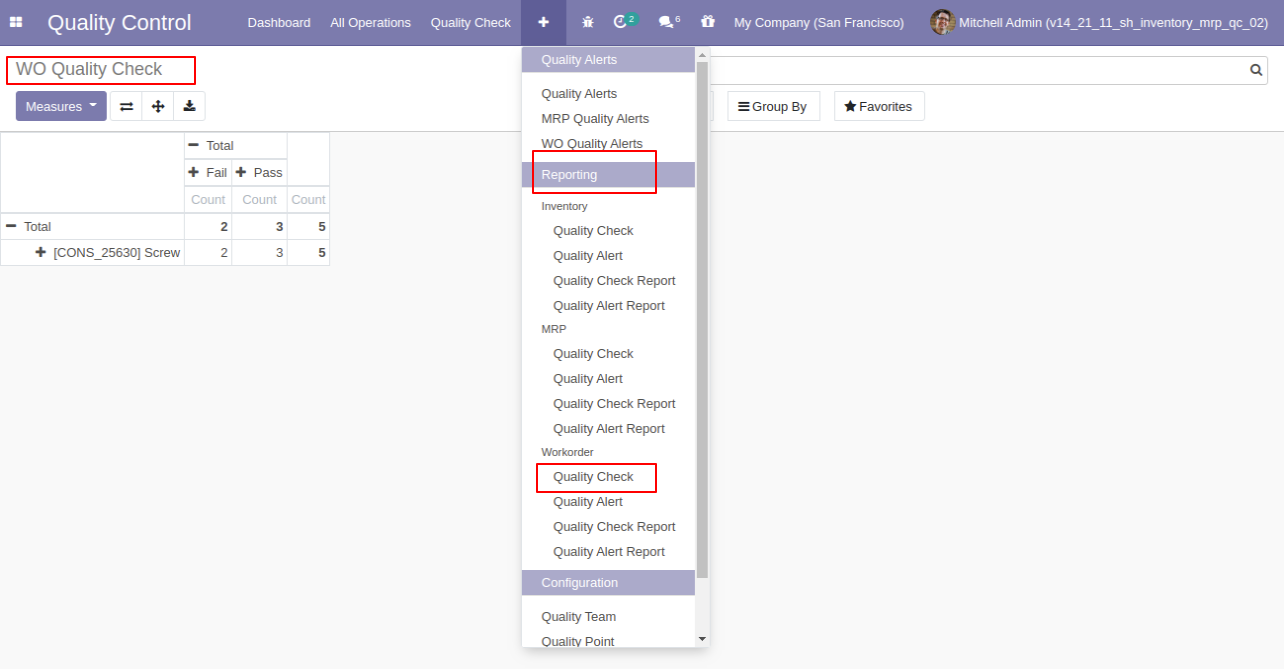
Work Order Quality Alerts Analysis Report Menu and View.
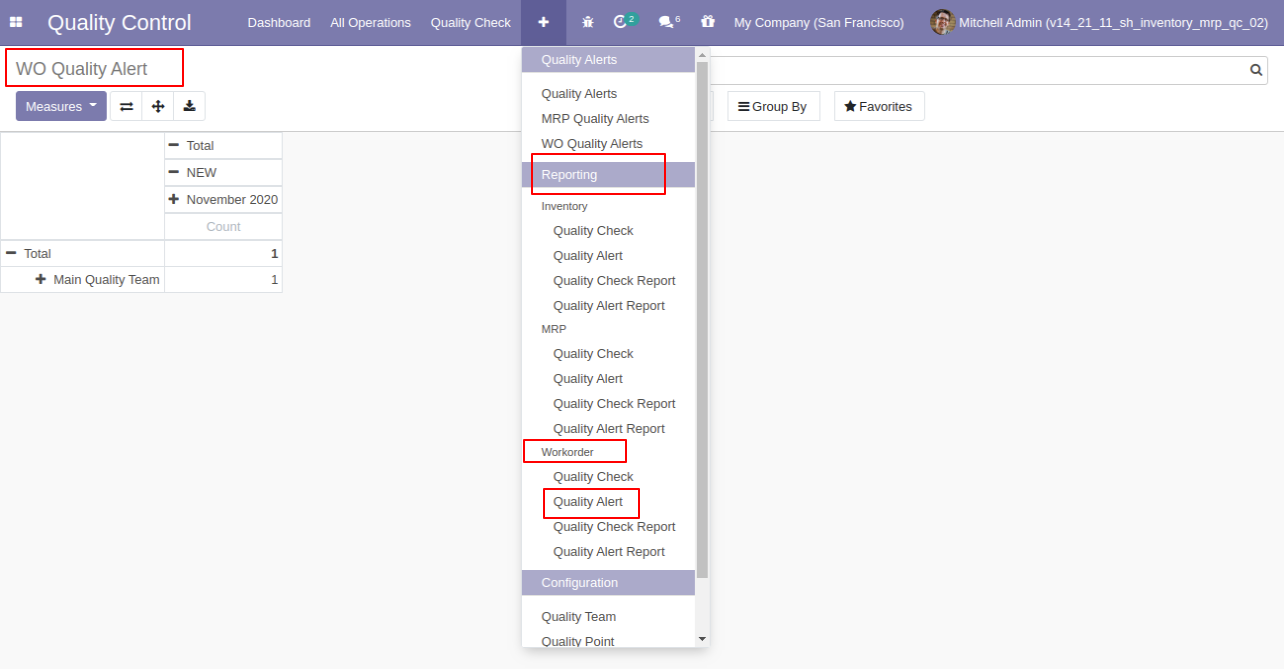
'Work Order Quality Check Report' action for print QC report in pdf format.
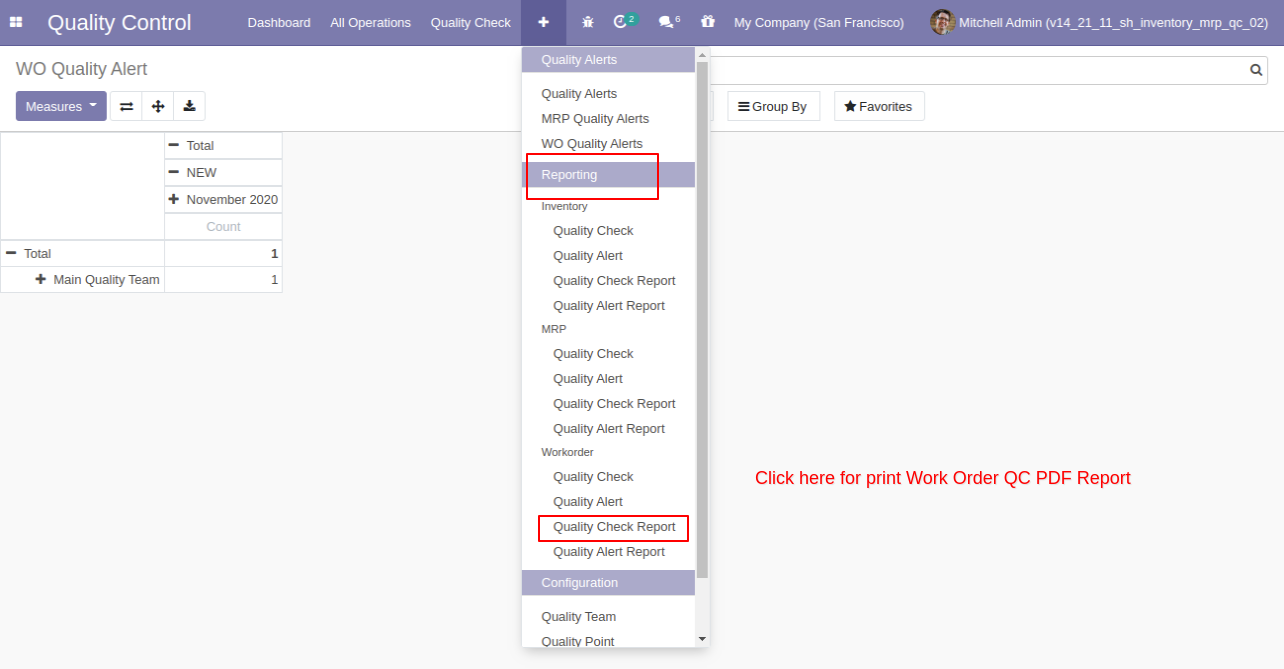
After clicking on that option this wizard will popup, where you can print reports with the group by, stages or start and end date filters.
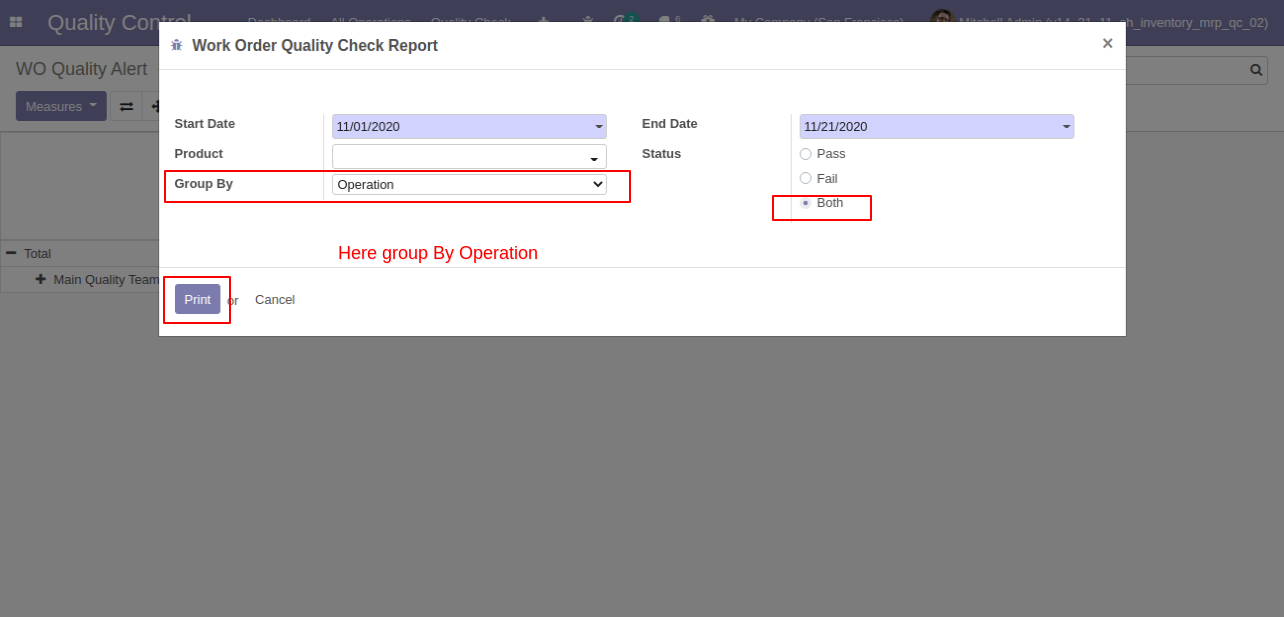
This quality check pdf report is generated with the group by operation.
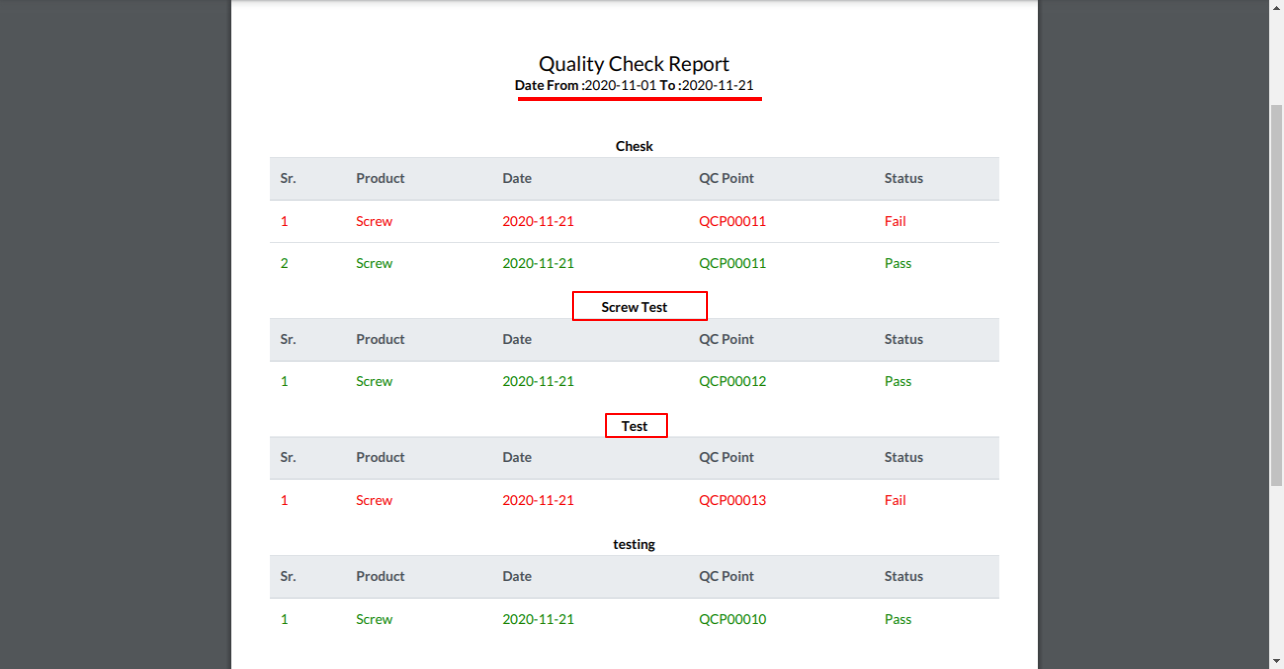
Select 'Product' in the group by.
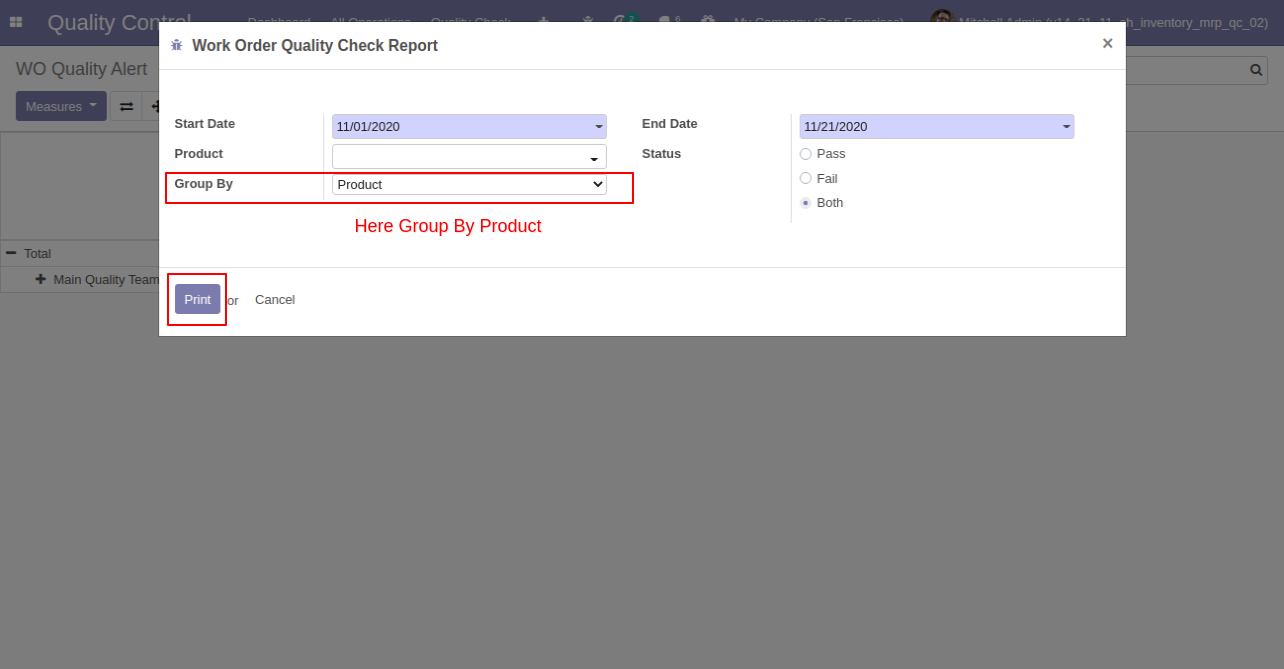
'Quality check PDF report group by 'Product'.
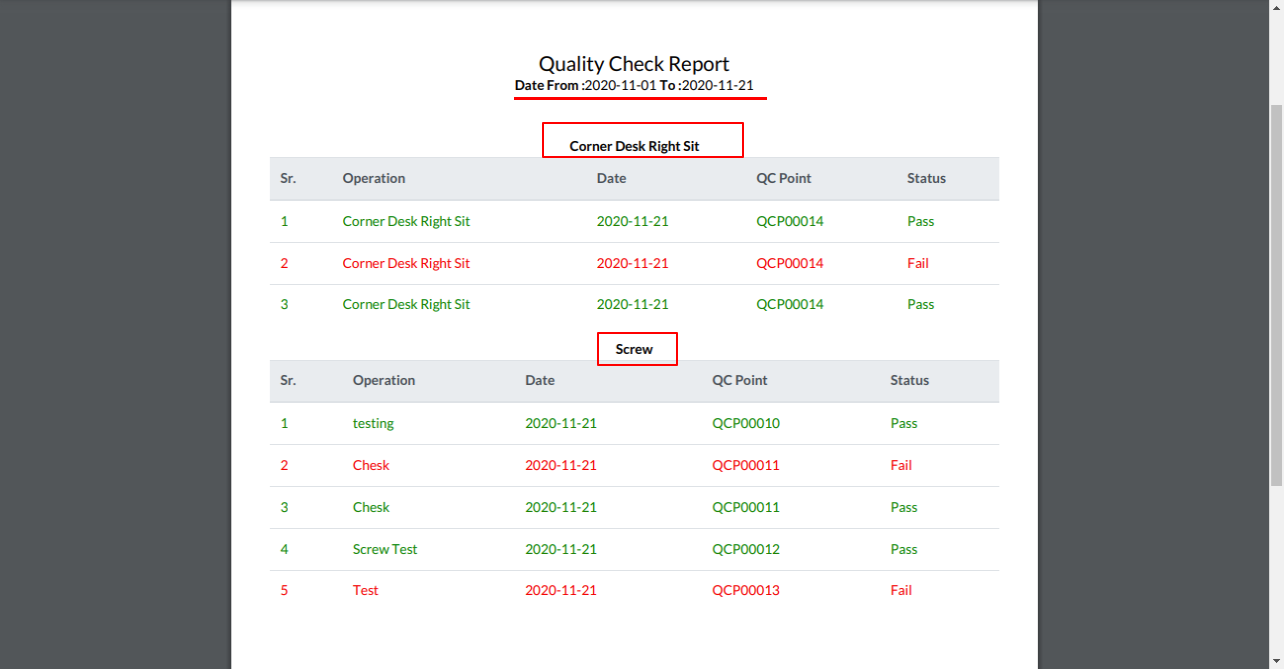
Work Order Quality Alert Pdf report action.
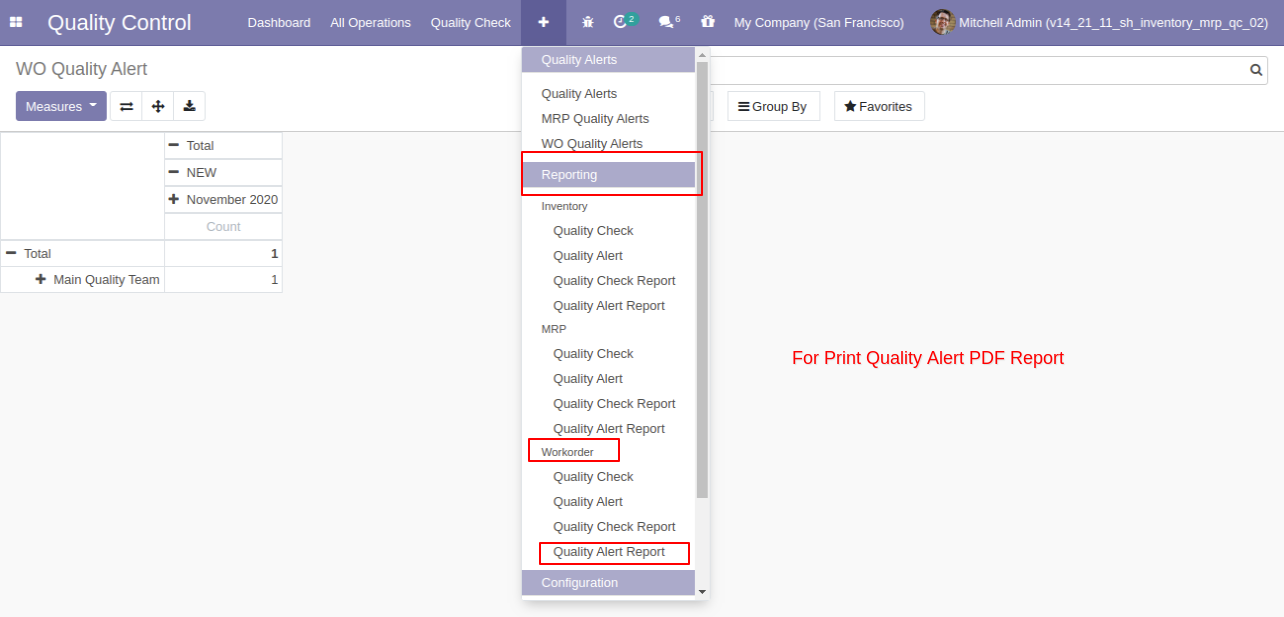
'Quality Alert Report' by-product and responsible person with the stage.
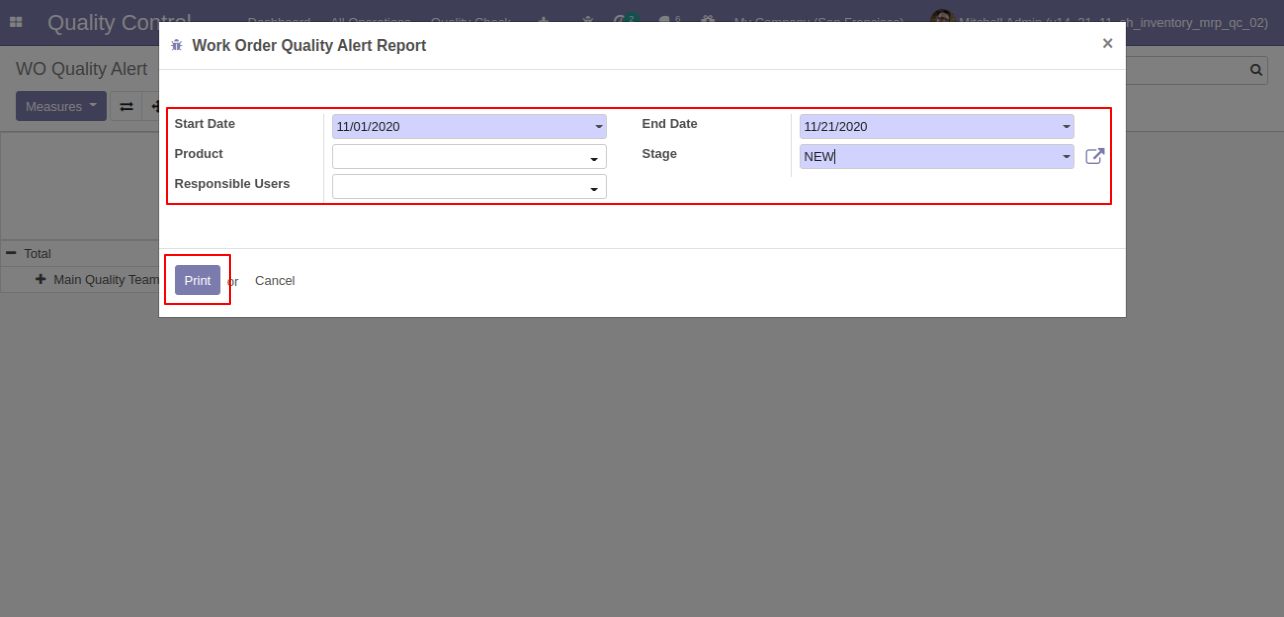
Work order quality alert pdf report generate with only stage 'New'.
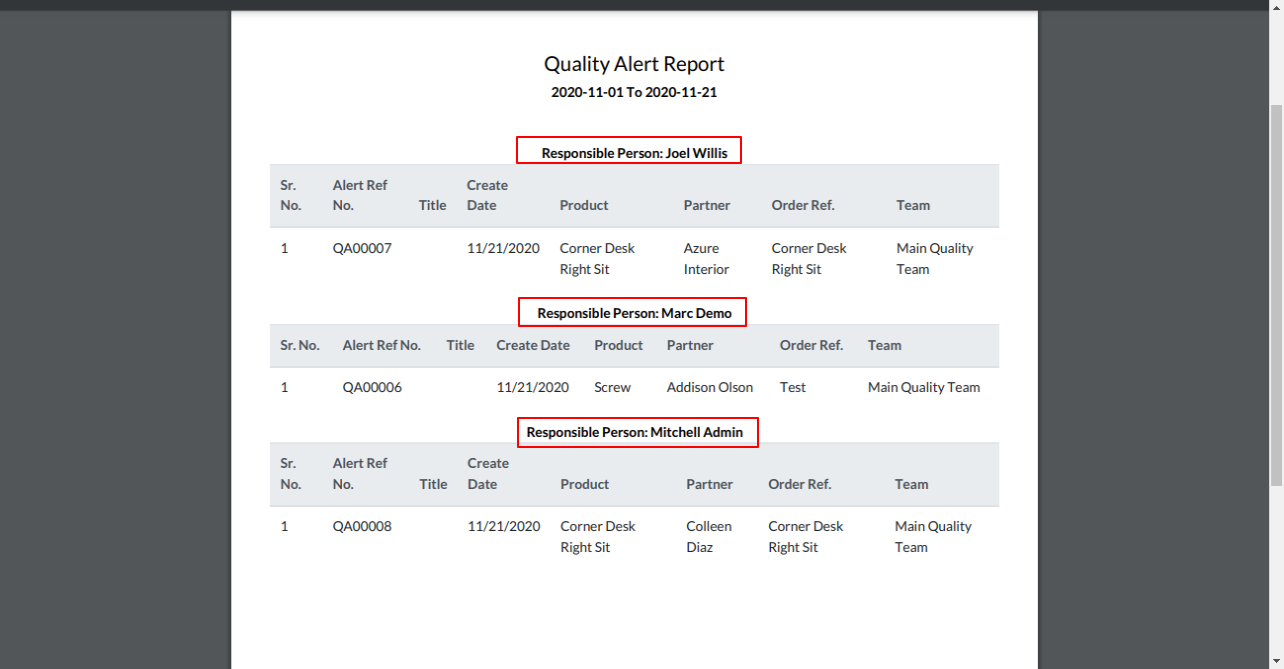
Version 14.0.1 | Released on : 29thSeptember 2022
- Yes, this app works perfectly with Odoo Enterprise (Odoo.sh & Premise) as well as Community.
- Yes, This app is compatible with Odoo's Multi-Company Feature.
- Please Contact Us at sales@softhealer.comto request customization.
- Yes, we provide free support for 100 days.
- You can set only a single quality point per product.
- Yes, you will get free update for lifetime.
- No, you don't need to install addition libraries.
- Yes, You have to download module for each version (13,14,15) except in version 12 or lower.
- No, We do not provide any kind of exchange.